Microfiltration Membrane: Principles and Applications
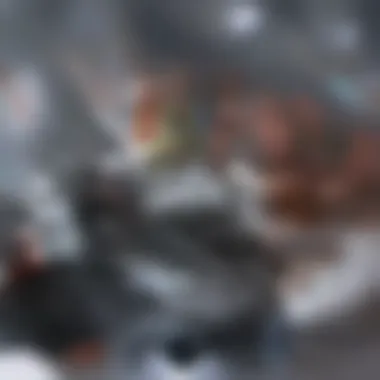
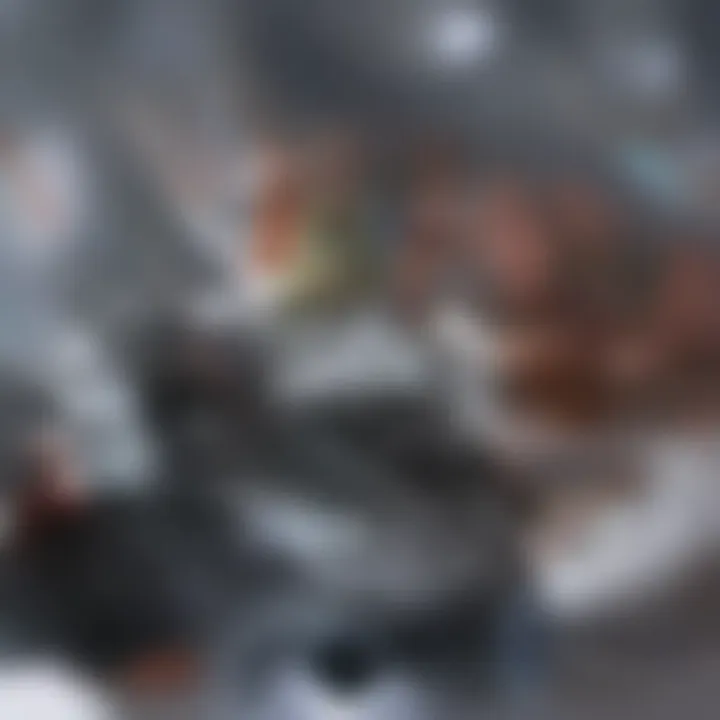
Intro
Microfiltration membranes play a crucial role in various sectors, including water treatment, pharmaceuticals, and food processing. These membranes are designed to separate particles based on size and can effectively remove bacteria and larger particles from liquids. This comprehensive analysis aims to present the fundamental principles behind microfiltration membranes, explore their applications in different industries, and highlight recent advancements.
Understanding these membranes is essential due to their increasing relevance in addressing global challenges such as water scarcity and contamination. As we delve into the intricacies of microfiltration technology, we will provide insights into manufacturing processes, innovative materials, and the associated environmental implications. Research indicates a growing trend towards improving efficiency and sustainability in membrane technology. This article serves as a guiding resource for students, researchers, and industry professionals interested in the latest developments.
Methodologies
Studying microfiltration membranes involves various research techniques and methodologies that enhance our understanding of their functionality and performance.
Description of Research Techniques
Research on microfiltration membranes often utilizes both experimental and theoretical approaches. Experimental methods are essential for testing membrane performance under controlled conditions. Techniques such as flux measurement, fouling characterization, and permeability tests are commonly employed.
Theoretical frameworks are also critical. Computational fluid dynamics (CFD) simulations can predict how membranes perform in real-world conditions. Alongside these, literature reviews help to compile existing findings and identify gaps in the research.
Tools and Technologies Used
A range of tools and technologies are employed to study microfiltration membranes effectively:
- Scanning Electron Microscopy (SEM): Used for examining membrane surface morphology.
- Atomic Force Microscopy (AFM): Provides detailed topographical analysis.
- Dynamic Light Scattering (DLS): Measures particle sizes in solutions.
- Ultrafiltration units: Allow for the practical assessment of membrane separation performance.
Each methodology and tool aids in understanding how microfiltration membranes can be improved, both in terms of design and material selection.
Discussion
Comparison with Previous Research
The evolution of microfiltration technology has been notable over the past few decades. Compared to earlier studies, recent research emphasizes sustainable practices and the integration of advanced materials. Traditional polymeric membranes have undergone transformations, with the introduction of composite and ceramic membranes leading to enhanced performance.
Theoretical Implications
The implications of advancements in microfiltration membranes extend beyond just technical improvements. They challenge existing theoretical models that have been applied in filtration processes. For instance, increased understanding of fouling mechanisms has altered how researchers approach membrane cleaning and maintenance protocols.
As we analyze these changes, it is evident that microfiltration membranes are not merely filtration devices but integral components of complex systems aimed at sustainability and efficiency.
"Understanding the principles of microfiltration technology is vital for addressing contemporary global issues effectively."
Prologue to Microfiltration Membranes
Microfiltration membranes have emerged as a vital tool in various sectors, drawing attention for their unique capabilities in filtering particles and microorganisms. Understanding their roles and applications is essential for professionals and researchers in fields like water Treatment, biotechnology, and food safety.
Microfiltration is a process that operates on a physical principle, allowing substances to pass through a membrane while blocking larger particles. This function is of great significance in ensuring the purity of water and other solutions. The relevance of studying microfiltration membranes extends beyond mere filtration. It encompasses optimization of processes, enhancement of efficiency, and the improvement of quality in numerous applications.
Definition and Function
Microfiltration membranes are porous materials that separate particles based on size. Typically, these membranes have a pore size ranging from 0.1 to 5 micrometers, allowing for the effective removal of bacteria, suspended solids, and some viruses. The function of these membranes is not limited to filtration alone; they also play a crucial role in concentration processes, clarification, and in aspects of separation technology. Their significance lies in the balance they provide between filtering unwanted particles and allowing desired substances to pass, which is crucial in ensuring product quality in many industries
Historical Background
The development of microfiltration technology dates back to the early 20th century. Initially, these methods were employed in laboratory environments before being applied at an industrial scale. As technological advancement continued, and the demand for cleaner water and higher quality products surged, microfiltration membranes became more widely utilized. Key innovations in materials science led to the introduction of polymeric and ceramic membranes, greatly enhancing the effectiveness and durability of microfiltration systems. Over the years, we have seen adaptations in the types of materials used, ranging from polysulfone to polyvinylidene fluoride. This evolution laid the groundwork for the sophisticated membranes we rely on today.
Microfiltration is not merely a technological process; it revolutionizes how industries manage purity and quality across numerous applications.
Principles of Microfiltration
Microfiltration is an essential process in various industries, specifically those focusing on the purification and separation of solutions. Understanding the principles of microfiltration helps in optimizing membrane usage and ensuring efficient operations. This section will explore the mechanisms involved in microfiltration, along with factors that affect the efficiency of filtration processes.
Mechanisms of Filtration
Microfiltration operates primarily through two mechanisms: size exclusion and adsorption. Size exclusion involves the separation of particles based on their size while allowing smaller molecules, such as water and some dissolved solids, to pass through the membrane. This is particularly significant when removing solids, such as bacteria and sediment, from liquids.
Adsorption plays a role in enhancing the efficacy of the filtration process. Membranes can be modified to attract specific contaminants, improving the overall quality of the filtrate. For instance, membranes can be engineered to have positively or negatively charged surfaces, allowing them to selectively adsorb specific ions or contaminants.
"The combination of size exclusion and adsorption allows microfiltration to achieve high selectivity and efficiency in separating various substances."
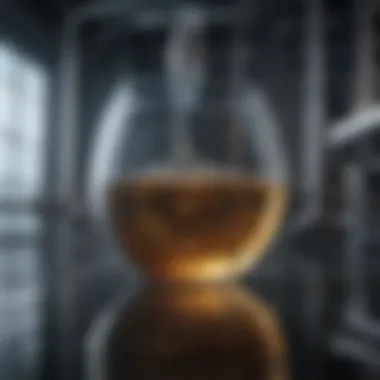
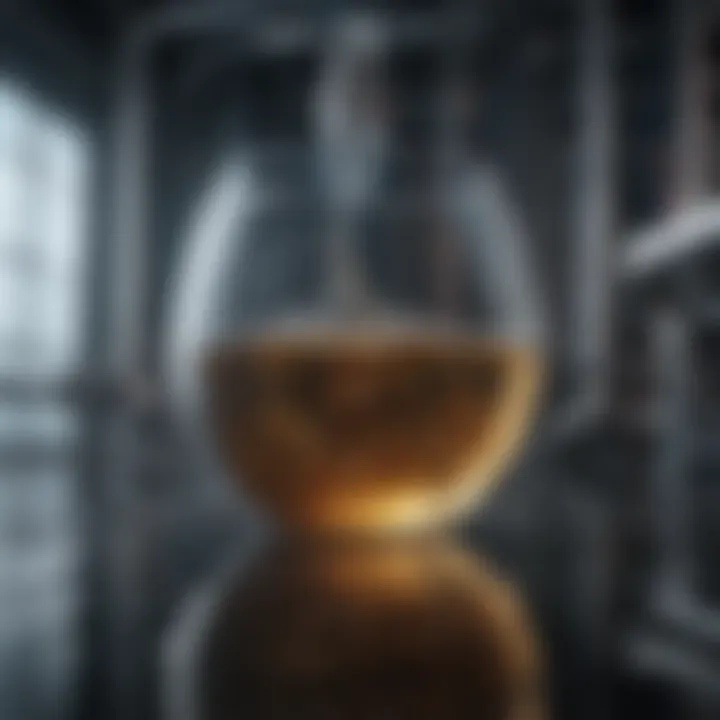
The success of this process largely depends on the membrane material, pore size, and the nature of the solution being filtered. Polymeric membranes typically exhibit better resistance to fouling while ceramic membranes offer stronger mechanical properties and thermal stability.
Factors Affecting Filtration Efficiency
Filtration efficiency in microfiltration is influenced by several key factors that warrant consideration:
- Membrane Properties: The material, pore size, and surface charge of the membrane can significantly affect how substances are filtered. Smaller pore sizes generally improve the ability to retain larger particles but may contribute to higher resistance and fouling.
- Feed Characteristics: The nature of the feed solution, including viscosity, concentration of particulates, and pH, plays a crucial role. Solutions with a high concentration of solids may lead to quicker fouling of membranes, reducing efficiency over time.
- Operating Conditions: Parameters such as transmembrane pressure, temperature, and flow rate impact filtration performance. Higher transmembrane pressure typically increases the flux but may also enhance fouling if not managed carefully.
- Cleaning Methods: Regular maintenance and appropriate cleaning methods can help restore membrane performance. Different fouling types, such as organic, inorganic, or biological, require specific cleaning techniques.
In summary, the principles of microfiltration not only underline the scientific aspects but also emphasize operational management. Knowing the mechanisms and factors affecting filtration efficiency is vital for anyone working in related fields. This understanding aids in improving membrane design and application across diverse industrial sectors.
Types of Microfiltration Membranes
Microfiltration membranes play a crucial role in a variety of applications, necessitating a deep understanding of their types. The distinction among these membranes enables engineers and researchers to select the appropriate solution for specific filtration needs. Selecting the right type can lead to improved efficiency, reduced operational costs, and better overall performance. In this section, we will explore the primary types of microfiltration membranes: polymeric, ceramic, and composite membranes.
Polymeric Membranes
Polymeric membranes are the most widely used type in microfiltration applications. They are generally made from organic polymers such as polysulfone, polyethersulfone, and polyvinylidene fluoride. These materials provide a balance of performance and cost-effectiveness, leading to their prevalence in the market.
The benefits of polymeric membranes include their lightweight nature and flexible characteristics, allowing easy installation. They exhibit high permeability, which results in lower energy consumption. Moreover, the manufacturing processes for these membranes are well-established, making it easier to scale production to meet varying demands.
However, the performance of polymeric membranes can be hindered by fouling. This occurs when particles accumulate on the membrane surface, leading to a decline in efficiency. This is a known challenge in various applications like water and wastewater treatment. Continuous research aims to develop surface modifications to minimize fouling.
Ceramic Membranes
Ceramic membranes distinguish themselves with their robust and durable nature. Typically composed of inorganic materials such as alumina or zirconia, they can withstand harsh chemical environments and high temperatures. This makes them suitable for demanding applications which polymeric membranes cannot endure.
The key advantage of ceramic membranes is their longevity. They typically have a longer lifespan compared to polymeric membranes, which reduces the frequency of replacement. Additionally, they demonstrate greater resistance to fouling, allowing them to maintain performance over time. Despite these benefits, ceramic membranes are often costlier to manufacture. This may limit their use to applications where performance justifies the expense.
Composite Membranes
Composite membranes offer a unique advantage by combining elements of both polymeric and ceramic membranes. These structures typically have a thin layer of a polymer material supported by a porous ceramic or polymeric substrate. This marriage of materials can optimize performance, durability, and cost.
One of the major benefits of composite membranes is the ability to tailor their properties for specific applications. For example, the thinness of the top layer can enhance permeability, while the robust substrate provides structural integrity.
However, the complexity of manufacturing composite membranes may introduce challenges in quality control. Ensuring consistent performance can be an issue due to potential variations in the layers.
"The types of microfiltration membranes dictate the suitability for specific applications, impacting efficiency and overall cost."
In summary, understanding the types of microfiltration membranes is essential for selecting the right option for the intended application. Each type has its benefits and limitations. An informed choice will ultimately enhance performance while addressing challenges encountered in various sectors.
Manufacturing Processes
The manufacturing processes of microfiltration membranes play a crucial role in determining their performance and applicability across various sectors. Understanding these processes allows for the enhancement of membrane features, such as permeability, selectivity, and fouling resistance. The choice of a specific manufacturing technique can significantly influence the functional properties of the membrane, which in turn affects its efficiency in real-world applications. Hence, this section will delve into the primary methods used for producing microfiltration membranes, exploring their specific benefits and necessary considerations.
Phase Inversion Techniques
Phase inversion is one of the most widely used methods for fabricating polymeric membranes. This technique involves the transition of a polymer solution into a solid membrane structure through a phase separation mechanism. The process typically begins with the dissolution of a polymer in a suitable solvent. Upon cooling or adding a nonsolvent, the polymer precipitates and forms a porous structure. The major benefit of this method is its versatility; it allows for the adjustment of membrane properties by altering factors such as the polymer type, solvent choice, and phase inversion conditions. However, controlling the membrane's final morphology can be challenging as the membrane's pore size and distribution will directly influence its filtering capabilities.
Sol-gel Processes
The sol-gel process is another innovative approach to producing microfiltration membranes, particularly those made of ceramic materials. This method starts with the formation of a sol, a colloidal solution of solid particles in liquid. The sol eventually transforms into a gel through hydrolysis and polycondensation reactions. Subsequently, heat treatment solidifies the gel into a dense, porous structure. One major advantage of the sol-gel process is the ability to create membranes with highly uniform pore sizes, enhancing performance. However, the complexity of this technique, along with the requirement for precise control over the chemical reactions involved, can make it less accessible for larger-scale production.
3D Printing of Membranes
The advent of 3D printing technology has opened up new possibilities in membrane manufacturing. This technique enables the precise layering of materials to create complex membrane architectures, tailored for specific applications. 3D printing can utilize a variety of materials, including polymers and ceramics, allowing for customization in terms of pore size and structural configuration. The main advantage of 3D printing is the capacity for rapid prototyping and production of membranes. It can also facilitate the design of membranes with integrated functions or unique surface properties. Nonetheless, challenges remain regarding scalability and balancing printing speeds with the desired resolution and accuracy of the final product.
"Advancements in manufacturing methods not only enhance membrane performance but also broaden their applications across diverse industries."
In summary, the manufacturing processes of microfiltration membranes are paramount to their functionality and effectiveness. Each method—phase inversion, sol-gel processes, and 3D printing—offers distinct benefits and challenges, shaping the future landscape of membrane technology.
Applications of Microfiltration Membranes
Microfiltration membranes have gained prominence in various sectors due to their ability to separate particles based on size. This section elucidates the significant applications of microfiltration membranes, showcasing how they improve processes and outcomes across different industries. Each application has its unique benefits and characteristics that enhance efficiency, safety, and product quality.
Water Treatment
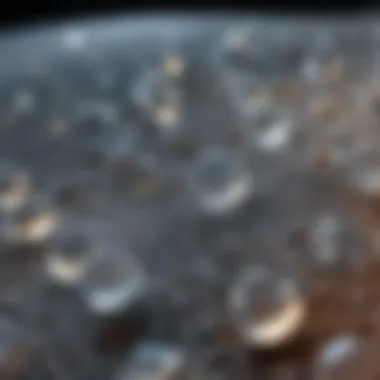
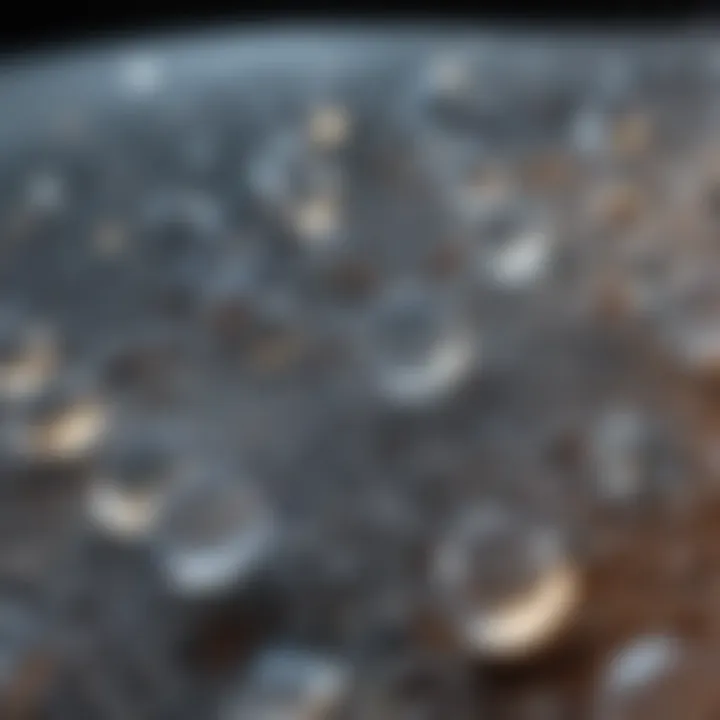
Microfiltration plays a critical role in water treatment processes. One of its foremost advantages is the removal of suspended solids, bacteria, and protozoa from water. This ensures that the treated water meets regulatory standards for safe consumption. The effectiveness of microfiltration membranes is notable in producing potable water from surface water sources.
Furthermore, microfiltration membranes are utilized in wastewater treatment, aiding in the recycling of water. By separating solids from liquid waste, these membranes reduce the environmental impact of effluents. In many cases, they also help recover valuable resources from wastewater, thereby contributing to sustainability efforts.
The advancement of microfiltration technology has also led to its integration with other techniques, such as reverse osmosis and UV treatment, strengthening the overall effectiveness of water treatment systems. The ability to address contaminants at the micron scale furthers the capabilities of water utilities to ensure public health.
Food and Beverage Industry
In the food and beverage sector, microfiltration membranes are essential for ensuring product quality and safety. They provide a means to filter out microorganisms, such as yeast and bacteria, from liquids like fruit juices and beer. This not only prolongs the shelf life of products but also maintains their sensory attributes.
For example, many wineries utilize microfiltration to clarify wine before bottling. This step is vital to remove unwanted particles without the use of harsh chemicals. By employing microfiltration, manufacturers can create products that are both high-quality and free from additives.
Moreover, the dairy industry benefits from microfiltration in milk processing. It helps in concentrating proteins and fat while removing contaminants. This leads to higher value-added products, such as yogurt and cheese, enhancing profitability for producers.
Biotechnology and Pharmaceuticals
The field of biotechnology and pharmaceuticals relies heavily on microfiltration for purifying biological products. Microfiltration membranes serve a dual purpose: they remove unwanted cells and debris while concentrating desired biomolecules. This is particularly critical in processes like protein purification and vaccine production.
In biopharmaceutical manufacturing, maintaining sterile conditions is paramount. Microfiltration is used to ensure that solutions are free from pathogens and particulates. This is crucial not only for efficacy but also for regulatory compliance. Manufacturers must adhere to strict guidelines, and microfiltration assists in meeting these requirements efficiently.
Additionally, microfiltration is applied in the fermentation process, where it helps maintain culture conditions by removing spent cells and maximizing yield. This dual role enhances both the quality of the end products and the efficiency of production workflows.
"Microfiltration is an invaluable tool for industries, enhancing product safety and quality while supporting sustainable practices."
In summary, applications of microfiltration membranes span crucial sectors, impacting water treatment, food and beverage production, and the biopharmaceutical industry significantly. Each application not only underscores the versatility of microfiltration technology but also highlights its role in promoting health, safety, and sustainability.
Performance Metrics
Performance metrics are essential for assessing and optimizing the efficiency of microfiltration membranes. These metrics help to understand how well a membrane performs under varying conditions and for different applications. Reliability is key for any membrane technology; considering these metrics ensures that users can evaluate the membranes to meet specific needs.
Among the critical metrics for microfiltration membranes, flux and rejection rates, as well as membrane fouling and cleaning, play significant roles in performance evaluation.
Flux and Rejection Rates
Flux refers to the volume of fluid that passes through a membrane per unit area over time, typically measured in liters per square meter per hour (LMH). High flux values indicate that a membrane can process larger volumes of water quickly, which is often desired in industrial applications. However, a balance must be struck because increasing flux can sometimes lead to reduced filtration quality.
Rejection rates indicate how well the membrane can remove specific particles, pathogens, or substances from the fluid stream. This is vital in applications like water treatment, where the goal is to minimize contaminants effectively. Understanding both flux and rejection rates provides insight into the operational efficiency of the membrane system.
In practical terms, maintaining high flux while achieving optimal rejection rates necessitates careful monitoring of the operating conditions, including pressure and temperature. A fundamental understanding of these performance metrics is invaluable for anyone involved in membrane technology and its applications.
"Evaluating flux and rejection rates is essential for determining the suitability of a microfiltration membrane for specific industrial applications."
Membrane Fouling and Cleaning
Membrane fouling is one of the most pressing challenges in microfiltration technology. It refers to the accumulation of particles on the surface or within the pores of the membrane, leading to decreased performance and increased operational costs. Fouling can originate from various sources, including organic matter, colloids, and biofilms, thereby affecting both flux and rejection rates.
Cleaning protocols must be established to counteract fouling and restore membrane performance. These protocols can include physical, chemical, or a combination of cleaning methods. Physical cleaning may involve backwashing or air scouring, while chemical cleaning can utilize acids or alkalis to dissolve foulants. Each method has its pros and cons, which impact the longevity and effectiveness of the membrane.
The development of fouling-resistant membranes is a significant area of research. Innovations in surface modification or the use of specific materials aim to minimize fouling tendencies. Addressing the fouling issue is critical for the sustainability of microfiltration systems and can lead to lower maintenance costs and extended lifespan of the membranes.
In summary, both flux and rejection rate metrics, alongside efficient fouling management, are key to optimizing the performance and sustainability of microfiltration technologies.
Challenges in Microfiltration Technology
Microfiltration technology faces several key challenges that can affect its performance and applicability across various industries. Understanding these challenges is essential for researchers and professionals who are involved in the design, implementation, and maintenance of microfiltration systems. This section will address three primary complications: membrane fouling, longevity and durability, and scaling alongside economic viability.
Membrane Fouling
Membrane fouling is one of the most significant challenges in microfiltration. This process involves the accumulation of particles, bacteria, and other contaminants on the membrane surface, leading to reduced filtration efficiency. Fouling can occur due to both organic and inorganic materials, which can block pores and reduce the effective area available for filtration.
To mitigate fouling, several strategies can be employed. Regular cleaning procedures, such as chemical cleaning or backwashing, can help maintain membrane performance. Additionally, the selection of appropriate membrane materials that possess anti-fouling properties is critical. Some new materials, such as modified polymers, have shown promising results in reducing fouling tendencies.
"Membrane fouling not only decreases the efficiency but also increases the operational cost of microfiltration systems, making it a central issue to address."
Longevity and Durability
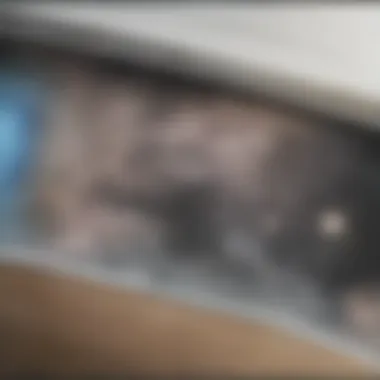
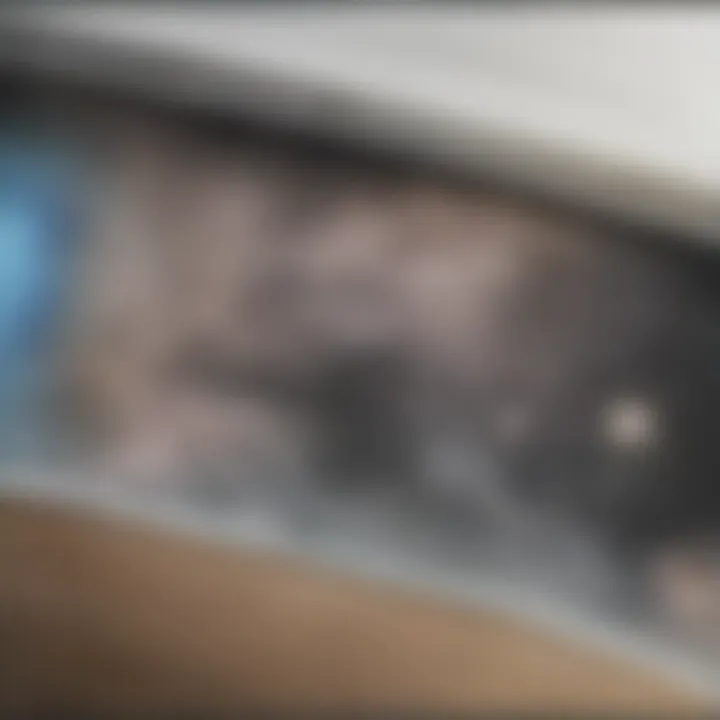
Another important consideration is the longevity and durability of microfiltration membranes. Membranes are subject to wear and tear from various operational stresses, including hydraulic pressure, temperature fluctuations, and chemical exposure. The material choice affects how long membranes will last under specific operational conditions.
High-quality membranes made from materials like polyethersulfone and ceramic composites often exhibit greater resistance to physical and chemical degradation. However, understanding the operating environment plays a crucial role in prolonging membrane life. Regular monitoring and proactive maintenance can further extend the lifespan, thus reducing the frequency of membrane replacement and associated costs.
Scaling and Economic Viability
Scaling refers to the deposition of mineral salts on the membrane surface, which can lead to similar issues as fouling. The development of scale is especially prevalent in water treatment applications where hardness is a concern. This results in more frequent need for cleaning or replacement of membranes, thus impacting the overall economic viability of microfiltration systems.
To combat scaling, techniques such as pre-treatment of feed water can help mitigate the concentration of scale-forming ions. Furthermore, factors such as energy consumption, operational costs, and capital investment must be considered when assessing the overall economics of employing microfiltration technology. As the technology advances, optimizing designs for decreased energy usage and enhanced performance may improve the financial feasibility of microfiltration in various applications.
Regulatory and Environmental Considerations
Regulatory and environmental considerations play a crucial role in the development and utilization of microfiltration membranes. As industries increasingly adopt this technology, understanding the regulations governing their use and recognizing the environmental impact becomes vital. This section will explore key areas of legislation impacting membrane use and analyze sustainability issues that arise in their application.
Legislation Impacting Membrane Use
The legal framework surrounding microfiltration membranes is complex, as it involves various national and international regulations designed to ensure safety and environmental protection. Several key legislations influence membrane application:
- Safe Drinking Water Act (SDWA): In the United States, this act sets standards for drinking water quality. Microfiltration membranes are often deployed for water treatment, and compliance with SDWA is essential to ensure the safety of water produced.
- European Union Water Framework Directive: This directive aims to protect aquatic ecosystems and ensure sustainable water usage. Microfiltration technology must meet these guidelines to be accepted for use in EU member states.
- Food and Drug Administration (FDA) Regulations: The FDA has oversight on materials intended for food and beverage processing. Microfiltration membranes must follow strict guidelines for their application in these industries.
Legislation evolves based on emerging technologies and environmental needs. Continuous assessment and adaptation to regulations are necessary for manufacturers and users of microfiltration membranes to remain compliant.
Sustainability Issues
Sustainability is a pressing concern in the use of microfiltration membranes. In recent years, the focus has shifted towards reducing environmental impact without compromising performance. Several issues arise within this domain:
- Energy Consumption: The energy required for operating microfiltration systems can be significant. There is an ongoing need to develop low-energy or energy-neutral solutions to reduce the carbon footprint of these technologies.
- Material Lifecycle: The choice of materials for membranes affects their environmental sustainability. Biodegradable or recyclable materials could minimize waste and lessen ecological impact over time.
- Chemical Usage: Cleaning and maintaining membranes often involve chemicals. Reducing or eliminating harmful substances in the cleaning process can contribute to more sustainable practices.
"The future of microfiltration depends on not just efficiency, but also the environmental responsibilities associated with their use."
Progress in sustainable practices will play a critical role in gaining public trust and regulatory approval, facilitating broader adoption. It is imperative for researchers and manufacturers to prioritize sustainable innovations in the development of microfiltration membranes for various applications.
Future Trends in Microfiltration Membrane Technology
As the demand for clean water and efficient separation processes grows, the future of microfiltration membrane technology becomes increasingly critical. This section explores innovations and integration strategies that promise to enhance the effectiveness and applicability of microfiltration membranes. Key trends include the development of innovative materials and designs that improve membrane performance and their integration with other water treatment technologies.
Innovative Materials and Designs
Advances in material science are propelling the microfiltration sector. Researchers are focused on developing materials that improve permeability and selectivity. New polymer blends and nanocomposites are significant in this evolution. Potential materials such as polyvinylidene fluoride (PVDF) and polyethersulfone (PES) are widely studied for their favorable mechanical properties.
- Nanomaterials: Incorporating nanoparticles can dramatically enhance membrane filtration efficiency. These additives can assist in reducing fouling and improving flux.
- Smart Membranes: Emerging designs may use stimuli-responsive materials that adapt under specific environmental changes. There is potential for these smart membranes to modify their properties in real time, optimizing the filtration process.
- 3D-Printed Membranes: The application of 3D printing is an innovative trend. This technique allows for precise control over membrane geometry, enhancing flow characteristics and minimizing dead zones. 3D printing may lead to quicker prototyping of membranes tailored for specific applications.
- Surface Modifications: Techniques such as surface coating and grafting can improve antifouling properties and extend the lifespan of membranes. Modification methods can make membranes more hydrophilic or hydrophobic, depending on the intended application.
By adopting these innovative materials and designs, the microfiltration industry can solve longstanding challenges, reducing operational costs while boosting efficacy.
Integration with Other Water Treatment Technologies
Integration of microfiltration membranes with other water treatment processes promises to optimize overall efficiency and effectiveness. Combining technologies allows for synergistic improvements.
- Membrane Bioreactors (MBRs): This technology blends biological processes with microfiltration, enhancing wastewater treatment. By combining biomasses' effectiveness in degrading organics with membrane filtration, operators achieve higher quality effluent.
- Reverse Osmosis: Utilizing microfiltration as a preliminary treatment before reverse osmosis can diminish fouling. It reduces the load on RO membranes, enhancing their operational life and efficiency.
- Electrodialysis: Engaging microfiltration with electrodialysis can provide significant benefits for seawater desalination. This multi-tier approach enhances salt removal while decreasing energy consumption.
- Activated Carbon Filtration: The synergy of microfiltration with activated carbon can effectively target organic contaminants. This approach ensures that toxins and particulates are removed, leading to better water quality for end-users.
"The future of microfiltration technology lies in the seamless integration of various treatment processes, leading to improvements in sustainability and operational efficacy."
Epilogue
In the context of this article, the conclusion serves as a vital synthesis of the information presented throughout the various sections regarding microfiltration membranes. This section ties together the fundamental principles, applications, challenges, and future trends discussed. In essence, the conclusion reassesses the importance of microfiltration technology as it continues to evolve, addressing both its implications and benefits across numerous sectors.
Recap of Key Points
- Definition and Function: Microfiltration membranes act as a physical barrier, facilitating the separation of particles from liquids. This functionality is crucial in various processes including water purification.
- Types of Membranes: Different materials such as polymeric, ceramic, and composite membranes cater to specific filtration needs, impacting operational characteristics significantly.
- Manufacturing Techniques: Innovations like phase inversion and sol-gel processes have improved membrane performance, durability, and scalability.
- Performance Metrics: Key indicators such as flux rates and membrane fouling affect efficiency, necessitating understanding of these variables for practical use.
- Challenges and Solutions: Membrane fouling and longevity issues remain significant hurdles, yet continued advancements in technology provide promising solutions.
- Regulatory Considerations: Adherence to legislation ensures safe and effective use of membranes, enhancing public trust and acceptance.
- Future Trends: Ongoing research indicates a shift towards novel materials and integrated systems, paving the way for enhanced filtration technologies.
The collective understanding derived from these points stresses the necessity for ongoing exploration and refinement in microfiltration technology to maintain and expand its relevance in both current and emerging applications.
Call for Continued Research
As microfiltration membrane technology advances, it is crucial that research continues to keep pace. Various areas warrant further scholarly attention:
- Material Innovations: Exploring new materials that enhance filtration capability and reduce costs is vital for the future success of the technology.
- Environmental Impact Assessments: Understanding more about how microfiltration affects environmental sustainability can guide its application in ecological contexts.
- Integration with Other Technologies: Researching how microfiltration can complement other filtration or treatment methods can enhance overall system efficacy.
- Longevity Studies: Evaluating long-term durability impacts the economic viability of membrane technologies, making this a priority for researchers.
Promoting interdisciplinary collaboration among educators, industry professionals, and researchers will lead to innovative solutions and broader adoption of microfiltration membranes, ultimately benefiting various sectors.
"The future of microfiltration is defined not only by what we know today but also by the inquiries we pursue tomorrow."
Ensuring that continued efforts focus on these areas is essential for meaningful advancements in the field.