Zinc Manufacturing: Processes, Applications, and Innovations

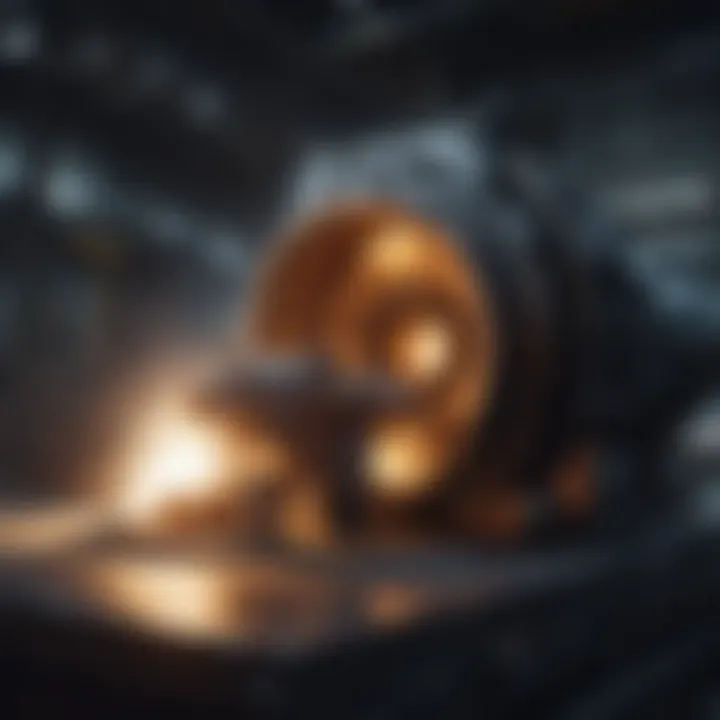
Intro
Zinc, an element often taken for granted, plays a pivotal role in various industries ranging from construction to electronics. Despite its commonality, the complexities involved in its manufacturing are nothing short of fascinating. This explore dives into the multifaceted processes that lead to the production of zinc and its numerous applications. The section will also touch upon the innovations that are pushing the boundaries of what zinc can accomplish in the modern world. Coining this phenomenon as a mix of traditional and cutting-edge techniques, it's imperative to understand how essential metal processing has evolved.
Methodologies
Description of Research Techniques
In order to grasp the intricate dynamics of zinc manufacturing, one must first understand the research methodologies utilized throughout the industry. Commonly adopted research techniques include:
- Literature Review: Gathering existing data from reputable sources like academic journals and industry reports. This serves as a foundation for understanding both historical and current practices in zinc production.
- Field Studies: Direct observations in manufacturing environments provide real-world insights into operational challenges and efficiencies.
- Experimental Techniques: Laboratory-based experiments involve isolating specific variables in the zinc extraction and refinement processes to determine optimal conditions for production.
These methods coalesce to form a robust framework for investigating the nuances of zinc manufacturing, shedding light on both its established and evolving practices.
Tools and Technologies Used
The landscape of zinc manufacturing is rich with advanced tools and technologies, enhancing efficiency and optimizing production. Key tools include:
- Electrolytic Cells: Utilized in the electrolytic process, where the separation of zinc from its ore occurs, these cells are crucial for ensuring high purity levels.
- Furnaces: Varied types of furnaces, such as blast and smelting furnaces, play essential roles in high-temperature operations that affect zinc extraction.
- Software Solutions: Modern manufacturing increasingly depends on software applications for process control, simulation, and data analysis.
Incorporating these cutting-edge technologies not only streamlines the production process but also contributes to more sustainable practices, reducing waste and environmental impact.
Discussion
Comparison with Previous Research
Exploration into zinc manufacturing reveals a significant evolution in both methods and applications compared to historical research. For instance, older methods were primarily focused on efficiency metrics without much consideration given to environmental ramifications. In contrast, contemporary studies emphasize a more balanced approach that integrates sustainability within production lines. This shift marks a pivotal progression in how zinc is perceived not just as a commodity but as a material with substantial ecological impacts.
Theoretical Implications
Theoretical frameworks surrounding zinc manufacturing have received fresh insights over the years. As new technologies emerge, previously held notions about best practices are often challenged and revised. For example, earlier models suggested linear processes; however, emerging frameworks are embracing circular economy principles. This theoretical shift indicates a move towards not only maximizing output but also minimizing resource depletion and waste generation.
Given these developments, it's evident that the manufacturing of zinc is not only about production but also about responsibility towards future generations. The combination of ongoing research and emerging best practices makes the study of zinc manufacturing a continuously evolving field.
Prelims to Zinc Manufacturing
Zinc manufacturing stands at the crossroads of various industries, embodying both tradition and innovation. Its significance stretches beyond simple metal production; it is a foundational element that underpins countless applications. From construction to electronics, understanding the nuances of zinc manufacturing has become essential for professionals across sectors. This article aims to break down the complexity surrounding this metal's manufacturing, examining the processes, the key applications, and current trends on the horizon.
Firstly, zinc's role in galvanization cannot be understated. This process involves coating iron or steel with a layer of zinc to prevent corrosion, showcasing how zinc not only adds value but acts as a protective barrier. Without this manufacturing expertise, countless structures and products would face diminished longevity, highlighting zinc’s relevance in real-world applications.
The importance of exploring zinc manufacturing also lies in its environmental impact. As industries grow more conscious about sustainability, zinc production methodologies are continuously evolving. Understanding these changes is crucial for both regulatory compliance and market positioning. The integration of recycling practices and resource management strategies demonstrate a shift towards more responsible manufacturing processes.
This overarching analysis will begin with a historical context, offering insight into how zinc production has developed over the years. We will then explore current global demand, a crucial factor for understanding the economic implications of zinc in manufacturing today.
Historical Context of Zinc Production
Zinc’s journey through history is quite fascinating. The production of zinc dates back to ancient times, with evidence of usage found in the Roman Empire where it was combined with copper to create brass. However, it wasn't until the 18th century that zinc was recognized as a distinct metal. The first smelting process, as developed by German chemist Andreas Marggraf, laid the foundation for modern zinc production.
As the Industrial Revolution swept through Europe, zinc found its place in the growing manufacturing landscape. The advent of the "new metallurgy" in the 19th century introduced techniques that improved extraction and refining, making it more accessible and versatile. Over the centuries, this metal has evolved from being considered a mere alloy to a staple in multiple industries— a transition marked by continuous innovation.
Today, zinc is extracted primarily through mining methods, such as open-pit and underground mining, followed by an arduous processing cycle that ensures quality and purity. The historical developments highlight not just technological advancements but also an increasing understanding of the metal's value.
Current Global Zinc Demand
The demand for zinc is as dynamic as the metal itself. Currently, the global market observes a significant uptick in usage, driven by diverse factors. Firstly, infrastructural growth, especially in developing nations, fuels the need for galvanized products. The construction of buildings, bridges, and highways demands components that resist rust, making zinc an irreplaceable element.
Moreover, the automotive and electronics sectors are on a growth trajectory, as they increasingly rely on zinc alloys and coatings. According to various industry reports, the market for galvanization is expected to expand steadily over the next decade. This trend is indicative of both a reliance on traditional manufacturing practices while simultaneously embracing emerging technologies.
"The balance between traditional practices and innovative methods is what shapes the current landscape of zinc demand."
As more businesses pivot towards sustainability, the interest in secondary zinc (material recovered from recycling) is also rising. This shift emphasizes the necessity for recycling processes in maintaining supply chains— a development often seen in environmentally conscious markets.
To summarize, the integral nature of zinc manufacturing, molded by historical evolution and current demand dynamics, sets the stage for understanding its full spectrum of applications, environmental considerations, and future trends to be explored further in this article.
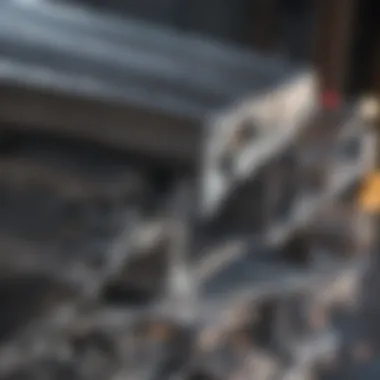
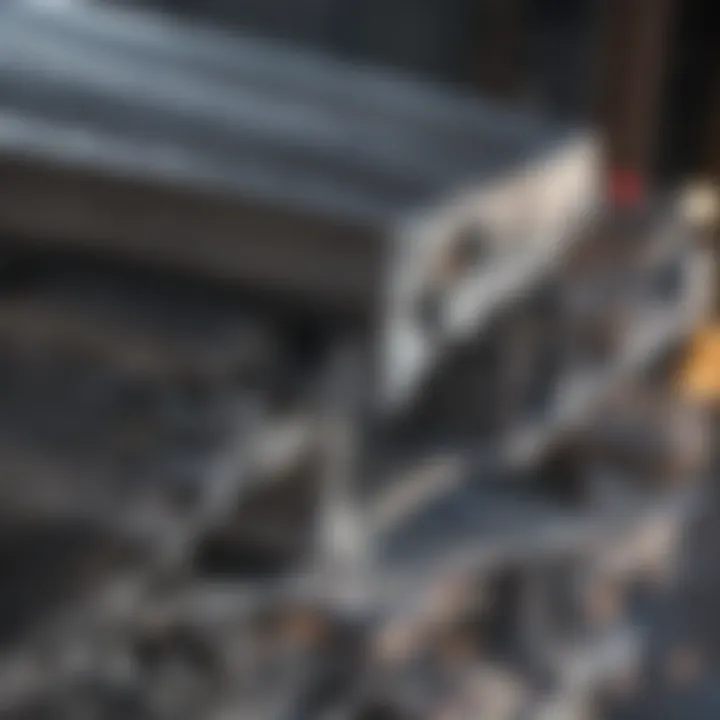
Zinc Extraction Techniques
Zinc extraction is a fundamental aspect of zinc manufacturing and understanding these techniques is vital for several reasons. First, the methods of extraction significantly influence the quality and economic feasibility of zinc production. Different extraction techniques can yield varying levels of purity and recovery rates. Therefore, knowledge of these methods directly correlates with the efficiency and viability of the processes involved in zinc manufacturing.
Moreover, as the world searches for more sustainable practices, analyzing the extraction methods provides insights into environmental impacts, energy consumption, and resource management.
Mining Methods
Open-pit Mining
Open-pit mining stands out as a widely adopted method in the extraction of zinc ores. This technique involves removing large quantities of soil and rock to reach the ore deposits near the earth's surface.
The key characteristic of open-pit mining is that it allows for the extraction of ore in a more efficient and cost-effective manner compared to other methods. The expansiveness of the pit means that heavy machinery can operate effectively, facilitating higher production rates. This method is often favored for its relatively lower operational costs, which helps keep the price of zinc in check, an important factor for producers and consumers alike.
However, this method does come with its own set of challenges. Environmental degradation is a significant concern, as the process can lead to habitat destruction and pollution. Furthermore, potential soil erosion and contamination of local water sources must be managed appropriately to mitigate these impacts.
Underground Mining
Underground mining is another commonly used technique, particularly when the zinc deposits are located deep within the earth. This method involves tunneling to extract ore while minimizing the surface disturbance often seen with open-pit operations.
A standout feature of underground mining is its reduced environmental footprint compared to surface mining. Additionally, as it goes deeper, the risk of resource replenishment increases, making this method potentially more sustainable in the long run. While this process can be more expensive and complex due to the need for additional safety measures and ventilation systems, the trade-off can be worthwhile in terms of the quality of ore extracted.
Still, this technique is not without disadvantages. Limited access to larger machinery can slow down production rates compared to open-pit mining. Thus, mining companies must assess the trade-offs between environmental impacts and economic feasibility when choosing their extraction methods.
Zinc Ore Processing
Crushing and Grinding
Crushing and grinding are critical steps in the zinc ore processing journey. This stage involves breaking down the ore to liberate the zinc minerals from the waste rock. The key characteristic of this process is its ability to prepare the ore for concentration methods that follow.
Utilizing crushing and grinding allows for improved efficiency in subsequent stages of production. It enables a higher recovery rate, which is an essential goal in zinc extraction. However, the energy consumption associated with crushing and grinding can be significant, posing a challenge to sustainability efforts.
In short, while effective, companies must continually seek to optimize these processes to minimize their energy footprint and production costs.
Concentration Methods
Concentration methods follow crushing and grinding, aiming to increase the zinc content by separating it from gangue materials. The most common techniques include flotation and gravity separation.
The key benefit of these concentration methods lies in their ability to maximize the recovery of zinc from the ore, impacting overall production efficiency. Floating materials can be selectively retrieved, leading to high-purity zinc concentrates.
Yet again, challenges abound. Some of these methods can be water-intensive, raising concerns about resource management and environmental impact.
Hydrometallurgical Processes
Leaching Techniques
Leaching techniques represent an innovative approach to zinc extraction, particularly when it comes to secondary sources like zinc-containing scrap. This process uses chemicals to dissolve zinc from its ores, allowing it to be selectively recovered.
A major advantage of leaching is its flexibility. It can be adapted to various types of ores and is often less energy-intensive than pyrometallurgical methods. However, the economic viability can depend on the concentration of zinc in the ore as well as the cost of chemicals used in the process.
Such techniques can also generate by-products which, if not managed correctly, can pose environmental risks.
Separation Processes
Separation processes are integral to hydrometallurgical techniques, focusing on isolating zinc from other minerals or metals in the solution. A common method is solvent extraction, which allows for the selective recovery of zinc in an efficient manner.
The unique feature of separation processes lies in their precision; they can significantly improve the purity of the zinc obtained. However, the effectiveness of these methods is highly dependent on the chemistry of the ore and may require extensive testing and adaptation.
Pyrometallurgical Processes
Roasting
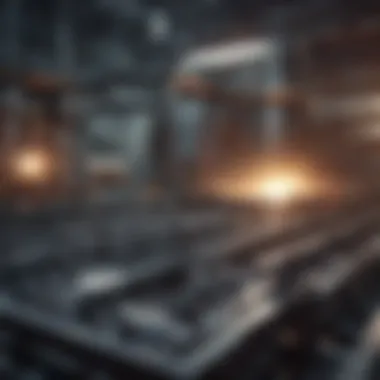
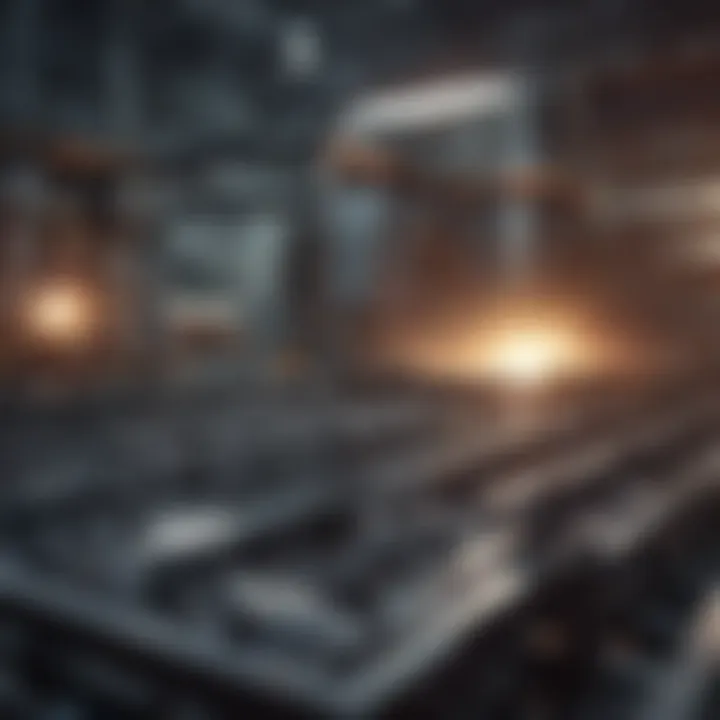
Roasting is a critical pyrometallurgical process that involves heating zinc ores to convert them into zinc oxide. This step serves as a precursor to further reduction processes.
The key benefit of roasting is that it can enhance zinc recovery rates when following up with reduction techniques. However, this step can produce sulfur dioxide, which must be managed to minimize environmental impacts.
Balancing the efficiency of production with ecological considerations is a constant necessity in optimization of roasting processes.
Reduction Techniques
Reduction techniques aim to convert zinc oxide back into metallic zinc, typically utilizing carbon in forms like coke. The uniqueness of this process lies in its direct influence on the final purity and quality of the produced zinc.
While effective, the technique comes with considerable carbon emissions, raising concerns regarding sustainability. Finding more eco-friendly reduction methods is becoming increasingly important amidst global shifts toward greener manufacturing practices.
Refinement and Production Techniques
In the world of zinc manufacturing, the refinement and production techniques play a pivotal role in determining the quality and usability of the final product. These essential processes ensure that zinc reaches its highest purity, thus making it suitable for various applications. Without these techniques, the extracted material would be substantially less effective, meaning its industrial utility would take a nosedive. The stable characteristics of refined zinc are becoming increasingly important as product demands shift towards more sustainable and durable materials across the board.
The two main processes we consider under this section are electrolytic refining and casting methods. Together, they illustrate the transition zinc goes through from a crude form to one that is ready for widespread industrial application. Not only do these processes enhance the physical and chemical properties of zinc, but they also align with modern environmental standards that demand less waste and more reclamation.
Electrolytic Refining
Electrolytic refining is a cornerstone in the zinc production landscape. its primary goal is to separate impurities and produce high-purity zinc, which can be a game changer for industries reliant on impeccable material standards. This process generally involves an electrochemical cell where an anode—typically made from impure zinc—and a cathode—often plain aluminum—are immersed in an electrolyte solution containing zinc sulfate.
During the process, zinc ions migrate from the anode to the cathode, where they deposit as refined zinc. The impurities, which may include lead, cadmium, and copper, are left behind at the anode, ensuring the resulting zinc is of remarkably higher purity.
Using electrolytic refining has several advantages:
- High Purity: The end product can reach over 99.99% purity, essential for applications in electronics and high-performance alloys.
- Resource Efficiency: Compared to other methods, it generates less waste, adhering better to sustainability goals in manufacturing.
- Versatile System: The technique can be modified to accommodate the unique recycling requirements of secondary materials.
Depending on the scale of production, this technique can become complex and requires careful monitoring for optimal performance. Automation and precision control are vital components of modern electrolytic systems.
"The journey from raw ore to refined metal is not just a tale of extraction, but rather an art of transformation that illustrates zinc's versatility in modern manufacturing."
Casting Methods
Casting methods represent another critical avenue in the zinc manufacturing sector. Once zinc has been refined, it needs to take on a usable form for practical applications, which often involves casting. There are various casting methods, but the two notable ones in zinc processing are sand casting and die casting.
- Sand Casting: This method involves creating a mold from sand. It’s particularly suited for larger components where precision is less critical. The process typically allows for the inclusion of intricate designs and is often employed for recycling older zinc products. This method is also cost-effective for small production runs.
- Die Casting: Used primarily for small, complex shapes, die casting involves forcing molten zinc into molds under high pressure. This method ensures tighter tolerances and a smoother finish than sand casting, making it ideal for applications like automotive components and hardware fittings. The trade-offs include higher costs and tooling requirements, which might not suit all manufacturers.
Choosing between these methods often comes down to the specific needs of the project, including costs, production volume, and desired quality characteristics.
Applications of Zinc
Zinc plays a crucial role in various industries, essential not only for its physical properties but also for its diverse applications. This section explores numerous ways zinc is utilized, underscoring its significance from enhancing structural integrity to its importance in healthcare. Each application showcases how vital zinc is in contemporary manufacturing, providing solutions to a myriad of challenges.
Galvanization
Process Overview
In the realm of zinc applications, galvanization stands out as a key method for corrosion protection. This process involves coating steel or iron with a layer of zinc to prevent rust formation. Galvanization is appreciated not just for its protective qualities but also for the cost effectiveness it brings to the table. A notable characteristic of this process is that it enhances longevity without needing constant maintenance. One unique feature of galvanization is its self-healing property; if the coating gets scratched, the surrounding zinc will still protect the underlying metal. This makes it a beneficial method for industries where metal structures are exposed to harsh environments, such as construction and automotive sectors.
Performance Benefits
The performance benefits of galvanization relate directly to its ability to extend the life of metals significantly. Structures that undergo this process often exhibit durability that outlasts untreated counterparts by several years. Corrosion resistance is the standout characteristic of galvanized products, ensuring they remain dependable over time. Though there is a slight initial investment for galvanizing, the long-term advantages far outweigh the cons, making it a popular choice across various sectors. Additionally, its aesthetic appeal when it comes to finishes can also enhance the overall look of metallic structures.
Zinc Alloys
Brass Manufacturing
Brass manufacturing is another area where zinc shines due to its alloying properties. Brass, an alloy primarily of copper and zinc, is favored for its excellent machinability and resistance to corrosion. The inclusion of zinc not only helps improve the mechanical properties of the alloy but also influences its color and finish, allowing for a wide range of applications. A key aspect of brass manufacturing is its versatility; it can be molded into complex shapes, making it ideal for both decorative and functional components. The unique feature of using brass is its acoustic properties, which makes it valuable in music instrument production. However, while brass can be more expensive than pure zinc, its benefits often justify the costs in applications requiring aesthetic and functional excellence.
Die Casting Applications
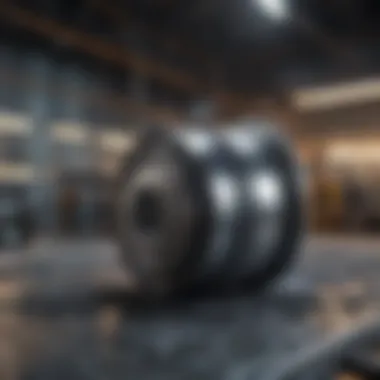
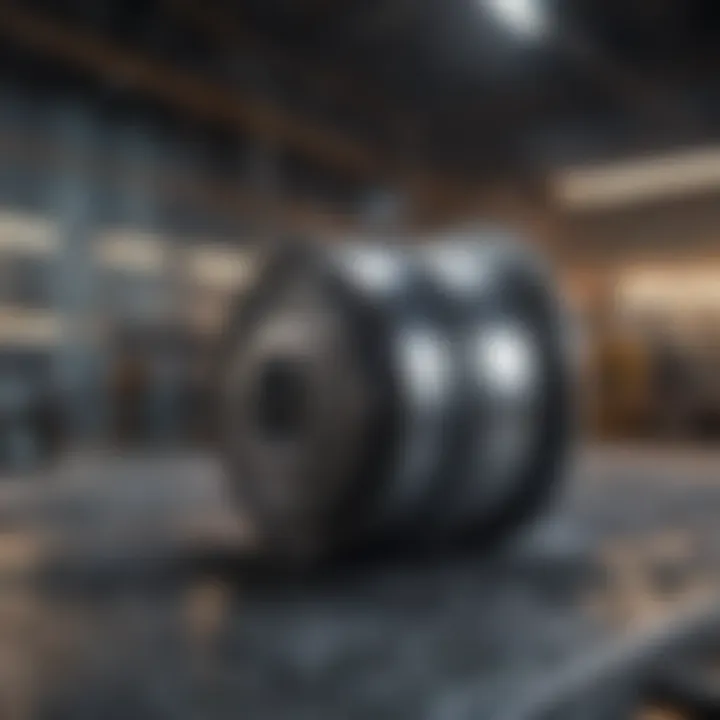
Die casting is yet another prominent usage of zinc in alloys, known for producing intricate parts with high precision. Zinc die casting involves injecting molten zinc into a mold which enables the production of complex shapes that are lightweight and durable. A key characteristic of this process is the efficiency it brings; large quantities can be produced rapidly, minimizing waste. This method is popular in industries ranging from automotive to electronics, offering excellent dimensional stability. The unique feature of die-casted zinc products is their reliable performance under mechanical stress, although one should note the limitation of zinc's soft nature compared to more robust metals.
Miscellaneous Uses
Pharmaceutical Applications
Zinc is pivotal in the pharmaceutical industry, serving numerous roles in various formulations. As an essential trace element, it contributes to numerous biochemical processes in the human body. The benefits of including zinc in medicines lie in its immune-boosting properties and its role in wound healing. A notable aspect is its ability to stabilize cellular membranes, making it a valuable component in supplements and topical creams. One distinct characteristic of pharmaceutical applications of zinc is its balance between efficacy and the minimal side effects compared to other treatments. However, excessive zinc intake can lead to adverse effects, thus requiring careful formulation and dosing.
Cosmetic Industry
In the cosmetic realm, zinc's anti-inflammatory properties mark its importance. Used in creams, sunscreens, and ointments, zinc oxide is a go-to ingredient due to its ability to shield the skin from harmful UV rays. This quality makes products containing zinc a beneficial choice for consumers looking for skin protection and healing. The unique feature of zinc in cosmetics is its capability to provide a matte finish, ideal for formulations targeting oily skins. However, there can be formulation challenges, as some people may experience sensitivity to zinc products, necessitating further testing.
Zinc's applications are not just integral to manufacturing but also to our everyday lives, highlighting its multifaceted contributions to society.
In summary, zinc's vast range of applications underscores its relevance in multiple sectors. From galvanization and alloys to healthcare and cosmetics, zinc serves varied roles that enhance performance, aesthetics, and health. Each application brings its distinct advantages, solidifying zinc as a linchpin in modern industry.
Environmental Considerations
Zinc manufacturing, like many industrial processes, inevitably brings environmental implications to the forefront. Understanding environmental considerations is vital as it helps balance industrial needs with ecological preservation. The discussions in this section aim to highlight the shifts toward more sustainable practices, the recycling of essential materials, and effective management strategies that can be employed throughout the zinc production cycle.
These considerations save money, protect vital ecosystems, and align industry practices with global sustainability goals. Through a holistic examination of sustainability in zinc production and its impact on ecosystems, we can delve into how innovative practices can integrate environmental stewardship without sacrificing the economic benefits of zinc.
Sustainability in Zinc Production
Recycling of Zinc
Recycling zinc is a critical component in fostering sustainability within the industry. The main aspect of recycling is its ability to minimize waste; instead of discarding zinc products at their end-of-life, they can be collected and processed. This approach not only reduces the mining demand for raw ores but also significantly cuts energy consumption associated with the overall production process.
One key characteristic of zinc recycling is its efficiency. The process achieves near-complete recovery of zinc with quality comparable to newly produced materials. This makes recycling a popular choice among manufacturers looking to maintain quality while enhancing environmental performance.
The unique feature here lies in the longevity of zinc; it can be recycled multiple times without degrading its properties—this opens the door for continuous sustainable practices within the industry. However, while there are clear advantages to recycling, challenges remain: ensuring a stable supply of scrap zinc and the imperatives of separate collection methods are often necessary.
"Recycling is not just about recovery; it’s a systemic approach to resource efficiency that sparks innovation in production techniques."
Resource Management
Effective resource management serves as the backbone of sustainability within zinc production. It emphasizes the careful allocation and usage of natural resources to optimize production while minimizing environmental impact. Resource management approaches incorporate techniques to maximize the yield from both primary and secondary sources, reducing the overall extraction pressure on the earth's crust.
The defining characteristic of resource management in this context is its systemic nature. It incorporates measurements like life cycle assessments and resource audits to ensure that every step in the zinc production chain is as efficient as possible. By employing these strategies, industries can identify areas for improvement and innovation, making resource management an exceedingly valuable choice in the discourse of this article.
A unique advantage of effective resource management is its potential for cost savings—lower raw material procurement costs can lead to a significant reduction in overall operating costs. Nonetheless, the challenge often lies in complex logistics and the need for detailed data collection, which require an upfront investment that may deter smaller players in the market.
Impact on Ecosystems
Understanding the impact of zinc production on ecosystems is paramount. Zinc manufacturing can influence soil and water quality if not managed properly. Factors like waste disposal and emissions must be systematically examined to mitigate their effects.
Also, nearby wildlife and plant life can be adversely affected, especially in areas where mining and production facilities operate without stringent environmental guardrails. Incorporating eco-friendly methodologies can go a long way in protecting these ecosystems, leading to a lasting symbiosis between industry and natural habitats.
As the industry moves forward, prioritizing environmentally sound practices will not only contribute to better ecological outcomes but also enhance public perception and compliance with regulatory frameworks.
Future Trends in Zinc Manufacturing
The world of zinc manufacturing is at a pivotal juncture, influenced by evolving technologies and changing market dynamics. Emphasizing future trends not only aids in grasping the industry's potential but also highlights critical elements that may reshape practices in the coming years. Key benefits of understanding these trends include adapting to market demands, promoting sustainability, and opening avenues for innovative applications. The exploration of this section will illuminate significant directions in zinc manufacturing, enhancing our comprehension of its relevance in the modern landscape.
Innovative Technologies
Automation in Production
Automation fosters efficiency, accuracy, and safety in zinc manufacturing. The steady march towards automated production lines transforms how processes are executed, reducing human error while speeding up operations. This aspect is increasingly favored as companies strive to enhance productivity and minimize costs. One key characteristic of automation is its capability to perform repetitive tasks without fatigue, allowing for a constant production output.
However, it’s worth noting that automation can present challenges, like the initial financial investment in technology and training for handling these systems. Yet, the long-term benefits may outweigh these drawbacks.
Advanced Materials Research
Advanced materials research delves into the exploration of new alloy compositions and coatings that utilize zinc's properties more effectively. This research is vital for developing stronger, lighter materials that further expand zinc's applications in various industries. A distinctive feature lies in utilizing nano-coatings that boost durability and resistance to corrosion while potentially reducing the amount of zinc needed in individual applications. The popularity of this approach stems from its potential to lower manufacturing costs and lessen environmental impact. However, challenges persist, particularly in the initial R&D stages, which often require significant investment and time before yielding practical results.
Market Outlook
The market outlook for zinc manufacturing depicts a landscape gradually emphasizing sustainability and technological advancements. Global demand for zinc primarily arises from construction, automotive, and electronics industries. Recognizing these trends, companies are increasingly leaning towards eco-friendly practices and innovative technologies that improve production efficiency. According to several industry reports, the global zinc market is expected to witness steady growth in the next decade, driven largely by emerging economies' infrastructure needs.
"The future of zinc holds promise, especially as industries focus on reducing carbon footprints and enhancing material performances."