Understanding Strain Gauges: Principles and Innovations
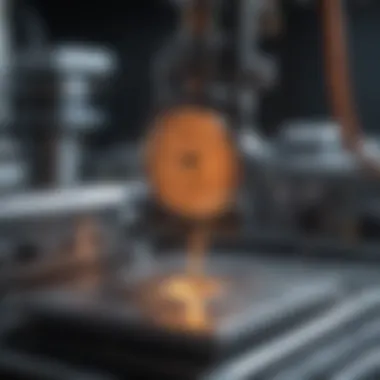
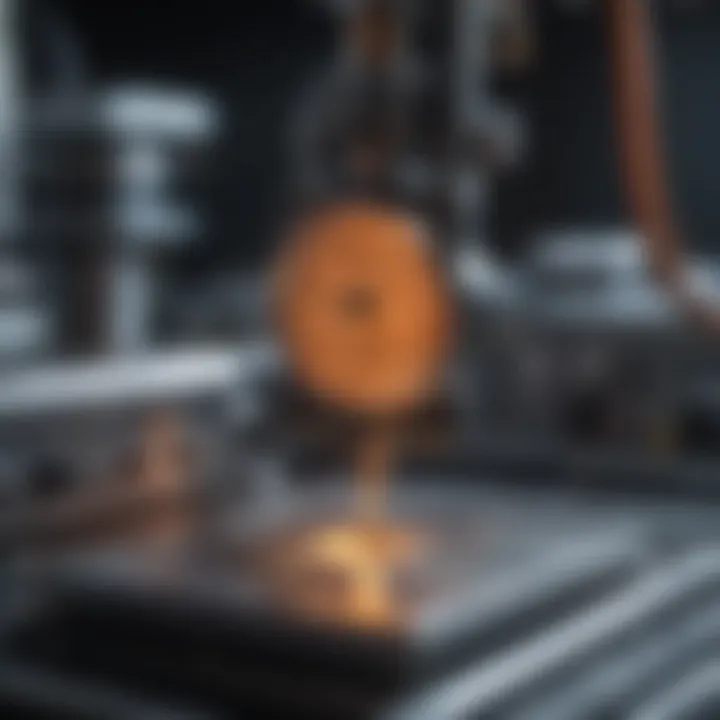
Intro
Strain gauges are fundamental devices in the field of engineering and scientific research. They play a pivotal role in quantifying the deformation or strain experienced by an object when subjected to external forces. By measuring these changes, strain gauges provide valuable data that informs the design and analysis of structures, machines, and various mechanical systems. The significance of strain gauges is reflected in their widespread applications across multiple industries, from aerospace to civil engineering and biomedical fields.
The basic operational principle involves the change in electrical resistance that occurs when a conductive element is deformed. This characteristic allows strain gauges to transform mechanical deformation into a measurable electrical signal, facilitating precise monitoring and analysis. As we progress through this exploration, the intricacies of their functionality, various implementations, and the innovative advancements in this technology will unfold.
In a world where precision is non-negotiable, understanding the role of strain gauges becomes not only beneficial but imperative. As organizations seek to optimize their designs and methodologies, the insights gained from strain gauge technology provide invaluable support in achieving optimal performance, safety, and reliability.
We will delve into the specific methodologies utilized in strain gauge applications, the innovative tools available, and the evolving landscape that surrounds these sophisticated instruments.
Preamble to Strain Gauges
Strain gauges are pivotal devices in the realm of engineering and scientific measurement, fuelling the innovation and analysis of material properties under stress. They are used to determine deformation, a critical characteristic when evaluating the integrity of structures and mechanical systems. Understanding strain gauges thus holds significance for various industries, from civil engineering to biomedical applications.
The essence of strain gauges lies in their ability to convert mechanical deformation into measurable electrical signals. This translation from physical strain to electrical output allows for real-time monitoring and assessment of materials and components, whether it's a bridge under heavy traffic or a prosthetic limb adapting to a patient's movement. Moreover, their use facilitates predictive maintenance, ultimately safeguarding assets and enhancing safety standards.
Defining Strain Gauges
Strain gauges are sensors that measure the amount of deformation or strain experienced by an object. They work on a simple premise: when an object is subjected to stress, it undergoes deformation, which leads to changes in electrical resistance in the gauge affixed to it. The primary function of a strain gauge can be summed up into a straightforward definition — it detects and quantifies these changes in response to external forces.
To clarify further, when a strain gauge is bonded to a material, any tensile or compressive force leads to a change in the length and cross-sectional area of the gauge's material, thereby altering its electrical resistance. This shift in resistance is proportionate to the strain and can be precisely measured, making strain gauges indispensable in experiments and practical applications alike.
Historical Background
The journey of strain gauges dates back to the 1930s. The technology emerged from the need for accurate measurements in structural engineering and materials science. One of the early developments was by George T. McGibboney, who pioneered the wire strain gauges. These gauges were fabricated using fine wire wrapped in a grid pattern, providing a reliable connection to measure deformation under load.
Over the decades, improvements continued, leading to the introduction of foil strain gauges in the 1950s. Foil gauges marked a significant milestone, as they offered enhanced sensitivity due to their reduced mass, improving responsiveness to changes in strain. This evolution continued with the incorporation of semiconductor technology in the 1980s, creating gauges that exhibit greater sensitivity compared to their metallic predecessors.
The advancement of strain gauges into modern applications now embraces optical technologies and smart materials, pushing boundaries in measuring and monitoring systems. As the demand for accuracy in measurement grows, understanding the historical context of strain gauges becomes imperative, highlighting the strides made in material science and engineering.
"The journey of strain gauge technology illustrates not only the evolution of measurement techniques but also the growing intersection of engineering disciplines."
Fundamental Principles
Understanding the fundamental principles of strain gauges is paramount in grasping their entire operational spectrum. These principles lay the groundwork for how strain gauges function, the relevance they hold in various applications, and their continual evolution in technology. The relationship between mechanical deformation and the resulting strain sensed by the gauge, along with the role of the Wheatstone bridge circuit in quantifying these changes, form the backbone of strain gauge technology. By mastering these concepts, students and professionals can harness the full potential of strain gauges in their respective fields.
Mechanical Deformation and Strain
Mechanical deformation occurs when an external force is applied to an object, causing it to change shape or size. This alteration can be temporary or permanent, depending on the force applied and the material's properties. The deformation experienced by materials can be categorized mainly into elastic and plastic strains. The former is reversible, allowing materials to return to their original shape once the stress is removed, while the latter results in a permanent change.
Strain gauges are designed to measure these deformations accurately. When a strain gauge is adhered to a material, any deformation due to stress leads to a change in the gauge's resistance. This change can be precisely measured and used to calculate the amount of strain experienced.
To summarize:
- Deformation: Change in shape or size due to stress.
- Elastic strain: Temporary deformation that disappears when the stress is removed.
- Plastic strain: Permanent alteration of the material shape.
Understanding mechanical deformation is essential. It shapes how engineers assess material performance and helps in designing structures that can withstand environmental forces.
The Wheatstone Bridge Circuit
The Wheatstone bridge circuit is a fundamental aspect of strain gauge operation, allowing for precise measurement of resistance changes. This circuit consists of a diamond shape of four resistors, with a voltage source applied across one diagonal and a galvanometer (or measuring instrument) across the other. When a strain gauge is integrated into the circuit, an applied strain modifies its resistance, leading to a voltage imbalance detectable by the galvanometer.
Principles of Operation
The principle of operation of the Wheatstone bridge circuit simplifies the complex task of measuring tiny resistance changes resulting from strain. Its configuration makes it a favorites choice for this application, as it minimizes error and maximizes sensitivity. The unique setup allows for direct comparative measurements that enhance accuracy, which is robustly beneficial when dealing with the minute changes in resistance typical with strain gauges.
Each arm of the bridge must be appropriately balanced before strain is applied. Upon deformation, the differential voltage allows the output to reflect the strain, making it indispensable in dynamic measurements where both precision and speed are crucial. However, one must carefully calibrate and account for initial resistance values to achieve optimal results.
Calibration Techniques
Calibration techniques play an essential role in ensuring that strain gauges provide accurate and reliable measurements. With calibration, engineers can establish the relationship between the measured strain and the electrical signal output, making it a linchpin for meaningful data collection. One notable characteristic of effective calibration is its capacity to account for variations in environmental conditions, which can significantly affect readings.
Common methods of calibration may involve the use of known weights or applying specific strains while adjusting the measurements on the recording instrument. A standout feature of calibration is its adaptability; it can apply to various gauge types, from simple foil gauges to complex semiconductor models.
However, the calibration process is not without its challenges. Factors such as temperature changes, improper installation, and wear over time can affect accuracy. Thus, ongoing recalibration is often necessary for long-term applications.
"The precision of strain gauging begins at a fundamental level. Without solid principles, applications might crumble like a house of cards."
Types of Strain Gauges
Understanding the various types of strain gauges is key for designing effective measuring systems in engineering and science. Different strain gauges come with distinct properties that allow them to perform optimally under various circumstances. From materials to fabrication techniques, the choice of strain gauge impacts not only the measurement efficiency but also the reliability of the data gathered. Here, we will examine four primary types: foil, wire, semiconductor, and optical strain gauges.
Foil Strain Gauges
Foil strain gauges are perhaps the most commonly used type in modern applications. Their construction involves creating a pattern of conductive foil on a backing material, usually made from an insulating polymer. This design allows for high accuracy and excellent sensitivity. One of the standout points about foil gauges is their remarkable resistance to temperature fluctuations, making them reliable in environments where conditions can change swiftly.
Moreover, these gauges are simple to install and can be affixed to varied surfaces, including metals and composites. The design of foil strain gauges is relatively straightforward, allowing for mass production at low cost. Because of these attributes, they have become popular in industries such as automotive and aerospace, where precise measurement is critical.
Wire Strain Gauges
Wire strain gauges, built from a fine wire element, were the original design in strain gauge technology. They are often crafted using alloys like copper-nickel or stainless steel, and their main advantage lies in their durability and robustness. These gauges can withstand significant strain and are less susceptible to damage, making them ideal for heavy-duty applications.
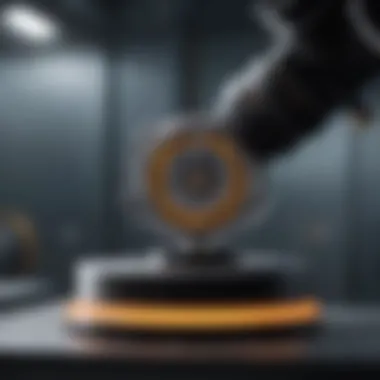
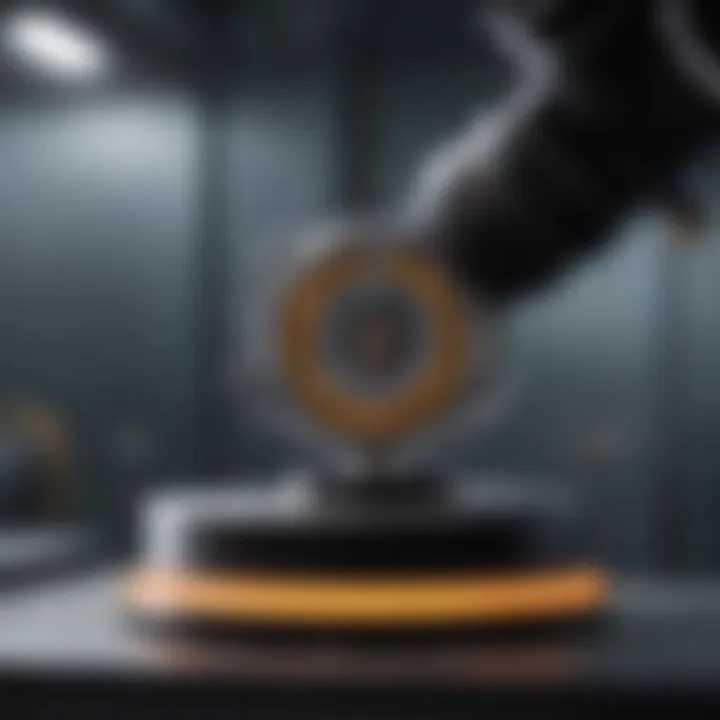
A notable characteristic of wire strain gauges is their ability to measure larger displacements compared to some other types. This attribute is valuable in experimental stress analysis and similar applications. However, the complexity of installation can pose challenges, as their placement requires careful consideration to ensure accurate measurements.
Semiconductor Strain Gauges
Semiconductor strain gauges are on the technical side of the family, often utilized in situations demanding high sensitivity. These gauges are made from silicon or germanium, which allows them to have a much greater gauge factor than their metallic counterparts. This means they can provide vastly higher sensitivity even with minimal strain.
However, this heightened sensitivity comes with some drawbacks. Semiconductor strain gauges can be quite sensitive to temperature changes, which might complicate their use in environments where temperatures are not stable. Despite that, advancements in technology are slowly addressing these issues, making semiconductor gauges more appealing. In demanding applications such as precision weighing or micro-measurements, they are often the go-to choice due to their high performance.
Optical Strain Gauges
Optical strain gauges work on the principle of light transmission through optical fibers. When a fiber is stretched, the light traveling within it experiences a change in its path, allowing for the measurement of strain. This type of strain gauge is relatively new but growing in popularity due to its unique advantages.
One of the primary benefits of optical strain gauges is their immunity to electromagnetic interference. In environments with strong electromagnetic fields, these gauges can operate without fear of signal distortion, unlike their electronic counterparts. Additionally, they can be deployed in remote monitoring applications where traditional gauges might fail or be impractical due to access difficulties.
"Choosing the right strain gauge isn't just about the number; it's about knowing what’s beneath the surface."
Each of these types has its place, determined by the specific applications and environmental considerations in play.
Manufacturing and Material Considerations
Manufacturing and material considerations have a pivotal role in the field of strain gauges. The choice of material and the methods used in fabricating these gauges impact not only their performance but also their longevity and precision in applications across various industries. Selecting the right materials can significantly influence the strain gauge's sensitivity, temperature stability, and ability to function under hostile environmental conditions.
When engineers and researchers prioritize the manufacturing aspects, they delve into the specifics of both metallic and polymeric materials. Both categories present unique benefits and trade-offs that can affect the gauge's usefulness for particular tasks.
Material Selection
Metallic Materials
Metallic materials constitute a traditional choice for strain gauges due to their robust electrical conductivity and well-established performance in diverse applications. Copper and aluminum are common metals utilized, as they exhibit predictable behavior under strain. One of the key characteristics of metallic strain gauges is their excellent linearity, making them easy to relate to the amount of deformation experienced.
Although they are widely popular, metallic materials have somewhat limited range when it comes to their operational temperature qualities. They can become less effective at dramatically high or low temperatures. Additionally, while they tend to be more reliable, they aren't necessarily the lightest or most adaptable option available.
- Advantages of Metallic Materials
- Disadvantages of Metallic Materials
- Excellent linearity in readings
- High sensitivity to strain
- Robustness in various environments
- Temperature sensitivity can limit range
- Not as lightweight compared to polymers
Polymeric Materials
Polymeric materials bring a different flavor to strain gauge manufacturing. They offer higher flexibility and the potential for integration into intricate 3D designs, which is often a necessity in modern engineering projects. The lightweight nature of polymers creates opportunities for innovations in design applications, particularly in areas like biomedical engineering where comfort and adaptability matter significantly.
The main appeal of polymeric strain gauges lies in their impressive range of operable temperatures, which can outperform metals under certain conditions. Yet, their mechanical strength is often inferior to that of metals, which might hinder their application in high-load scenarios.
- Advantages of Polymeric Materials
- Disadvantages of Polymeric Materials
- Flexibility allows for complex designs
- Wider operational temperature range
- Lightweight and comfortable for wearable applications
- Potentially less robust under high loads
- May not provide the same electrical conductivity as metals
Fabrication Techniques
Shifting focus to the methods of creating strain gauges, fabrication techniques such as screen printing and laser cutting are often pivotal for achieving desired specifications and innovations in performance.
Screen Printing
Screen printing is recognized for its capability to produce intricate patterns on a range of surfaces with precision. This technique involves pushing ink through a mesh to transfer designs, allowing for a high level of control over the gauge layout. The benefits of screen printing lie in its adaptability for various substrates and thicknesses, leading to cost-effective and scalable solutions in large volumes.
However, screen printing might incur challenges in ensuring consistent quality across a production batch, specifically in terms of ensuring that the ink adheres uniformly across different materials.
- Advantages of Screen Printing
- Disadvantages of Screen Printing
- Versatile for different substrates
- Cost-effective for mass production
- Quality consistency may fluctuate
- Potential constraints in design complexity
Laser Cutting
Laser cutting presents a technique that elevates precision to new heights. This method utilizes focused laser beams to cut materials with extreme accuracy, making it ideal for both complex shapes and fine details in the design. Reliability in laser cutting lays in its capability to handle a varied range of materials, including both metals and polymers.
Despite its advantages, the cost of setting up laser cutting systems may be a barrier to entry for smaller manufacturers, which might struggle with high initial investment requirements.
- Advantages of Laser Cutting
- Disadvantages of Laser Cutting
- High precision with minute details
- Ability to work with various materials
- High setup costs may limit access
- Slower compared to mass printing methods
In summary, understanding the nuances of material selection and fabrication techniques is crucial for advancing strain gauge technology. Striking a balance between the properties of metallic and polymeric materials, alongside optimal manufacturing processes, can set the groundwork for more sophisticated and reliable gauging solutions.
Applications Across Industries
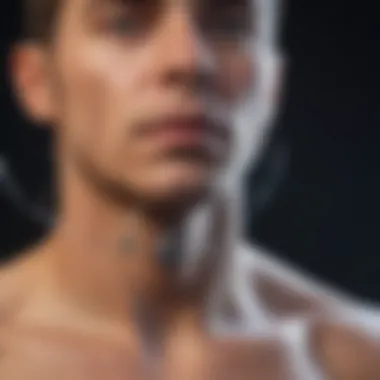
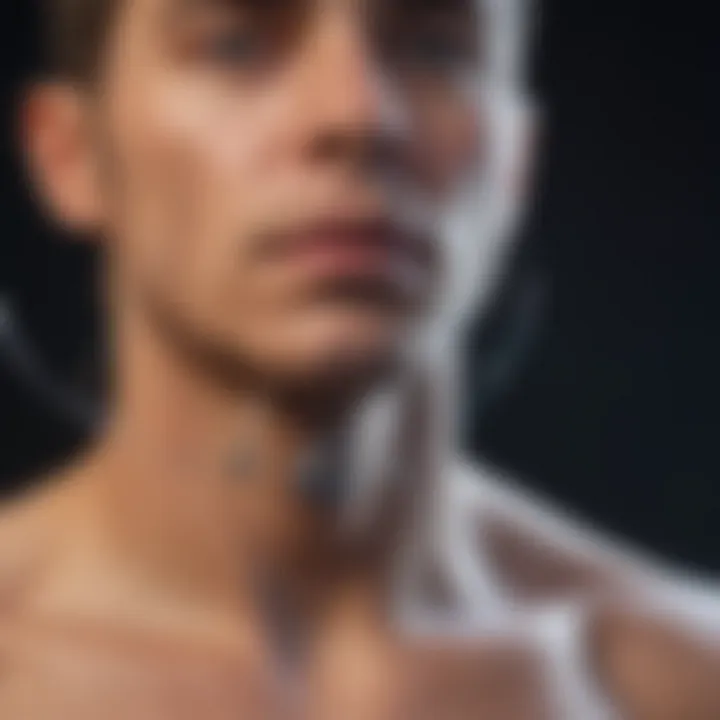
Strain gauges find their footing in a variety of sectors, underscoring their versatility and significance in modern applications. From civil engineering to aerospace, these devices help bridge the knowledge gap in understanding how materials respond under stress. In industries where precision and reliability are paramount, the role of strain gauges becomes even more critical, ensuring safety and efficiency in operations.
Civil Engineering
Structural Health Monitoring
Structural Health Monitoring (SHM) utilizes strain gauges to track the integrity of structures over time. By deploying these devices in critical areas, engineers can detect early signs of distress, allowing for proactive maintenance before catastrophic failures occur. This capability makes SHM not just a beneficial approach, but an essential part of modern infrastructure management.
One of the standout characteristics of SHM is its ability to provide real-time data. This means that engineers are not left in the dark; they can actively monitor the state of buildings, bridges, and dams throughout their lifespan. SHM is popular because it promotes a culture of safety and forethought in construction management. However, it does come with a unique feature—sensitivity to environmental influences. Factors like temperature and humidity can skew readings, which necessitates rigorous calibration practices.
Load Analysis
Load Analysis is another critical application of strain gauge technology in civil engineering. Engineers employ strain gauges to assess how loads distribute across different structural members. This data is pivotal in ensuring that buildings can withstand both static and dynamic loads without risking structural failure.
A key point here is that Load Analysis helps to maximize the utility of materials. Instead of over-engineering a structure, leading to increased costs and unnecessary resource consumption, load analysis allows for optimized designs. This balanced approach is a popular choice as it connects directly to cost efficiency and sustainability. However, reliance on the accuracy of strain gauges requires careful consideration. Misinterpretations of the data can lead to dangerous oversights in construction practices.
Aerospace Engineering
Fatigue Testing
In aerospace, fatigue testing is crucial in determining the lifespan and safety of components. Strain gauges are installed on aircraft parts to monitor stress under various operational conditions. This testing provides invaluable data on how materials behave when subjected to cyclic loading.
The paramount benefit of fatigue testing with strain gauges is the ability to evaluate material performance in real-world scenarios. This approach ensures that even the smallest component, which may seem insignificant, contributes positively to the aircraft's overall integrity. The unique feature of this application lies in its predictive capability; it provides insights into when a component might fail in the future. On the downside, the need for precise setup and data interpretation makes this a technically demanding process.
Performance Evaluation
Performance evaluation in aerospace leverages strain gauges to guarantee that systems work as intended. Through real-time data gathering, engineers can assess not only static loads but also dynamic responses during flight maneuvers. This monitoring ensures that aircraft maintain optimal performance levels under various conditions.
A hallmark characteristic of using strain gauges in performance evaluation is their adaptability. They can be integrated into various systems without significant redesign, making them a flexible choice for engineers. However, the challenge remains in the management of data overload, which can happen if too many variables are monitored at once.
Biomedical Applications
Prosthetics Design
Strain gauges are also reshaping the landscape of prosthetics design. These devices provide critical feedback on how prosthetic limbs bear weight and respond to daily activities. This data is essential to develop high-quality prosthetics that can adapt to individual needs.
The standout feature of using strain gauges in prosthetics is their ability to offer precise measurements of forces acting on the devices. This leads to improved design tailored to user experiences. However, the limitation lies in ensuring comfort and usability of the sensors themselves within the prosthetic framework.
Biomechanical Studies
In biomechanical studies, strain gauges empower researchers to investigate the interactions between biological tissues and external forces. By analyzing how muscles and bones react under different conditions, significant advancements are made in physical rehabilitation and sports science.
A defining characteristic of biomechanical studies using strain gauges is their ability to draw connections between observed mechanics and theoretical models. It provides a rich narrative on how movement can be optimized, aligning physical therapy with engineered solutions. The downside, however, involves the complexity of biological systems, making it challenging to isolate variables accurately.
Automotive Industry
Crash Testing
In automotive testing, the use of strain gauges is indispensable during crash tests. They provide crucial data on how vehicles deform upon impact, enabling engineers to enhance safety features. These insights play a vital role in airbag deployment and structural reinforcement designs.
The defining feature of strain gauges in crash testing is their ability to precisely capture transient events. They record changes that happen in milliseconds, which is critical for analyzing the effectiveness of safety systems. This kind of testing is beneficial because it directly informs regulatory standards and industry safety protocols. Yet, the high-stakes environment calls for impeccable calibration, as errors can lead to misleading conclusions about vehicle performance.
Engine Dynamics
Strain gauges assist in monitoring engine dynamics by measuring vibrations and structural deformations during operation. Understanding these metrics allows automotive engineers to improve performance and longevity of engines.
A key advantage of using strain gauges in engine dynamics is their ability to provide immediate feedback on engine behavior under load. This choice helps engineers fine-tune engines to meet efficiency benchmarks without compromising power output. On the flip side, the challenge lies in the installation of sensors, where they may be subject to extreme conditions, potentially affecting their lifespan and accuracy.
Through these applications across industries, the relevance of strain gauges remains evident. They not only allow for enhanced understanding and data collection but also pave the way for innovations aimed at improving safety, efficiency, and functionality in various fields.
Advancements in Strain Gauge Technology
The field of strain gauge technology has seen remarkable progress in recent years, reshaping how engineers and scientists monitor and analyze material deformations. These advancements not only improve the accuracy of measurements but also broaden the horizons of applications. With contemporary challenges demanding more precise data collection and analysis, innovation in this area can be pivotal to various sectors, whether it's biomedical engineering or civil infrastructure.
Wireless Strain Measurement
One of the most significant advancements is the advent of wireless strain measurement systems. Traditionally, strain gauges required hardwired connections to data acquisition systems, which could impose limitations on mobility and flexibility. Wireless systems eliminate this barrier. They allow for easier installation and scalability in remote or hard-to-reach locations, such as bridges or aircraft. Not only do these systems facilitate real-time data collection, they also minimize the risk of wiring damage in high-stress environments.
The integration of wireless technology can enhance data integrity too. Sensors that communicate wirelessly mitigate issues related to electromagnetic interference that often affect traditional wired arrangements. Coupled with the development of compact and energy-efficient battery technologies, wireless strain gauges can operate effectively for extended periods without needing maintenance, thus reducing downtime.
In essence, wireless strain measurement opens up opportunities for long-term monitoring and instant feedback in research contexts. It's a game changer for applications that require consistent data, such as fatigue testing in aerospace engineering or structural health monitoring in civil projects.
Smart Materials Integration
The integration of smart materials into strain gauge technology signifies another leap. Smart materials, which can adapt to environmental changes, enhance the functionality of traditional strain gauges. These materials can respond dynamically to strain, offering insights beyond mere deformation.
For instance, piezoelectric materials can generate electrical charge in response to mechanical stress. This property can be harnessed to develop strain gauges that not only measure deformation but also provide energy to power sensors or transmit data. This self-sustaining capability reduces reliance on external power sources, making it suitable for remote installations.
Furthermore, the synergy between smart materials and advanced data analytics creates opportunities for predictive maintenance. Devices equipped with smart materials can potentially analyze strain data to forecast failures before they happen, allowing engineers to take preventative actions.
In summary, the integration of smart materials into strain gauge technology is pushing the boundaries of real-time monitoring and proactive maintenance across industries. With ongoing research, the full potential of these materials could redefine how we approach structural integrity assessments and the overall durability of materials.
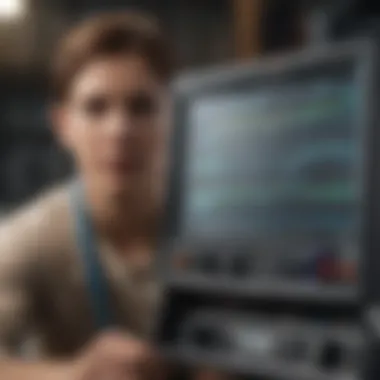
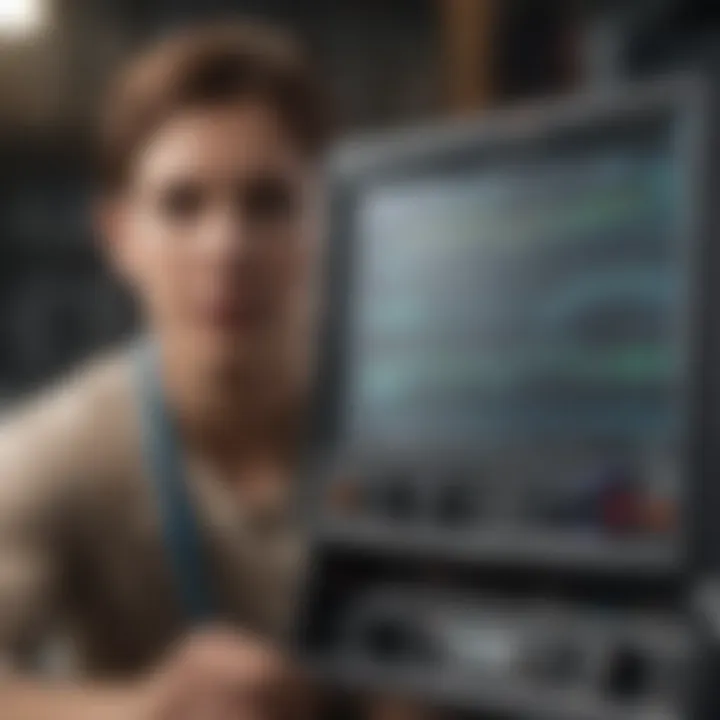
"The future of strain gauge technology is not just in measuring stress, but in understanding and predicting material behavior under varying conditions."
The combination of wireless capabilities and smart materials is indicative of a broader trend towards more sophisticated, reliable, and intelligent measurement systems. As we venture further into the 21st century, the evolution of strain gauge technology is likely to play a critical role in ensuring the safety and performance of structures, devices, and materials in our increasingly complex world.
Challenges and Limitations
Understanding the challenges and limitations of strain gauges is crucial for anyone engaging with this technology, especially in research and practical applications. These gauges, while immensely useful, are not infallible; their effectiveness can be compromised by various factors. Addressing these challenges helps in harnessing their full potential while meeting the demands of accuracy and reliability in measurements.
Environmental Factors Impact
Temperature Variations
Temperature can have a significant impact on strain gauge performance. This aspect is essential because temperature fluctuations can alter the electrical resistance of the strain gauge materials, leading to inaccuracies in the readings. This means that, if the gauge is not compensated for temperature, the results can be skewed, making them unreliable.
A key characteristic of temperature variations is that it introduces a behavioral change in the strain gauges. Strain gauges, particularly those made from metallic materials, are sensitive to thermal expansion. They may expand or contract differently depending on their environment, which creates a challenge in maintaining precision. This makes understanding how temperature influences performance crucial for engineers and researchers.
Moreover, temperature considered during gauge calibration can help mitigate errors. However, this introduces another layer of complexity and demand for precision in calibration processes. Therefore, while temperature can be a double-edged sword, it is a pivotal parameter to account for in strain gauge applications.
Humidity Effects
Humidity can also play a significant role in influencing strain gauge measurements. High levels of moisture can affect the adhesive bond between the strain gauge and the substrate, leading to poor signal quality. This is particularly relevant in environments where moisture levels fluctuate frequently, causing variations in the readings that can be misleading.
The key feature of humidity's impact is its potential to alter the mechanical properties of the materials used in strain gauges, such as polymers and metallic components. As a result, it is essential to consider humidity effects when designing and implementing strain gauge systems. This knowledge helps in avoiding significant discrepancies that could arise from environmental influences.
While measuring in humid areas can pose its challenges, the existence of certain protective measures, such as conformal coatings, can enhance durability. Thus, while there are disadvantages to humidity effects, awareness and appropriate responses can mitigate its impact.
Measurement Accuracy Considerations
Calibration Difficulties
Calibration is another significant challenge in ensuring accurate measurements with strain gauges. It involves adjusting the gauge output to correspond with known values, but the calibration process is not always straightforward. One of the aspects contributing to difficulties in calibration is the variability in gauge performance over time due to wear, environmental conditions, or long-term exposure to stresses.
This characteristic makes calibration a recurrent necessity in applications requiring high precision. Calibration methods, while effective, can often lead to inconsistencies, particularly if the process is not meticulously executed. Therefore, understanding the calibration landscape is vital for ensuring that readings remain reliable across different environments or usage scenarios.
While calibration difficulties present challenges to those working with strain gauges, they also underscore the importance of periodic checks and maintenance for sustained accuracy. This reinforces a proactive approach towards measurement practices.
Signal Noise
Signal noise presents a substantial hurdle when dealing with strain gauge measurements. In many situations, the output from a strain gauge can be corrupted by electrical noise, originating from external sources or even from the gauge itself. Signal noise can mask the actual strains being measured, making it difficult to discern the true data required for analysis.
A defining feature of signal noise is that it can arise from various sources, whether they are electromagnetic interference from nearby equipment or thermal noise inherent in electrical components. Hence, addressing this concern is not just about isolating the gauge; it requires understanding the broader electrical ecosystem in which the gauge operates.
To combat signal noise, proper shielding techniques and filtering methods exist, but these solutions can add to the complexity and cost of strain gauge systems. Nonetheless, acknowledging the potential for signal noise allows for a more comprehensive risk assessment in strain gauge applications—ultimately leading to improved reliability in data collection.
In summary, recognizing the challenges and limitations faced by strain gauges, particularly concerning environmental factors and accuracy considerations, is vital for enhancing their reliability and effectiveness in various applications. Ultimately, maintaining vigilance concerning these aspects will contribute to more robust and favorable outcomes in engineering and scientific endeavors.
Future Perspectives
The exploration of strain gauge technologies continues to grow, drawing interest from various fields due to its critical role in precise measurement. As we venture into the future of this technology, it is vital to recognize how innovations and emerging research areas will shape its applications. The potential benefits that strai gauges bring in terms of accuracy, reliability, and versatility can't be overstated. With ongoing advancements, the landscape of what strain gauges can achieve keeps expanding, welcoming new challenges and opportunities.
Emerging Research Areas
Recent studies have shed light on several promising areas of research that can significantly enhance our understanding of strain gauges and their applications. These areas include:
- Material Science Innovations: Research focusing on new materials, such as graphene or bio-compatible polymers, could lead to the development of strain gauges with increased sensitivity and durability.
- Integration with IoT: The Internet of Things (IoT) is making waves throughout the engineering world. Investigating how to merge strain gauges with IoT devices fosters real-time data acquisition and monitoring, benefiting sectors like civil engineering and healthcare significantly.
- Nanotechnology Applications: The interplay between nanotechnology and strain gauge technology holds potential for miniature strain sensors capable of measuring slight deformations in intricate applications, such as electronic components in smartphones or biomedical devices.
- Advanced Data Processing: The advent of machine learning and AI is pushing the boundaries of data analysis. Incorporating these technologies into strain gauge readings could revolutionize predictive maintenance strategies in manufacturing, leading to cost savings and enhanced efficiency.
Each of these research areas stands at the forefront of innovation, promising to introduce better functionality and applications for strain gauges. The complexity of mechanical systems requires us to stay at the cutting edge of these developments.
Potential Innovations
Looking ahead, there are several innovations that could redefine how strain gauges are manufactured and utilized. Key potential innovations include:
- Smart Strain Gauges: With advancements in artificial intelligence, future strain gauges could possess onboard data processing. This would allow for swift analysis and decision-making without relying heavily on external systems.
- Biodegradable Strain Gauges: As sustainability becomes more vital, research into eco-friendly materials for strain gauges could lead to greener options that do not compromise on performance.
- Enhanced Telemetry: Innovations could lead to the creation of strain gauges with built-in telemetry, allowing for better long-range data transmission and less dependence on cabling and batteries.
- Expanded Functionality: Future designs might include multiple sensing capabilities, allowing a single gauge to measure strain, temperature, and even pressure simultaneously, thus providing a richer context for data interpretation.
As we ponder the future of strain gauge technology, it's clear that the blend of new materials, advanced data processing, and innovative designs will take these devices to the next level, helping various industries refine their measurement processes further.
"By combining cutting-edge technologies with strain gauge principles, the future surely looks bright for precision measurement devices, opening the door to a multitude of applications across sectors."
As students, researchers, and professionals delve into the future perspectives of strain gauge technology, they must keep an eye on how these advancements might transform existing applications and inspire new ones.
Finale
In wrapping up our exploration into strain gauges, a few key elements standout. These instruments have proven indispensable in a range of fields, from structural engineering to medical applications. Understanding their principles, placement in technological advancement, and the results they produce provides significant insight into their role in modern measurement techniques.
Recapitulation of Key Insights
As we dissected the world of strain gauges, several insights emerged:
- Core Functionality: Strain gauges measure deformation, giving vital feedback about material integrity. This means they’re not just numbers on a screen; they reflect safety, efficiency, and performance in varied contexts.
- Diverse Applications: From monitoring bridges and buildings to enhancing the design of prosthetics, the applications are as varied as they are crucial. Each application underscores the versatility of strain gauges in real-world use, illustrating their contribution to technical advancements.
- Technological Evolution: As we've seen, innovation drives the evolution of strain gauge technology. The shift towards wireless communications and the integration of smart materials signals a bright future for enhanced capabilities in strain measurement.
Final Thoughts on Future Directions
Looking ahead, several potential pathways for strain gauge technology could redefine its application:
- Wireless Technologies: Continued development in wireless strain gauges can lead to more straightforward installations and better data collection in hard-to-reach areas.
- Data Integration: The advent of IoT means strain gauges could become part of a larger data ecosystem, leading to smarter infrastructures and improved decision-making processes.
- Advanced Materials: Research into new materials, such as nanomaterials, may yield strain gauges with higher sensitivity, expanding their usage into more precise areas like nanoengineering.
As we venture further into the complexities of strain gauge applications, the intersection of traditional engineering with cutting-edge technology will likely provide exciting new solutions yet to be visualized.
In summary, strain gauges stand at the forefront of measurement technology. As the industry continues to evolve, staying informed about these advances can foster greater accuracy and safety across multiple sectors.