Exploring CFRP Materials: Properties and Future Trends
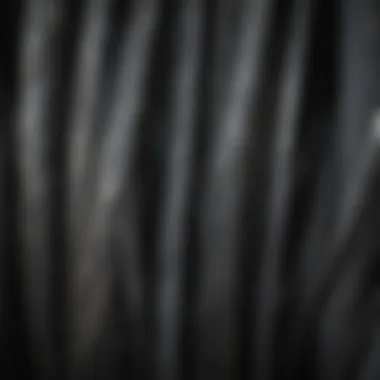
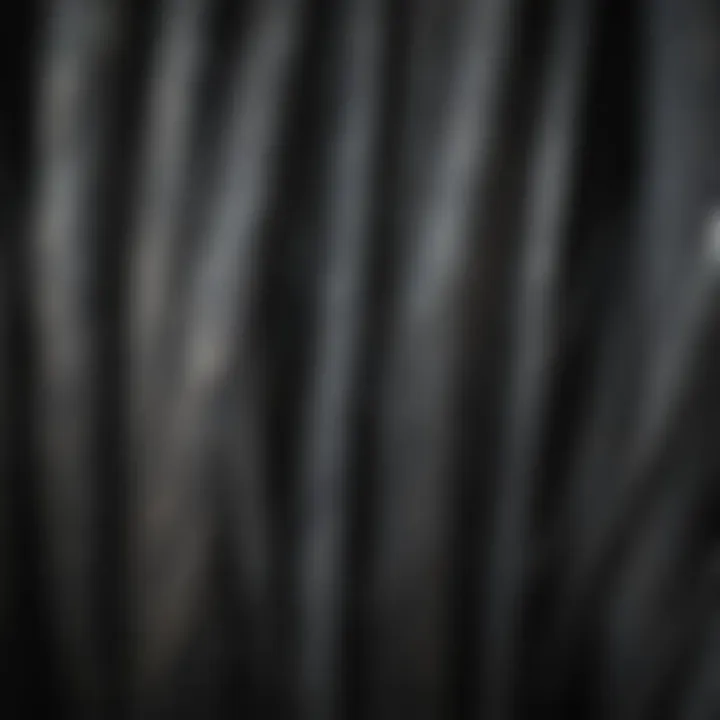
Intro
Carbon Fiber Reinforced Polymer, commonly known as CFRP, has become an essential material in various industries. This composite material consists of carbon fibers embedded in a polymer matrix, which enhances its strength-to-weight ratio significantly compared to traditional materials, like steel and aluminum. CFRP is not merely a replacement for other materials; it opens pathways for innovation in engineering, automotive, aerospace, and sports. This article aims to provide an in-depth exploration of CRFP, covering its properties, applications, current uses across industries, and potential future developments.
Understanding CFRP's role requires a look into its unique characteristics, such as high tensile strength, low density, and resistance to corrosion. Additionally, while the properties of CFRP confer specific advantages, several limitations also merit discussion. This exploration leads to a versatile understanding of CFRP, which is valuable to students, researchers, and industry professionals alike.
Preamble to CFRP Material
Carbon Fiber Reinforced Polymer (CFRP) has emerged as a material of choice in numerous high-performance applications across multiple industries. Understanding CFRP material is crucial due to its unique properties and applications. The ability to combine high tensile strength, lightweight, and corrosion resistance makes CFRP particularly attractive for aerospace, automotive, and construction sectors. The increasing demand for composite materials necessitates a thorough exploration of CFRP, especially as industries strive for greater efficiency and sustainability.
Definition and Composition
CFRP is a composite material made of carbon fibers embedded within a polymer matrix. The carbon fibers provide strength and rigidity, while the polymer matrix holds the fibers together and protects them from environmental degradation. The composition typically includes a thermosetting resin such as epoxy, which forms a strong bond with the carbon fibers. The ratio of fiber to matrix in CFRP can vary, influencing the overall mechanical properties.
This material exhibits excellent specific strength, meaning it possesses a high strength-to-weight ratio. For this reason, CFRP is widely used in applications where reducing weight without sacrificing strength is essential. The manufacturing processes to produce CFRP can differ, leading to variations in its properties.
History of CFRP Development
The development of CFRP materials began in the mid-20th century, with the first uses appearing in military and aerospace applications. Early carbon fibers were derived from rayon and later from polyacrylonitrile (PAN). Over the years, advancements in production techniques, including the introduction of filament winding and resin infusion methods, have increased the availability and performance of CFRP.
The aerospace industry recognized the potential of CFRP materials quickly due to their lightweight and strength, crucial considerations for aviation. In recent decades, the popularity of CFRP has expanded into the automotive and civil engineering sectors as manufacturers look to improve performance and sustainability.
As material technology continues to advance, research into enhancing CFRP properties, such as durability and impact resistance, is ongoing. This only adds to the relevance of CFRP in modern engineering and applications today.
Properties of CFRP
Understanding the properties of Carbon Fiber Reinforced Polymer (CFRP) is essential for various applications in industry. These properties not only define the material's performance but also dictate its suitability for specific environments and uses. Engineers and designers value CFRP for its unique characteristics which contribute significantly to advancements in technology and product design. The mechanical, thermal, and chemical properties of CFRP provide insight into its applications and the benefits that come with using it.
Mechanical Properties
Tensile Strength
Tensile strength refers to the maximum amount of tensile (stretching) stress that a material can withstand before failure. In the case of CFRP, this property is crucial because it indicates how much load the material can bear without breaking. A high tensile strength is one of the primary reasons CFRP is favored in construction. It allows for lighter structures without compromising safety. This unique feature of CFRP enables industries, especially aerospace, to innovate without the added weight impacting performance. The lightweight nature of this material makes it a beneficial choice, especially where reducing overall mass is necessary without sacrificing strength.
Flexural Strength
Flexural strength measures a material's ability to resist deformation under load. In CFRP, this aspect reinforces its application in scenarios where the material is subjected to bending forces. The key characteristic of flexural strength allows CFRP composites to endure considerable loads while maintaining form stability. This can be particularly beneficial in aerospace and automotive sectors where components are often subject to dynamic loads. The resilience of CFRP against bending makes it a preferred material in areas requiring durability and strength.
Shear Strength
Shear strength is the resistance of a material to sliding forces parallel to its surface. For CFRP, this property is significant because many applications, such as joints and connections in structures, require materials that can handle shear loads effectively. CFRP exhibits high shear strength, which makes it suitable for critical applications that demand stability under stress. The advantage of high shear strength in CFRP can be seen in wind turbine blades and aerospace components where safety and integrity are high priorities.
Thermal Properties
Thermal Conductivity
Thermal conductivity describes the ability of a material to conduct heat. CFRP has relatively low thermal conductivity compared to metals, making it a good insulating material. This property is valuable in applications where thermal management is critical, such as in aerospace and automotive industries. The unique feature of CFRP provides advantages in reducing unwanted heat transfer. This distinction makes CFRP a favorable option in instances needing effective thermal insulation.
Temperature Resistance
Temperature resistance indicates how well a material can withstand temperature fluctuations without degrading or losing functionality. CFRP materials are designed to perform effectively across a wide temperature range. This property enhances the material's applicability in environments where exposure to extreme temperatures is common. The stability of CFRP under varying temperature conditions enables consistent performance in critical settings, making it a reliable choice for many industrial applications.
Chemical Resistance
CFRP demonstrates a strong resistance to various chemicals, which is crucial for its use in environments where exposure to aggressive substances is common. This resilience to chemical degradation allows CFRP to maintain integrity and performance in harsh conditions, such as those found in the chemical processing industry. The ability to resist corrosion expands the range of applications for CFRP, providing significant advantages in extending the lifespan of structures and components that encounter chemicals regularly.
CFRP's diverse properties make it an adaptable material that serves a wide range of industries and applications while enhancing performance and innovation.
Understanding the properties of CFRP is invaluable for professionals within engineering, manufacturing, and applied sciences. Each mechanical, thermal, and chemical aspect contributes to the overarching value CFRP brings to numerous fields, making it a material of choice for future advancements.
Manufacturing Techniques of CFRP
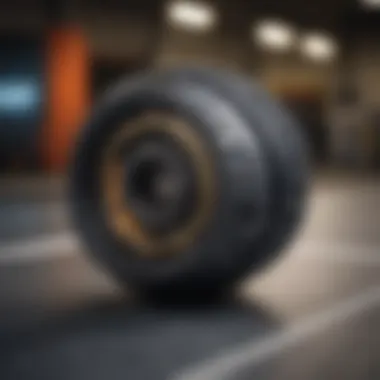
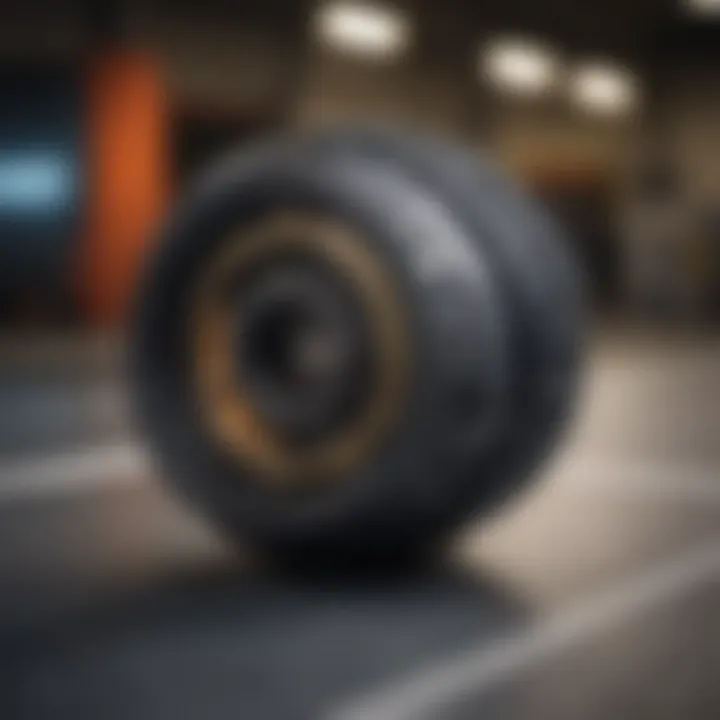
The manufacturing techniques of Carbon Fiber Reinforced Polymer (CFRP) are crucial for its application in various industries. Understanding these methods helps to appreciate how processing affects the properties of CFRP. Each technique offers different benefits and has specific considerations regarding cost, time, and material properties. This section will explore three prevalent techniques: lay-up process, resin transfer molding, and filament winding.
Lay-Up Process
The lay-up process is a traditional method for creating CFRP structures. It involves placing layers of carbon fiber fabric in a mold and applying resin to bond them together. This technique allows for precise control over the fiber orientation, which is essential for achieving desired mechanical properties.
There are two main types of lay-up: manual lay-up and automated lay-up. Manual lay-up is commonly used for prototypes and smaller production runs. It allows flexibility in design. However, the labor-intensive nature increases the risk of human error. Automated lay-up, on the other hand, is more efficient for large-scale production. It uses machines to place the fibers, ensuring consistency and quality.
Advantages of Lay-Up Process:
- Versatility: Can be used for complex shapes.
- Control: Fiber orientation can be tailored.
- Cost-effective: Suitable for low-volume production.
Resin Transfer Molding
Resin transfer molding (RTM) involves injecting resin into a closed mold that contains dry carbon fiber. This method is suitable for creating high-strength components with a good surface finish, making it a popular choice in automotive and aerospace applications.
RTM allows for better resin distribution, which reduces voids in the final product. The process is relatively quick, enabling higher production rates compared to manual lay-up techniques. Furthermore, it minimizes waste material, making it an environmentally friendly option.
Key Benefits of RTM:
- High-quality finish: Achieves superior surface properties.
- Efficiency: Faster production cycles.
- Material efficiency: Minimizes excess waste.
Filament Winding
Filament winding is a specialized manufacturing technique used primarily for creating cylindrical and spherical shapes. In this process, continuous strands of carbon fiber are wound around a mold while being saturated with resin. This method is particularly suitable for pressure vessels, pipes, and other tubular shapes.
One advantage of filament winding is the ability to control fiber placement precisely, which significantly enhances the strength-to-weight ratio of the final product. Additionally, it offers uniform thickness and minimal air entrapment, resulting in consistent quality of the finished item.
Advantages of Filament Winding:
- Strength: Optimal fiber alignment enhances performance.
- Uniformity: Consistent material properties throughout the structure.
- Reduced labor costs: Automation of the process is possible.
The choice of manufacturing technique significantly impacts the final performance and application of CFRP materials. Understanding these techniques is essential for optimizing the benefits of CFRP in various sectors.
Applications of CFRP
Carbon Fiber Reinforced Polymer (CFRP) is increasingly prominent in several industries due to its unique properties. Understanding the applications of CFRP is crucial for recognizing how this material can address various challenges. Its extensive use across fields such as aerospace, automotive, civil engineering, and sports is a testament to its versatility and benefits. This section will unravel the importance of CFRP applications by looking into specific sectors, examining the rationale behind its use, and exploring the advantages it brings.
Aerospace Industry
The aerospace sector has been a significant beneficiary of CFRP technology. Aircraft manufacturers utilize CFRP in components like wings, fuselage sections, and tail structures. The benefits include a lower weight, which contributes to fuel efficiency, and enhanced strength, allowing aircraft to handle various stresses during flight.
Moreover, CFRP demonstrates excellent resistance to corrosion, leading to reduced maintenance costs over the lifespan of the aircraft. This makes CFRP not just a lightweight choice but a cost-effective one in the long run. With aerospace regulations becoming stricter, adapting to CFRP can provide companies a competitive advantage in meeting performance criteria.
Automotive Sector
In the automotive industry, CFRP is increasingly used in high-performance vehicles. Components such as body panels, chassis parts, and interior elements benefit from the high strength-to-weight ratio of CFRP. As automakers strive to make vehicles more fuel-efficient, minimizing weight is essential.
Furthermore, CFRP's ability to absorb energy during impacts adds a layer of safety to vehicles. While the initial cost is high, the performance characteristics and long-term savings in fuel consumption often justify the investment. Moreover, leading companies, like BMW and McLaren, have been pivotal in showcasing what CFRP can do for modern vehicles, thus influencing industry trends.
Civil Engineering
CFRP is not limited to aerospace and automotive sectors; it plays a crucial role in civil engineering. This material is used in structural reinforcement, especially in retrofitting existing structures. Beams and columns can be wrapped in CFRP to enhance their load-bearing capacity, accommodating increasing demands on aging infrastructures.
The lightweight nature of CFRP also simplifies handling during installations, making it easier to work with in complex urban environments. Moreover, its corrosion resistance adds a significant advantage in applications exposed to environmental stressors, extending the useful life of structures.
Sports Equipment
In sports equipment, CFRP finds applications in producing lightweight and durable items like bicycles, tennis rackets, and golf clubs. The use of CFRP allows manufacturers to create high-performance gear that enhances athletic capability through weight reduction and stiffness. This directly influences athletes' performance as they can leverage equipment that does not hinder their movements.
In summary, the applications of CFRP are wide-ranging and impactful across several domains. Its properties lead to enhancements in efficiency, strength, and durability. Understanding these applications provides insight into why CFRP is a focal point in ongoing research and development.
Advantages of CFRP Materials
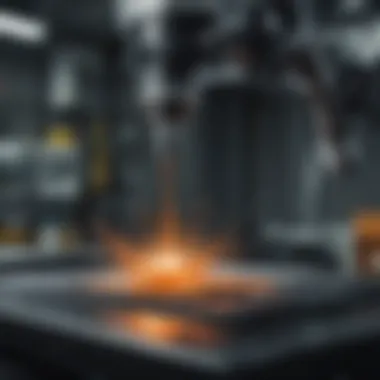
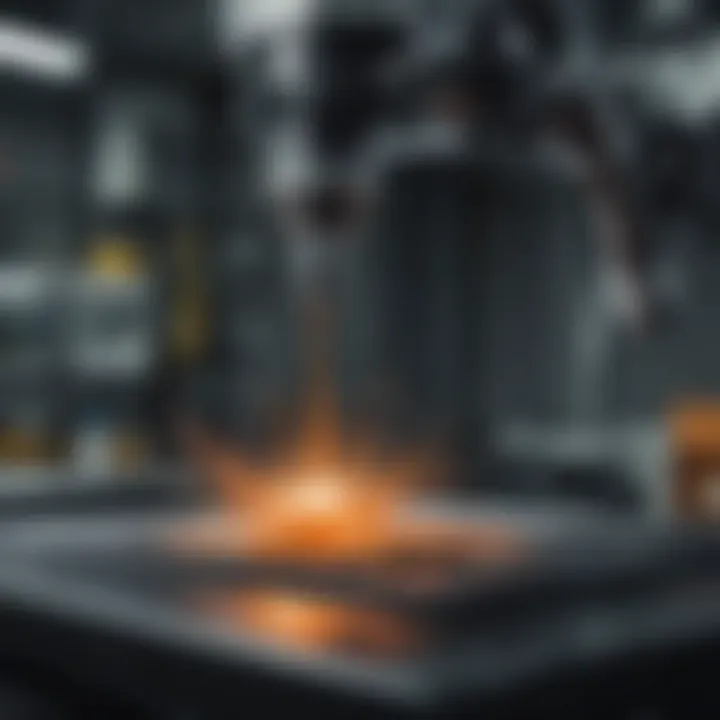
The merits of Carbon Fiber Reinforced Polymer (CFRP) materials are significant and play a pivotal role in numerous applications. Each advantage contributes to the material's overall efficacy in various industries. Tackling the strengths of CFRP can enhance understanding and inspire further utilization in innovative designs.
High Strength to Weight Ratio
CFRP materials possess an exceptional strength-to-weight ratio. This characteristic is essential in sectors where performance and efficiency are paramount. For example, in aerospace and automotive industries, the need for lightweight yet strong materials is critical. Reducing weight directly contributes to improved fuel efficiency and enhanced performance. Thanks to its impressive properties, CFRP is often the go-to material for components that require both lightweight construction and high durability.
- Key points about high strength to weight ratio include:
- Lower energy consumption in transportation.
- Increased payload capacity in aircraft and vehicles.
- Enhanced design possibilities with strength optimization.
Corrosion Resistance
Another advantage of CFRP is its inherent corrosion resistance. Unlike metals which can be vulnerable to rust and degradation from chemical exposure, CFRP remains stable in harsh conditions. This property is particularly valuable in outdoor applications, marine environments, and chemical processing industries. The longevity of CFRP reduces the need for frequent replacements and maintenance, ultimately leading to cost savings over time.
- Advantages of corrosion resistance include:
- Increased lifespan of components.
- Reduced maintenance costs and downtime.
- Broad usability across various environments, including chemically aggressive settings.
Design Flexibility
CFRP offers considerable design flexibility, allowing engineers and designers to create complex shapes and structures with ease. This capability is particularly beneficial in industries where aerodynamics and aesthetics are crucial. Moreover, the ability to mold CFRP into specific designs can lead to innovative product developments that might not be feasible with traditional materials. Designers can explore unique forms that optimize performance while maintaining visual appeal.
- Aspects of design flexibility include:
- Customization for specific applications.
- Architectural creativity in civil projects.
- Potential for intergrative designs with other materials.
The advantages of CFRP materials not only contribute to current applications but also open pathways to future innovations. Understanding these benefits can drive more effective use of CFRP in diverse fields.
Limitations of CFRP
Understanding the limitations of Carbon Fiber Reinforced Polymer (CFRP) materials is essential for making informed decisions in their applications. While CFRP offers numerous advantages, such as high strength-to-weight ratio and design flexibility, there are critical constraints one must address. This section examines three main limitations: cost considerations, difficulties in repair, and environmental impact.
Cost Considerations
CFRP is not the most economical material available in the market. The initial costs associated with manufacturing CFRP components can be significantly higher than traditional materials like metals or plastics. This cost largely stems from the complexities involved in the production process, as well as the price of carbon fibers themselves. For instance:
- Raw Material Expenses: Carbon fibers are expensive compared to most alternatives. The cost of production can vary depending on the type and quality of fibers used.
- Manufacturing Techniques: Advanced processes such as resin transfer molding and filament winding require specialized equipment and skilled labor, contributing to higher costs.
In many cases, companies must weigh whether the performance benefits of CFRP justify the investment. For lower-end applications or where cost is a priority, alternative materials may be more suitable.
Difficulties in Repair
CFRP materials pose unique challenges when it comes to repair. Unlike metals that can be welded or mechanically fastened, repairing CFRP can be considerably more complicated. This complexity arises from:
- Layered Structure: CFRP is made up of multiple layers of carbon fiber and resin. Damaging one layer can compromise the integrity of the entire structure.
- Specialized Techniques: Repairing CFRP often requires advanced techniques, such as the use of additional resin or bonding agents. This can be time-consuming and may involve significant costs.
These difficulties present a notable issue, particularly in applications where downtime must be minimized, such as in the aerospace and automotive industries.
Environmental Impact
The environmental footprint of CFRP is a significant consideration. While CFRP itself is durable and can be recycled to some extent, its production raises several concerns:
- Energy-Intensive Process: Manufacturing CFRP requires significant energy consumption, leading to higher carbon footprints compared to traditional materials.
- Disposal Issues: End-of-life disposal of CFRP products poses challenges, as they are not biodegradable. Proper recycling methods are limited, and many CFRP components end up in landfills.
This aspect of CFRP use is subject to increasing scrutiny, especially as industries move towards more sustainable practices.
"While CFRP boasts impressive performance characteristics, its limitations must be critically assessed to ensure responsible usage in various applications."
Addressing these limitations is crucial for researchers and industry professionals. Understanding both the capabilities and constraints of CFRP will lead to better material choices and potential innovations in the future.
Current Research and Innovations
In the rapidly evolving field of materials science, Carbon Fiber Reinforced Polymer (CFRP) is at the forefront due to its unique properties and numerous applications. This section delves into current research and innovations that are pushing the boundaries of CFRP technology. The exploration of nanocomposites and green manufacturing processes highlights not only the potential enhancements in material performance but also the shift towards sustainable practices in the industry.
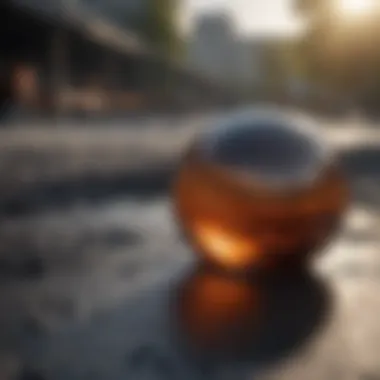
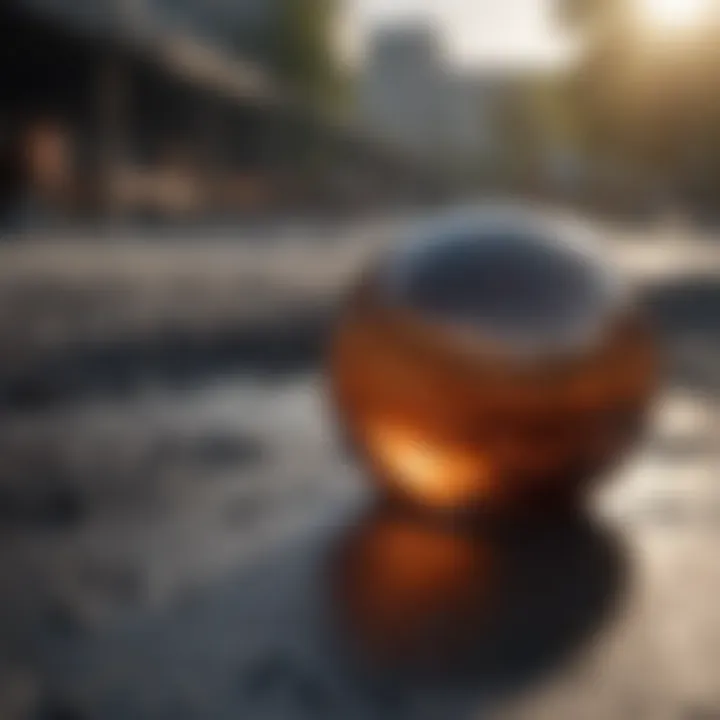
Nanocomposites in CFRP
Nanocomposites represent a significant advancement in the field of CFRP materials. By integrating nanomaterials, such as carbon nanotubes or graphene, into the polymer matrix, researchers aim to enhance the mechanical and thermal properties of CFRP. These additions can result in increased tensile strength and improved thermal stability. Several studies have shown that even a small amount of nanomaterial can significantly alter the overall performance of CFRP components.
The benefits of utilizing nanocomposites in CFRP include:
- Improved mechanical properties: The incorporation of nanofillers can lead to tougher and more resilient materials.
- Lightweight nature: Maintaining low weight while enhancing performance is crucial in applications such as aerospace and automotive industries.
- Enhanced durability: Nanocomposites may contribute to better resistance against environmental stressors, resulting in a longer lifespan of the materials.
This ongoing research signifies a shift towards smarter materials that can adapt and perform under various conditions, which could lead to widespread adoption across industries.
Green Manufacturing Processes
Green manufacturing processes are becoming an essential focus within the CFRP sector. As the global emphasis on sustainability grows, researchers and manufacturers seek ways to create CFRP with a reduced environmental footprint. This involves both developing eco-friendly resins and optimizing production techniques.
Key aspects of green manufacturing processes include:
- Biobased Resins: Utilizing resins derived from renewable sources can significantly lessen the environmental impact compared to traditional petroleum-based materials.
- Recycling Techniques: Innovative methods are being explored to recycle CFRP waste, thus minimizing landfill contributions. Techniques like pyrolysis are investigated to recover fibers and resins.
- Energy Efficiency: Implementing more energy-efficient production methods contributes to lower greenhouse gas emissions during manufacturing, aligning with global sustainability goals.
Adopting green practices not only benefits the environment but also enhances the marketability of CFRP products, as consumers and companies alike are increasingly prioritizing sustainability. This proactive approach to manufacturing indicates a promising future for CFRP in diverse applications, adhering to both performance and ecological standards.
"Innovations in CFRP not only enhance material properties but also align with sustainability efforts, proving that performance and eco-consciousness can coexist."
These research directions evoke interest and underline the importance of continual advancements in CFRP technology, reflecting a future rich with potential while addressing critical global challenges.
Future Directions for CFRP
The exploration of Carbon Fiber Reinforced Polymer (CFRP) extends beyond its current applications and advantages. Understanding the future directions for CFRP is critical for professionals, researchers, and organizations aiming to harness the full potential of this composite material. The current trends indicate that the ongoing advancements in technology, coupled with increasing demands for performance and sustainability, are shaping new pathways for CFRP utilization.
Emerging Applications
CFRP materials have found success in a variety of sectors, yet several emerging applications promise to redefine their market scope. One noteworthy domain is the renewable energy sector. With the global push towards clean energy, CFRP is being integrated into the design and production of wind turbine blades, where their lightweight nature can enhance efficiency and durability.
Additionally, potential applications in medical technology are gaining traction. CFRP's biocompatibility and strength can be advantageous in creating prosthetic devices or surgical instruments. Another field with prospective growth is the construction industry, where CFRP can be leveraged for reinforcing structures, offering both strength and resistance to environmental factors.
Here are some potential emerging applications for CFRP:
- Automotive lightweighting: Improving fuel efficiency by reducing weight in vehicles.
- Aerospace components: Ensuring performance while minimizing weight for improved fuel economy.
- Consumer electronics: Producing lightweight casings and components.
- Sports equipment: Enhancing performance characteristics in gear and apparel.
Regulatory Frameworks
As CFRP technologies evolve, regulatory frameworks play an essential role in guiding its development. Establishing regulations ensures safety, promotes sustainability, and governs materials' usage in various applications. Considerations such as production practices, end-of-life disposal, and recyclability have become increasingly vital in the formulation of these frameworks.
Organizations and governments worldwide are striving for regulations that accommodate the rapid innovation of CFRP while maintaining stringent safety and environmental standards. Key elements of these frameworks may include:
- Safety standards for the production and use of CFRP materials in construction and transportation.
- Recycling guidelines to promote sustainable practices and reduce waste.
- Environmental assessments to evaluate the life cycle impacts of CFRP products.
Compliance with established regulatory frameworks will enhance consumer confidence and encourage further research and investment in CFRP technology.
Closure
The conclusion is essential in any piece of scholarly work, especially in a detailed analysis of Carbon Fiber Reinforced Polymer (CFRP) materials. It serves as a synthesis of the main themes discussed throughout the article. After exploring properties, applications, and future directions of CFRP, the conclusion highlights the significance of comprehensive knowledge about this material. Understanding CFRP not only supports engineering advancements but also facilitates informed decisions in design and manufacturing across multiple industries.
In this article, we examined key properties such as mechanical, thermal, and chemical attributes of CFRP, providing a robust understanding of its performance characteristics. The applications in aerospace, automotive, civil engineering, and sports equipment underscore the versatility of CFRP as a material choice, driven by its unique advantages. Additionally, the discussion of current research and emerging innovations places CFRP at the forefront of material science developments.
"The environmental impact and limitations in repair and cost considerations warrant further investigation, especially as industries seek sustainable solutions."
The conclusion serves to reinforce the need for continuous exploration in CFRP technologies, ensuring that stakeholders are aware of potential environmental considerations and seeking ways to mitigate them. As users of CFRP grow more informed, the industry can advance responsibly while maximizing the benefits of this remarkable material.
Summary of Key Points
- Comprehensive Analysis: The article provided an in-depth exploration of CFRP, from its composition to its diverse applications and limitations.
- Unique Properties: CFRP offers outstanding mechanical strength, thermal resilience, and chemical resistance. These properties make it ideal for various demanding applications.
- Wide Applications: Industries such as aerospace and automotive benefit significantly from CFRP, enhancing performance while also reducing weight.
- Advantages and Limitations: The advantages of CFRP include high strength-to-weight ratio and corrosion resistance, but factors like cost and repair difficulties need consideration.
- Research and Innovations: Advancements like nanocomposites and green manufacturing processes show promise in improving CFRP application and sustainability.
Recommendations for Further Study
The exploration of CFRP materials is far from complete, and several areas merit further research:
- Environmental Impact Assessments: More studies are needed to understand the life cycle of CFRP materials, from production to disposal.
- Repair Techniques: Investigating effective strategies for repairing CFRP structures will enhance their usability and longevity in various applications.
- Cost-Effective Alternatives: Researching lower-cost substitutes or hybrids that maintain performance while being affordable will broaden market access.
- Regulatory Frameworks: As CFRP becomes more prevalent, clear guidelines and standards for its use, recycling, and environmental impact are essential.
- Emerging Applications: Continued investigation into novel uses of CFRP in sectors like renewable energy or medical devices could highlight yet untapped potential.
Researchers, educators, and industry professionals should collaborate to foster innovation and address challenges in CFRP technologies. Keeping abreast of advancements will ensure that users unlock the full potential of this critical material.