Understanding Aluminium Alloys: Composition and Uses

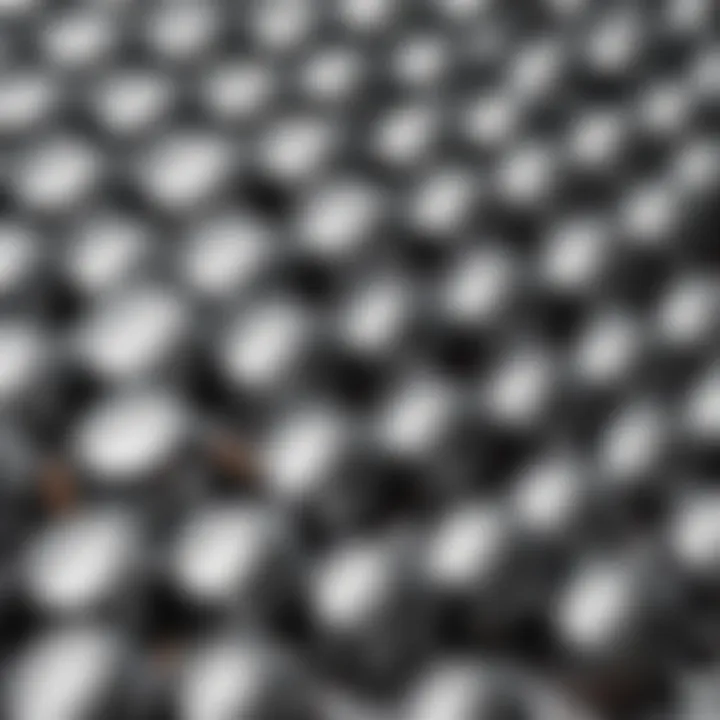
Intro
Aluminium alloys play a crucial role in many industries. These materials, formed by combining aluminium with other elements, exhibit a variety of properties that can be tailored for specific applications. Understanding the composition, characteristics, and uses of these alloys is essential for professionals in engineering, manufacturing, and design.
In this guide, we will explore the intricacies of aluminium alloys, covering the different types, their production methods, and the significance of their mechanical properties. As we delve deeper into the subject, the relevance of these materials in modern technology and manufacturing will become clear.
Intro to Aluminium Alloys
Aluminium alloys play a vital role in the development of various industries, making their understanding crucial for anyone involved in materials science or engineering. Aluminium is valued for its favorable balance between strength, weight, and corrosion resistance. These attributes make aluminium alloys suitable for diverse applications, from aerospace to automotive and beyond.
Definition of Aluminium Alloys
Aluminium alloys consist of aluminium and other elements, which are added to enhance specific properties. The primary purpose of alloying is to improve characteristics such as strength, ductility, and resistance to corrosion. Different types of elements can be introduced, resulting in a wide array of aluminium alloy categories suitable for various applications. This distinction is essential for professionals who choose materials based on specific performance requirements.
Historical Development of Aluminium Alloys
The journey of aluminium alloys begins in the 19th century when scientists first recognized the potential of aluminium for industrial applications. The first notable production of aluminium occurred in 1825, but it was not until the advent of the Hall-Héroult process in 1886 that large-scale production became feasible.
Over the years, extensive research led to the creation of numerous aluminium alloys. In World War II, aluminium alloys gained attention for their lightweight nature, boosting aircraft efficiency and performance. Advancements in metallurgy and processing techniques have further propelled the development of aluminium alloys. Today, they are integral materials in construction, transportation, and consumer goods. Their evolution mirrors the increasing demands of modern engineering and technology.
"The history of aluminium alloys is a testament to innovation in material science, reflecting society's continuous quest for efficiency and sustainability."
In summary, aluminium alloys are a significant area of study due to their diverse properties and applications. Understanding their composition and development is essential for leveraging their benefits in current and future projects.
Basic Composition of Aluminium Alloys
Understanding the basic composition of aluminium alloys is imperative to recognizing their utility and performance across various applications. Aluminium alloys are primarily composed of aluminium combined with different other elements. These elements are stratgically selected to enhance the physical and mechanical properties of aluminium, making it adaptable for diverse uses in industries such as aerospace, automotive, and construction.
The composition not only determines the performance characteristics like strength, ductility, and corrosion resistance, but also influences production methods and cost-efficiency. Consequently, knowledge of alloy composition is paramount for engineers, designers, and manufacturers.
Primary Elements in Aluminium Alloys
The primary element in all aluminium alloys is aluminium itself, usually comprising over 90% of the alloy's total weight. This metal is valued for its lightweight nature, excellent corrosion resistance, and favorable conductivity properties.
Aside from aluminium, alloying elements play an essential role in defining the characteristics of the final product. Common primary elements include:
- Copper: Enhances strength and improves machinability. It is often found in 2000-series alloys.
- Magnesium: Provides significant strength and toughness, largely in 5000-series alloys.
- Silicon: Increases fluidity for casting applications and reduces thermal expansion in alloys.
- Zinc: Promotes high strength, specifically in 7000-series alloys.
These primary elements are integral to the structure of aluminium alloys. They work in conjunction with aluminium to create materials that meet the specific needs of various applications.
Secondary Elements and Their Effects
Secondary elements offer additional benefits and fine-tune the qualities of aluminium alloys beyond the enhancements provided by primary elements. Their concentrations and combinations can lead to varied outcomes. Some common secondary elements and their significant effects include:
- Manganese: Increases resistance to wear and improves corrosion resistance, especially in 3000-series alloys.
- Lithium: Lightens the alloy while increasing specific strength, leading to applications in the aerospace segment for lighter structures.
- Titanium: Enhances the strength without adding significant weight and improves weldability.
These secondary elements can be added in smaller amounts but can have substantial impacts on alloy performance. Adjusting their levels allows material engineers to tailor aluminium alloys for the intended end-use, maximizing their effectiveness.
"In the realm of material science, the understanding of compositional influences is key to innovation in aluminium alloy applications. Each alloy serves a unique purpose, dictated by its elemental makeup."
In sum, the basic composition of aluminium alloys lays the groundwork for understanding their diverse applications. By meticulously selecting both primary and secondary elements, manufacturers can engineer alloys that not only meet but exceed performance expectations across various sectors.
Classification of Aluminium Alloys
The classification of aluminium alloys is not just a technical detail, but an essential framework for understanding their characteristics and applications. These classifications provide insight into the different functionalities and properties of the alloys. They highlight how structural needs, mechanical performance, and manufacturability influence the choice of alloy in diverse professional fields, such as aerospace, automotive, and construction. Furthermore, recognizing these distinctions is crucial for optimizing product performance and ensuring sustainability in their use.
Wrought Aluminium Alloys
Wrought aluminium alloys are formed through mechanical processes, which include rolling, extrusion, and forging. They are generally characterized by superior strength and ductility. These alloys undergo plastic deformation at elevated temperatures, which improves their mechanical properties. The series of wrought aluminium alloys is usually designated by a four-digit system, where the first digit represents the main alloying element. For instance, 1000 series alloys contain 99% or higher aluminium content, making them highly resistant to corrosion and distinctly ductile.
Typical applications of wrought alloys include:
- Aircraft structures: For their lightweight and strong characteristics.
- Automotive components: In body panels and structural parts to reduce weight and improve fuel efficiency.
- Construction materials: Used in window frames and building facades for both strength and aesthetic appeal.
Higher strength levels in some wrought alloys can be achieved through strain hardening and heat treatment. However, the degree of heat treatment applicability varies among different alloys.
Cast Aluminium Alloys
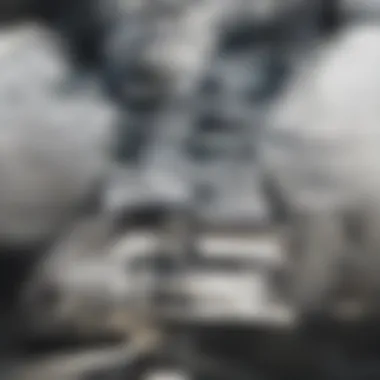
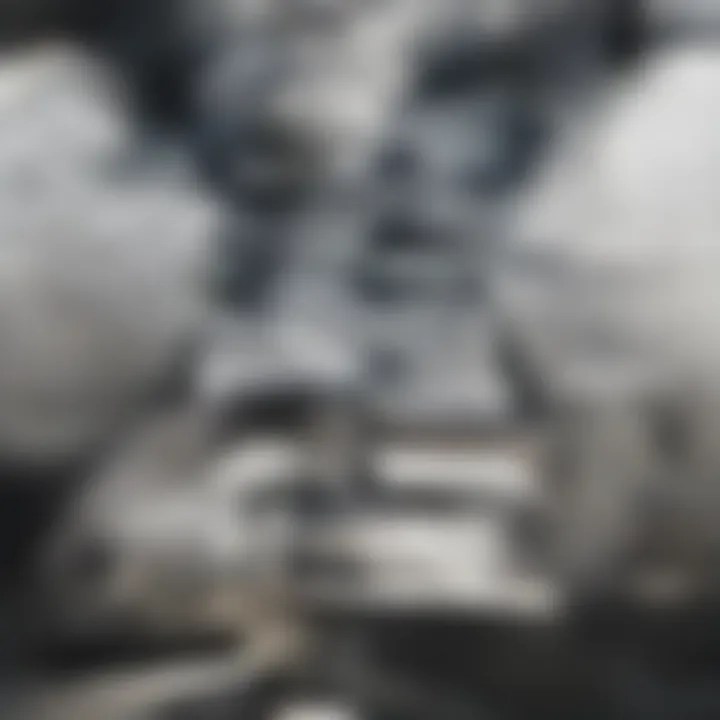
Cast aluminium alloys, on the other hand, are produced by pouring molten aluminium into a mold. This category of alloys is advantageous due to its ability to form complex shapes and internal structures that would be difficult to achieve with wrought methods. Cast alloys are designated using a system denoted by a four-digit number, beginning with a 1 or 2, reflecting different alloying elements. For example, the 2xx.x series primarily includes copper as the principal alloying element, known for high strength, but generally more susceptible to corrosion.
Applications of cast aluminium alloys can be found in:
- Engine components: Such as cylinder heads and engine blocks.
- Household products: Including cookware and appliances due to excellent corrosion resistance.
- Automotive parts: Wheels and transmission housings benefit from complex shapes that cast alloys provide.
The versatility of casting allows for enhanced design flexibility but can lead to varied mechanical properties compared to wrought alloys, making selection essential for specific applications.
Heat-Treatable vs Non-Heat-Treatable Alloys
When distinguishing alloys, understanding the heat-treatable and non-heat-treatable categories is vital. Heat-treatable alloys can develop increased strength through processed heating, followed by controlled cooling. This process is typically applicable to alloys in the 2xxx, 6xxx, and 7xxx series, much of which contain copper, magnesium, or zinc as alloying elements. The heat treatment process substantially enhances their tensile and yield strength, prominently valued in aerospace and automotive applications.
Conversely, non-heat-treatable alloys, primarily found in the 1xxx, 3xxx, and 4xxx series, usually rely on solid solution strengthening. These alloys do not gain strength through heat treatment due to their alloying elements' nature. They still offer vital attributes like excellent corrosion resistance and highworkability, making them suitable for applications where strength demands are less rigorous.
Properties of Aluminium Alloys
The properties of aluminium alloys are crucial for understanding their suitability in various applications. These alloys possess a range of characteristics that directly influence their performance in different environments. Key properties, such as mechanical properties, physical properties, and corrosion resistance, determine how aluminium alloys behave under stress, their usability in diverse sectors, and their durability over time. This section explores these properties in detail and highlights their significance for engineers and designers.
Mechanical Properties
Mechanical properties refer to the response of materials under applied forces. This includes factors such as tensile strength, yield strength, and hardness. Understanding these aspects is vital for engineers who design components that require specific performance characteristics.
Tensile Strength
Tensile strength is the maximum stress that a material can withstand while being stretched or pulled before breaking. This property is fundamental in determining how well an aluminium alloy can perform in structural applications. The key characteristic of tensile strength is its ability to indicate material behavior under tension.
Aluminium alloys, particularly those like 6061 and 7075, are recognized for their high tensile strength relative to weight. This makes them beneficial for aerospace and automotive sectors, where weight savings contribute to overall efficiency. However, a disadvantage can arise in some alloys that, while strong, may also become brittle under certain conditions, which may not be favorable in some scenarios.
Yield Strength
Yield strength indicates the stress at which a material begins to deform plastically. Understanding yield strength is essential for applications where deformation is not permissible. A high yield strength esures that components maintain their shape under load.
Aluminium alloys with high yield points, such as 7075-T6, are often favored in high-performance applications. This makes them popular among industries requiring stringent tolerance, such as aerospace. The unique feature of yield strength in aluminium alloys is its ability to balance robustness with weight, yet the increased performance can sometimes lead to higher costs in alloy production.
Hardness
Hardness measures a material's resistance to deformation, particularly permanent deformation, indentation, or scratching. It is significant in assessing wear resistance. The key characteristic of hardness is its correlation with the durability of components subjected to abrasion.
Aluminium alloys offer variable hardness levels, often enhanced through heat treatments. Alloys like 2024 are noted for their hardness, making them beneficial in applications like military and aerospace where wear resistance is critical. However, very hard alloys can be less ductile, limiting their applications in situations where flexibility is needed.
Physical Properties
Physical properties further define aluminium alloys and their behavior in different environments. These include ductility, thermal conductivity, and electrical conductivity. Each of these properties determines the alloy's usability across multiple facets of can engineering.
Ductility
Ductility describes the ability of a material to undergo significant plastic deformation before rupture. This property is vital for materials that need to be formed or shaped into specific forms. The key characteristic of ductility in aluminium is its capacity to be easily fabricated and worked into products such as wires or sheets.
Aluminium alloys, such as 1100, are highly ductile, making them beneficial in manufacturing processes where forming is necessary. However, alloys with higher strength may exhibit lower ductility, leading to challenges during processing.
Thermal Conductivity
Thermal conductivity measures a material's ability to conduct heat. This property is especially important in applications requiring effective heat dissipation. The key characteristic of aluminium alloys in this realm is their relative high thermal conductivity compared to other metals.
High thermal conductivity makes aluminium alloys beneficial in electronic and heat exchanging applications, such as heat sinks and radiators. On the downside, efficiencies can vary based on alloy composition, affecting application suitability.
Electrical Conductivity
Electrical conductivity indicates how well a material transmits electricity. This characteristic is essential for alloys considered for electrical applications. Aluminium alloys, such as 1350, have good electrical conductivity, making them popular for power transmission lines and connectors.
However, it is crucial to balance conductivity with other factors such as strength, as some high-strength alloys may sacrifice conductivity, which can be a disadvantage in electrical applications.
Corrosion Resistance
Corrosion resistance is a vital property for materials used in demanding environments. Aluminium alloys form a protective oxide layer that enhances their durability and extends their lifespan. This makes them suitable for applications in marine, automotive, and aerospace environments where exposure to harsh conditions is expected.
Corrosion resistance varies depending on the alloy's composition and the treatment it undergoes. Slightly less resistant alloys can be improved using coatings or anodizing, which provide additional protection. Therefore, understanding how to optimize corrosion resistance is essential for selecting the right aluminium alloy for specific applications.
Production Methods of Aluminium Alloys
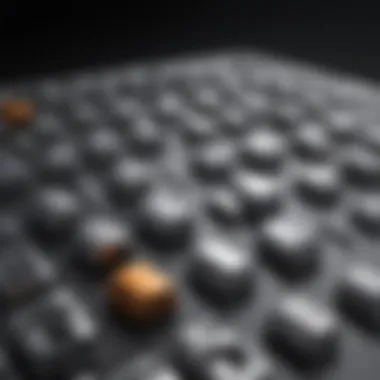
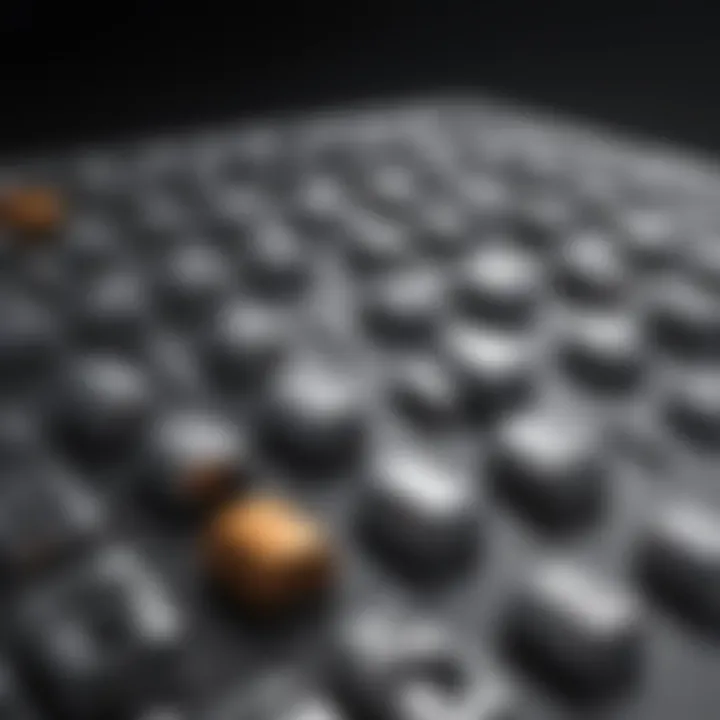
The production of aluminium alloys is critical to their final properties and applications. Understanding the methods used for producing these alloys is essential for optimizing their performance in various industries. This section will explore the main production techniques, which can broadly be categorized into primary and secondary production methods. Each technique has its unique advantages and disadvantages, impacting the properties and uses of the resulting alloys.
Primary Production Techniques
Bauxite Mining
Bauxite mining is the first step in the primary production of aluminium. Bauxite is the primary ore from which aluminium is extracted. The mining process involves extracting bauxite from the earth, typically found in tropical and subtropical regions. This raw material is rich in aluminium oxide, which is crucial for producing aluminium.
The key characteristic of bauxite mining is that it provides the necessary raw material for the aluminium production process. Its abundance in certain geographical areas makes it a popular choice for aluminium production. Additionally, bauxite's relatively low extraction cost allows for more economical production.
However, the unique feature of bauxite mining lies in its environmental impact. The extraction process can lead to deforestation and soil erosion. Thus, while it serves the essential role of supplying raw materials, it also poses significant challenges regarding sustainability.
Electrolytic Reduction
Electrolytic reduction is the next crucial step after bauxite mining. This process involves dissolving aluminium oxide in molten cryolite and then passing an electric current through it. This electric current separates the aluminium ions from oxygen, allowing for the metal's extraction.
The key characteristic of electrolytic reduction is its efficiency. It allows for the production of high-purity aluminium, which is crucial for applications demanding specific properties. The process is also energy-intensive, but it remains a critical choice for primary aluminium production because of the quality it offers.
A unique feature of electrolytic reduction is its role in minimizing impurities in the final aluminium product. However, this method requires significant amounts of electricity, which raises concerns about energy consumption and associated costs.
Secondary Production Techniques
Secondary production techniques involve recycling and repurposing aluminium to create new alloys. This process is crucial for reducing waste and improving sustainability within the industry.
Recycling of Aluminium
The recycling of aluminium is an essential aspect of secondary production methods. Recycling involves collecting and processing scrap aluminium to produce new aluminium alloys. This method contributes significantly to reducing the carbon footprint associated with aluminium production.
The key characteristic of recycling is its efficiency. Approximately 95% of the energy required to produce aluminium from bauxite can be saved when recycling. This method is increasingly popular as industries seek to lower their environmental impact.
A unique feature of recycling is that it does not compromise the quality of the aluminium produced. However, the recycling process can face challenges in the form of contamination from other materials, which may require additional processing to ensure purity.
Alloying Processes
Alloying processes are another significant aspect of secondary production techniques. This involves combining aluminium with other metals to enhance specific properties such as strength, corrosion resistance, and durability. Common alloying elements include copper, magnesium, silicon, and zinc.
The key characteristic of alloying processes is their ability to tailor aluminium to meet the demands of various applications. This customization makes aluminium alloys versatile and widely used in many sectors, including aerospace and automotive.
A unique feature of alloying is its role in improving material properties. However, it requires careful control of the alloying elements to prevent undesired characteristics in the final product.
"The production methods for aluminium alloys play a vital role in determining their characteristics and applications, making an understanding of these methods essential for professionals in the field."
Overall, the production methods of aluminium alloys significantly impact the final product's attributes and sustainability. It is important for researchers, manufacturers, and industry professionals to understand both primary and secondary techniques to enhance the use and efficiency of aluminium alloys.
Heat Treatment of Aluminium Alloys
Heat treatment is crucial for enhancing the properties of aluminium alloys. This process involves applying heat under controlled conditions to alter their physical and sometimes chemical properties. Through heat treatment, aluminium alloys can achieve specific characteristics that improve their performance in various applications. The main objective of heat treatment is to tailor the mechanical properties of the alloys, making them suitable for highly demanding environments and uses.
Types of Heat Treatment
Solution Treatment
Solution treatment is one effective method employed in the heat treatment of aluminium alloys. This process involves heating the alloy to a temperature that allows the alloying elements to dissolve into the aluminum matrix. It is followed by rapid cooling, usually through water quenching. The key characteristic of solution treatment is its ability to increase the alloy’s ductility and toughness by distributing alloying elements uniformly throughout the matrix.
Solution treatment is a beneficial choice in many industrial applications. It significantly enhances strength and corrosion resistance. However, one disadvantage includes the potential that some alloying elements might not remain in solution, which necessitates careful thermal management during the heating cycle.
Age Hardening
Age hardening, also known as precipitation hardening, is another vital heat treatment process. It involves heating the alloy to dissolve the solute atoms and then cooling it down. After that, the alloy is aged at a lower temperature, allowing precipitates to form. This process increases the strength of the alloy considerably. The key feature of age hardening is its efficiency in enhancing hardness and strength through microstructural changes.
Age hardening is popular due to its effectiveness in producing high-strength materials. It plays a crucial role in industries requiring lightweight yet strong materials, such as aerospace and automotive. However, age hardening also has its challenges. It can lead to reduced ductility if the aging period is too long, thus requiring careful optimization of time and temperature during the aging phase.
Effects on Material Properties
The heat treatment processes significantly influence the material properties of aluminium alloys. These effects can include improvements in tensile strength and yield strength, which are essential for structural applications. Additionally, heat treatment can enhance hardness, making the alloys more resistant to wear and deformation.
Moreover, the thermal treatments can influence properties like ductility and toughness. While ductility may temporarily decrease during some processes, proper management of heat cycles can restore it effectively. Overall, understanding the heat treatment of aluminium alloys allows for the capability to produce and utilize materials optimized for specific engineering requirements.
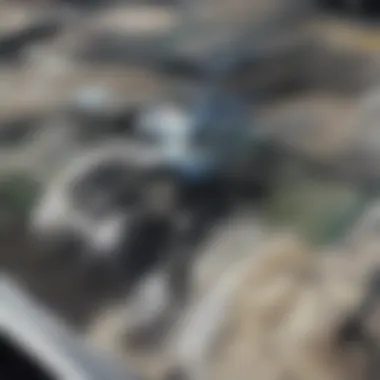
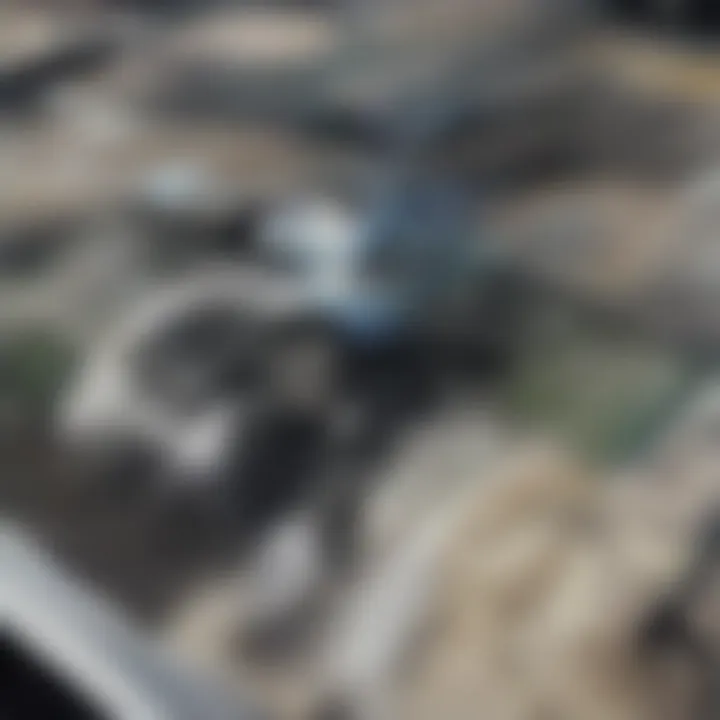
The appropriate heat treatment can transform a basic aluminium alloy into a high-performance material suitable for various applications, showcasing the versatility of aluminium in modern technology.
Applications of Aluminium Alloys
The applications of aluminium alloys are vast and nuanced, underscoring their pivotal role in various industries. Their unique blend of properties such as lightweight, corrosion resistance, and excellent electrical conductivity makes aluminium alloys indispensable in modern technology. Understanding their applications not only highlights their versatility but also illustrates the consequences of material choice in engineering and design. Each sector benefits in specific ways, providing diverse advantages while posing unique considerations in usage and performance.
Use in Aerospace Industry
Aluminium alloys are critical in the aerospace sector, where weight savings are paramount. Aircraft manufacturers favor these materials for fuselage components, wings, and other structural elements. For example, the alloys commonly used are 2024 and 7075, known for their high strength-to-weight ratios. Their resistance to fatigue and corrosion further enhances their suitability for aerospace applications.
The use of aluminium alloys in aerospace contributes to fuel efficiency and overall performance. By reducing weight without compromising strength, aircraft can traverse longer distances while consuming less fuel. However, it is important to consider fatigue life in designs to ensure the longevity of components under cyclic stresses.
"Aluminium alloys have transformed the aerospace industry by making aircraft lighter and more efficient. Their application is a testament to engineering advancements in material science."
Construction and Structural Applications
In the construction industry, aluminium alloys serve various purposes from architectural facades to structural components. Their lightweight nature simplifies handling and installation, making them an attractive choice for builders and architects. Additionally, aluminium’s corrosion resistance significantly contributes to long-term durability in buildings exposed to environmental elements.
Commonly employed alloys such as 6061 are notable for their good weldability and machinability. This flexibility allows for complex shapes and forms in construction. However, it is essential to account for local building codes and standards, as these may dictate specific alloy requirements based on environmental conditions and safety factors.
Automotive Industry Utilization
The automotive industry relies heavily on aluminium alloys to improve fuel efficiency and reduce greenhouse gas emissions. As manufacturers aim for lighter vehicles, the use of aluminium in body panels, engines, and structural components aligns with these goals. Alloys like 5754 and 6060 are typically used for automotive applications for their favorable properties.
Integrating aluminium alloys in vehicles also enhances performance. Their resistance to corrosion means lower maintenance costs and a longer lifespan for components. However, the challenge remains in the welding and joining processes, which require specialized techniques to maintain the integrity of the bond between parts.
Consumer Electronics and Appliances
Aluminium alloys find a significant place in the domain of consumer electronics. Commonly seen in the casings of laptops and smartphones, they provide not just aesthetic appeal but also contribute to heat dissipation and overall durability. Alloys such as 6063 are particularly popular due to their excellent surface finish and anodizing capability.
Moreover, aluminium’s lightweight nature facilitates portability in electronic devices. This trend extends to household appliances, where aluminium alloys are employed to manufacture components that require lightweight yet sturdy materials. The ongoing drive towards minimalistic design continues to support the use of these materials, highlighting their industrial relevance.
Future Trends in Aluminium Alloys
The landscape of aluminium alloys is evolving, spurred by rapid technological advancements and a growing focus on sustainability. Understanding future trends in aluminium alloys is not just beneficial; it is essential for industries that rely on these materials. As the demand for lightweight and high-strength materials increases, innovation in alloy development becomes crucial. This section will explore the developments in alloy science and the burgeoning trends in recycling, emphasizing their implications for the future of aluminium alloys.
Advancements in Alloy Development
Recent years have witnessed significant advancements in the development of aluminium alloys. Improved alloy compositions are leading to enhanced properties such as increased strength, improved corrosion resistance, and greater formability. For instance, new alloying techniques, including the use of advanced computational methods, are allowing engineers to predict and create alloys with tailored properties.
One notable development is the introduction of high-strength aluminium alloys, which are now being used in demanding applications such as aerospace and automotive industries. These high-performance alloys often incorporate elements like lithium and scandium to achieve superior mechanical characteristics. Additionally, innovations in additive manufacturing are also changing how aluminium alloys are processed.
Ultimately, these advancements foster the creation of lighter components without sacrificing structural integrity. This aligns with industry needs for more efficient and sustainable manufacturing processes.
Sustainability and Recycling Trends
In today’s world, sustainability is a priority. The aluminium industry is increasingly recognizing the importance of recycling as a vital component of its growth strategy. Recycling aluminium requires only about 5% of the energy needed to produce it from raw bauxite. This notable energy-saving is crucial in reducing the carbon footprint associated with aluminium production.
Several trends are emerging around sustainability within this sector:
- Circular Economy: There is a concerted push toward a circular economy where aluminium products are designed for reuse and recycling.
- Innovative Recycling Techniques: Method, such as the use of new sorting technologies and processes, are improving recovery rates of scrap aluminium.
- Life-Cycle Assessment: Manufacturers are increasingly conducting life-cycle assessments to understand the environmental impact of their products from production through to disposal.
"The shift towards sustainability in aluminium production is not merely a trend; it is a necessity for meeting global environmental standards."
These trends indicate critical changes in approach that can drive the aluminium industry towards more sustainable practices. The integration of these advancements poses both challenges and opportunities for stakeholders in various sectors, ensuring that aluminium alloys remain relevant in a rapidly changing manufacturing landscape.
Ending
The conclusion of this article serves as a vital component in encapsulating the discussed themes surrounding aluminium alloys. As we have explored, aluminium alloys play a significant role in modern technology and manufacturing due to their versatile properties and wide-ranging applications. Understanding the intricate details of their composition and classification allows professionals to make informed decisions about their use in various industries.
Aluminium alloys are valued for their lightweight nature, excellent strength-to-weight ratio, and resistance to corrosion. This makes them indispensable across sectors such as aerospace, automotive, and construction. As the demand for sustainable materials increases, the recycling processes for aluminium alloys also gain prominence. The importance of their development cannot be overstated, as advancements in alloy formulations continue to address the needs for greater efficiency and environmental compatibility.
Key considerations for employing aluminium alloys include their mechanical properties and the effectiveness of heat treatment methods. These factors can significantly influence performance and longevity in demanding applications.
"Aluminium alloys are not just materials; they are integral to innovation in many fields."
In summary, this article has aimed to provide a comprehensive understanding of aluminium alloys, highlighting their critical role in modern applications. The insights gathered here underscores their significance and the continuous evolution in their production and application processes.
Summary of Key Points
- Aluminium alloys consist of a primary element (aluminium) and other elements to enhance properties.
- They are classified into wrought and cast types, each with specific applications.
- These alloys exhibit excellent mechanical characteristics, including high strength and durability.
- The heat treatment processes significantly alter their performance, making it crucial to know the type required for specific uses.
- Applications span across numerous industries, including aerospace, construction, and consumer electronics, showcasing their versatility.
Final Thoughts on Aluminium Alloys
In concluding this exposition on aluminium alloys, it is clear that their significance transcends mere industrial applications. Their lightweight nature and versatility will continue to play pivotal roles in innovations aimed at enhancing efficiency and sustainability. Ongoing research and development in this area promise advancements that will likely further establish aluminium alloys as a cornerstone of modern engineering solutions. Understanding their properties and applications is essential for students, researchers, and professionals who aim to contribute to the fields of materials science and engineering.