In-Depth Insights into Refractory Removal Services
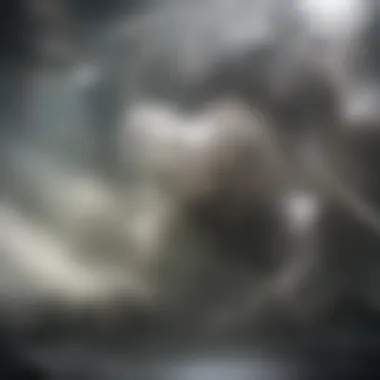

Intro
In the industrial sphere, the service of refractory removal holds significant value. Refractories are materials capable of withstanding high temperatures, and their use is widespread across industries such as steel, cement, and glass. Over time, these materials deteriorate and require removal to maintain operational efficiency. This article aims to provide an in-depth understanding of refractory removal services, elucidating the methodologies, techniques, and challenges involved in the process.
The focus will be on understanding how modern technology and practices are transforming refractory maintenance. Furthermore, the article emphasizes the importance of selecting competent service providers to guarantee not only efficiency in operations but also adherence to safety protocols. By evaluating the ins and outs of refractory removal, professionals and stakeholders will gain crucial insights into best practices and prevailing industry standards.
Prelims to Refractory Removal Services
In industrial settings, the management of refractory materials plays a crucial role in maintaining operational efficiency. This article presents a thorough exploration of refractory removal services. It aims to inform professionals about various techniques, safety measures, and the importance of these services in different industrial operations.
Definition and Scope
Refractory removal services refer to the processes and techniques used to eliminate or replace refractory materials from industrial equipment, such as furnaces, kilns, and reactors. The scope of these services is broad, ranging from mechanical removal methods to advanced chemical solutions that ensure thorough and efficient removal. These processes are essential in industries that rely on high-temperature operations, as refractory linings protect equipment from extreme conditions.
Importance in Industrial Operations
The significance of refractory removal cannot be overstated. First, it directly impacts the longevity and reliability of industrial equipment. Over time, refractory materials can degrade, leading to inefficiencies and increased energy consumption. Regular removal and maintenance can prevent costly equipment failures.
Additionally, efficient refractory removal contributes to operational safety. Improperly managed refractory systems may pose serious hazards, such as structural failures in furnaces that can result in accidents. Ensuring timely and professional removal mitigates these risks.
Moreover, the emphasis on environmental regulations increases the need for effective refractory removal practices. Industries must comply with strict safety and environmental standards, making it vital to engage proficient removal services. As such, understanding and implementing proper refractory management is crucial for sustained productivity and compliance in todayβs industrial landscape.
Types of Refractory Materials
Understanding the types of refractory materials is crucial for anyone involved in industrial processes. These materials play an essential role in high-temperature industries such as metallurgy, ceramics, and glass production. Knowing the distinct types helps professionals select the right refractory material for specific applications, leading to effective performance and safety in operations.
Common Refractory Types
There are several common types of refractory materials used across different industries. The primary categories include:
- Fireclay Refractory: This type is made from fireclay and is commonly used in furnace linings and kilns due to its thermal stability and moderate resistence to thermal shock.
- Silica Refractory: Composed primarily of silica, this material is utilized in environments where high temperatures are present. It's known for its excellent heat resistance.
- Alumina Refractory: This type contains high alumina content, resulting in superior strength and resistance to acidic environments. It is often used in steel and aluminum production.
- Magnesite Refractory: Derived from magnesium carbonate, this material is mainly used in steel processing. It has excellent resistance to basic slags and high-temperature performance.
- Carbon Refractory: These materials utilize carbon as a primary ingredient, which provides structural integrity under extreme conditions. It is typically found in aluminum and magnesium production.
Selecting the suitable type requires an understanding of the specific operational conditions, such as temperature and chemical exposure.
Material Properties and Applications
Each refractory type has unique material properties that influence its application. Professionals must consider thermal conductivity, thermal expansion, and chemical stability when selecting materials. Some key properties include:
- Thermal Stability: The ability to withstand high temperatures without melting or deforming.
- Thermal Shock Resistance: The capacity to resist cracking or fracturing from rapid temperature changes.
- Corrosion Resistance: Tolerance to chemical reactions that could degrade the material.
- Mechanical Strength: Strength under load, which is important for structural applications.
The applications of refractory materials include:
- Industries: Refractory materials are critical in sectors like steelmaking, cement, and ceramics, where high temperatures are standard.
- Equipment: They are used in furnaces, kilns, and reactors, ensuring safety and efficiency in high-temperature environments.
Choosing the right refractory material based on its properties ensures optimal performance and longevity. In summary, understanding the types and properties of refractory materials is essential in minimizing operational issues and enhancing safety in industrial environments.
Refractory Removal Techniques
Refractory removal techniques play a crucial role in ensuring operational efficiency in industries that rely on high-temperature processes. The selection of an appropriate method can significantly impact the effectiveness of the removal, safety of personnel, and longevity of equipment. These methods vary widely, and understanding their unique strengths and applications is essential for achieving optimal results.
Mechanical Removal Methods
Mechanical removal methods encompass a variety of physical techniques employed to detach refractory materials from surfaces. Tools and equipment such as chisels, scrapers, and hydraulic tools commonly facilitate this process. Depending on the type of refractory material, the choice of mechanical tool can differ. The primary advantage of mechanical removal is its direct approach to cutting through the refractory, which can be effective for thick or densely packed materials.
In practice, operators must consider the specific attributes of the refractory, such as hardness and thickness. Using the wrong mechanical technique can result in damage to the underlying structure or an incomplete removal process. Regular maintenance of tools is also crucial to prevent accidents.
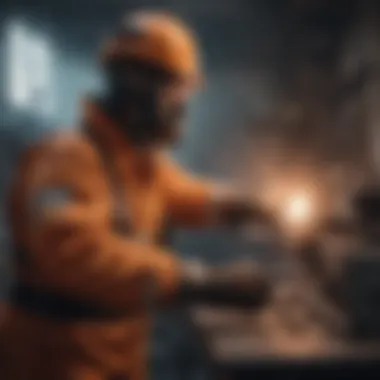
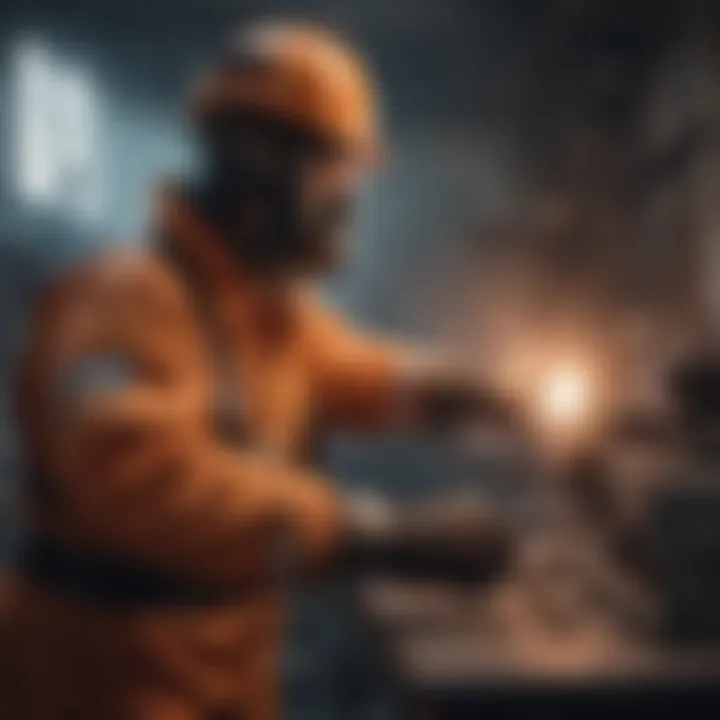
Thermal Removal Techniques
Thermal removal techniques use heat to effectively detach refractory materials from their substrates. Through methods such as flame-cutting or induction heating, heat expands the refractory, making it easier to remove once it cools. This technique is particularly advantageous in situations where the refractory material is extremely thick or strongly bonded.
The benefits of this method include a reduction in manual labor and increased efficiency in removing large sections. However, the operator must carefully control the temperature to avoid damaging surrounding structures or equipment. This highlights the need for skilled personnel who can manage these variables effectively.
Chemical Removal Processes
Chemical removal processes utilize specialized chemical agents to dissolve or disintegrate refractory materials. This technique is often less labor-intensive and can be completed with minimal manual effort. Chemical agents might be based on acids or other compounds that react specifically with the refractory material.
Choosing this method requires a deep understanding of the chemical properties involved. Incorrect application can lead to damage or unsafe working conditions. It's vital to conduct a thorough risk assessment and ensure proper safety measures are implemented to protect personnel and the environment.
In summary, the selection of refractory removal techniques is not merely a matter of convenience or efficiency. It demands a thorough understanding of the materials, tools, and the operational environment to ensure safety and efficacy in the removal process.
Challenges in Refractory Removal
The process of refractory removal presents several challenges that can impact industrial operations. Understanding these challenges is crucial for decision-makers as they influence not only operational efficiency but also safety, costs, and environmental compliance. Addressing these matters effectively ensures that companies can maintain productivity while adhering to safety protocols and regulatory standards.
Health and Safety Concerns
One of the paramount challenges in refractory removal is health and safety. The removal process often involves exposure to hazardous materials and environments. Workers can be at risk of inhaling dust, which may contain harmful particles. Protective gear, such as respirators and suits, is essential, but it may not always offer complete protection.
Furthermore, the physical demands of the job pose risks, including injuries from lifting heavy materials or the use of machinery. Ensuring that safety protocols are strictly followed is necessary. Training staff to recognize and mitigate risks is vital. Strong attention to safety can make the difference between a successful operation and a preventable incident.
Operational Downtime
Operational downtime is another significant concern during refractory removal. The need for equipment and facility shutdowns can lead to considerable loss in productivity. Industries that rely on continuous operations can find downtime particularly costly.
To minimize interruptions, planning and scheduling are critical. Effective project management includes assessing the extent of removal work needed before a shutdown occurs. Running simulations and creating detailed timelines can help in reducing unexpected delays. Ultimately, finding the balance between thorough refractory removal and operational availability is necessary for business continuity.
Environmental Considerations
Environmental considerations play a key role in the refractory removal process. Many industries face increasing pressure to comply with environmental regulations. The handling and disposal of removed materials must adhere to local and international standards. Improper disposal can lead to contamination of soil and water sources.
Additionally, emissions released during removal processes must be monitored. Companies should adopt best practices for waste management and consider alternatives that lessen their environmental footprint. Engaging with environmental specialists can aid in finding sustainable solutions for the disposal and recycling of refractory materials.
"Addressing health, operational, and environmental challenges in refractory removal is not just about compliance; it is about ensuring long-term sustainability for industrial operations."
In summary, navigating the challenges in refractory removal requires a comprehensive approach. Emphasizing health and safety, minimizing operational downtime, and addressing environmental impacts are crucial steps. By doing so, companies can enhance efficiency and maintain their commitment to operational excellence.
Equipment and Tools for Refractory Removal
The role of equipment and tools in refractory removal cannot be overstated. These tools are the backbone of effective and efficient removal processes. Using the right equipment minimizes downtime, enhances safety, and ensures that the job meets industry standards. Proper tools also mitigate potential risks associated with the removal process by improving precision and reducing the physical strain on workers.
In this section, the focus will be on the types of equipment necessary for successful refractory removal and the notable innovations that are raising the bar for these services.
Overview of Required Equipment
When it comes to refractory removal, a variety of equipment is necessary to handle different tasks. The requirements can vary significantly depending on the type of refractory material and the specific method of removal being used. Here are some essential equipment types:
- Hydraulic Breakers: These are used to easily break apart hardened refractories. Their efficiency and power make them a common choice in many industrial settings.
- High-Pressure Water Jetting Systems: This method uses high-pressure water streams to remove refractory material. It is effective and reduces the risk of damaging underlying structures.
- Diamond Wire Saws: These are used for cutting through dense refractory materials. They provide clean cuts with minimal waste.
- Thermal Lancing Equipment: This involves using high-temperature rods to melt through refractory materials. It is particularly useful for thick refractories that are difficult to remove by other means.
- Chemical Removal Agents: Certain chemical solutions can assist in breaking down specific types of refractory matrices.
Each tool has its distinct advantages and limitations, making it crucial for service providers to evaluate needs based on specific project requirements.
Technological Innovations
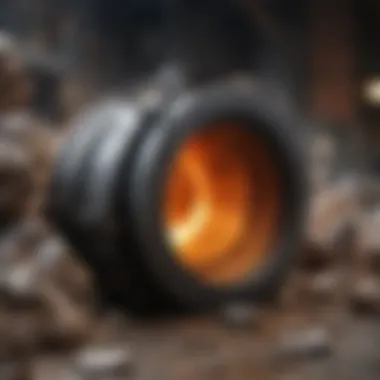
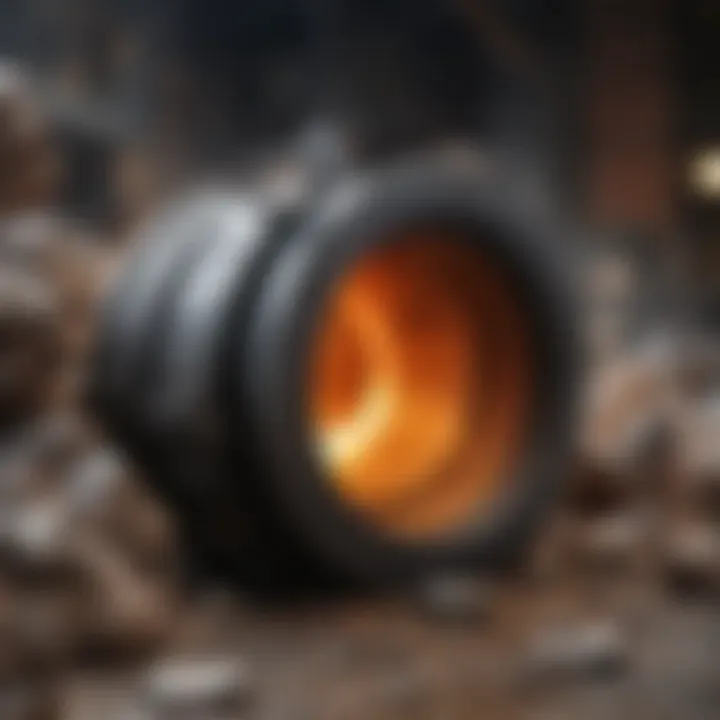
The refractory removal industry is witnessing a wave of technological advancements. These innovations are aimed at enhancing efficiency, safety, and effectiveness. Some noteworthy technologies include:
- Robotic Systems: Robots can perform dangerous tasks with precision and minimal supervision. They can work in hazardous conditions, reducing human exposure to risks.
- CNC Cutting Machines: These are programmed for accuracy and can handle complex removal projects. They ensure uniformity and quality in the removal process.
- Integrated Software Solutions: Software applications that assist in planning and monitoring removal tasks allow for better project management and resource allocation.
- Advanced Safety Gear: Modern personal protective equipment is designed to provide better comfort and safety for workers who are exposed to hazardous materials during removal tasks.
"Investing in the best tools not only enhances performance but also demonstrates a commitment to worker safety and operational excellence."
For additional information on technological trends, consider visiting Wikipedia, Britannica, or engage in discussions on platforms like Reddit.
Understanding the equipment and innovative technologies is essential for any stakeholder involved in the refractory removal industry.
Selecting a Refractory Removal Service Provider
Selecting the right refractory removal service provider is a critical element in ensuring smooth industrial operations. The choice of service can significantly affect not only the efficiency and effectiveness of the removal process but also the overall safety and downtime of the facility. With many options available in the market, it is essential to weigh various factors before making a commitment. This section will outline key criteria for evaluation, assess the reputation and experience, and discuss cost considerations that should guide your selection process.
Criteria for Evaluation
When evaluating refractory removal service providers, it is important to establish a comprehensive set of criteria to guide your decision. Here are some key points to consider:
- Experience and Expertise: Providers should have considerable industry experience and expertise in handling diverse types of refractories. Look for companies that have a proven track record in similar projects.
- Safety Record: Safety is paramount in refractory removal. Investigate the safety protocols adhered to by the provider and check their incident history.
- Technical Capabilities: The technology and methods employed by the service provider should be cutting-edge. This may include advanced mechanical, thermal, or chemical techniques that align with industry standards.
- Compliance: Ensure that the provider adheres to relevant industry regulations and compliance measures. This guarantees that all removal processes are conducted legally and safely.
Reputation and Experience
Reputation and experience should weigh heavily in your decision-making process. A well-regarded provider often comes with substantial references from previous clients. You can evaluate their reputation through:
- Client Testimonials: Reading reviews can give insights into the quality of service provided. Beware of companies with very few reviews or overwhelmingly negative feedback.
- Case Studies: Look for documented case studies that highlight successful removal projects. This showcases the provider's ability to handle complex tasks and challenges.
- Industry Standing: Choose providers that are known and respected within the industry. Membership in professional organizations can further indicate commitment to quality and ongoing training in best practices.
Cost Considerations
Understanding the cost structure of refractory removal services can be challenging, yet it is a necessity for budgeting and financial planning. Some aspects related to cost to keep in mind include:
- Transparency: Ensure that the provider offers transparent pricing models. Be wary of hidden fees that could inflate the overall cost down the line.
- Value vs. Price: Consider the value of the service in relation to its price. Cheaper options may save money initially but can incur additional costs through inefficient removal processes or safety incidents.
- Quotes and Comparisons: Obtaining multiple quotes from different providers allows for comparison, helping to identify a competitive rate while maintaining quality services.
Overall, taking the time to select the right refractory removal service provider contributes to the long-term success of industrial operations. Making informed decisions will mitigate risks, optimize costs, and enhance the overall effectiveness of refractory management.
Regulatory Standards and Compliance
In the realm of refractory removal services, adherence to regulatory standards and compliance measures is crucial for ensuring safety and efficiency. These regulations are designed to protect workers, the environment, and the integrity of industrial operations. Ignoring these standards can result in serious setbacks, including legal issues, increased costs, and risks to personnel safety.
Industry Regulations
Different industries face specific regulations regarding the removal of refractory materials. Regulatory bodies like the Occupational Safety and Health Administration (OSHA) and the Environmental Protection Agency (EPA) impose guidelines that must be followed. These regulations cover areas such as:
- Personal Protective Equipment (PPE): Requirements often detail the necessary safety gear for workers involved in refractory removal, including gloves, helmets, and specialized masks.
- Hazardous Waste Disposal: Protocols are in place to ensure that waste materials are disposed of correctly to mitigate environmental impacts.
- Air Quality Standards: Limits on emissions during the removal process help maintain air quality and reduce pollutants in the atmosphere.
Compliance with these regulations is not only a legal requirement but also enhances operational excellence. It helps build a culture of safety and responsibility within an organization, ultimately leading to better productivity and reduced risk.
Compliance Measures
To ensure adherence to industry regulations, companies can implement several compliance measures. These measures include:
- Regular Training: Staff should receive ongoing training on safety protocols and revised regulations to ensure everyone understands the latest requirements.
- Inspection and Audits: Routine audits of processes and equipment can help organizations identify potential compliance issues before they become serious problems.
- Documentation: Keeping thorough records of safety inspections, training sessions, and materials used for removal is essential for demonstrating compliance during audits.
"Maintaining compliance is a proactive strategy that shields companies from potential liabilities while safeguarding the workforce's well-being."
- Consulting Experts: Partnering with professionals who specialize in regulatory compliance can significantly ease the burden of navigating complex regulations.
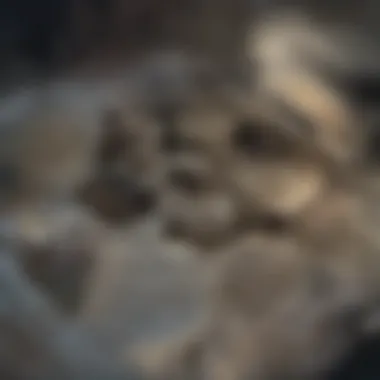
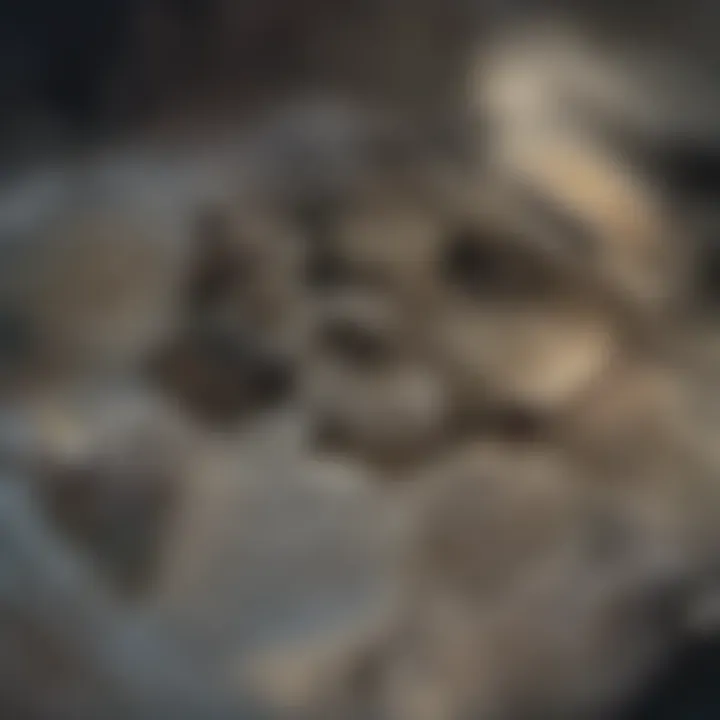
By prioritizing these compliance measures, businesses can effectively manage risks associated with refractory removal, ensuring both operational continuity and the protection of workers and the environment.
Case Studies
Case studies play a vital role in understanding the efficacy of refractory removal services. These concrete examples provide valuable insights not only into successful methodologies but also into the potential pitfalls organizations may face. They serve as real-world representations of how strategies are applied and measured. Evaluating case studies allows industry stakeholders to grasp the nuances of different approaches, leading to more informed decisions in their operations. They illustrate the practical implications of technologies, techniques, and service providers in various scenarios.
Successful Removal Projects
Successful removal projects display the effectiveness of well-planned logistics and skilled execution. For instance, a recent case study involving a large steel manufacturer showcased how employing advanced thermal removal techniques led to a significant reduction in downtime.
The project involved removing outdated refractory linings from critical furnace sections. The team strategically scheduled the removal during maintenance windows to minimize operational disruption.
The results were remarkable:
- Downtime decreased by 30% compared to previous projects.
- The costs were brought down due to better project management and use of innovative equipment.
- Safety incidents were reduced by implementing stringent protocols.
Such examples provide a roadmap for best practices. They highlight the importance of preparation, skilled personnel, and appropriate choices of removal techniques. Documenting these successes helps gather a compendium of reliable approaches that can be referenced for future projects.
Lessons Learned from Failures
Not all projects achieve their goals. Lessons learned from failures can reveal vital considerations that are often overlooked. For example, one industrial client experienced significant complications during a refractory replacement project when inadequate planning led to unforeseen delays and costs.
The primary reasons for this failure included:
- Insufficient Assessment of Existing Conditions: The team did not fully evaluate the condition of the existing materials, leading to unexpected complications during removal.
- Poor Communication Among Teams: Lack of clarity resulted in misaligned objectives among contractors and operations staff.
- Ineffective Resource Allocation: Not enough manpower and specialized equipment were allocated, which contributed to prolonged downtime and increased expenses.
These failures provided critical lessons that can inform future projects. They stress the necessity of comprehensive evaluations before commencing work, clear lines of communication among all parties, and resource planning tailored to project requirements. Each failure serves as a reminder that preparedness is key to avoiding similar setbacks in future endeavors.
Understanding both successful and failed projects enriches the knowledge base within the industry. Sharing these experiences can lead to enhanced strategies and overall improvements.
Future Trends in Refractory Removal Services
The discussion around refractory removal services is increasingly gaining attention due to ongoing advancements in technology and the demand for more efficient industrial operations. Understanding the future trends in this sector can provide valuable insights for organizations aiming to enhance their refractory management processes. As industries evolve, so do the tools and techniques for refractory removal. Key trends include the emergence of innovative materials, advancements in automation, and the integration of data analytics to improve decision-making.
Emerging Technologies
Several emerging technologies are transforming refractory removal services. These innovations focus on improving efficiency while ensuring safety and compliance with industry standards.
- Robotics: The use of robotics in refractory removal is on the rise. Automated systems can perform hazardous tasks, reducing the risk to human workers. Robots can operate in high-temperature environments, effectively and efficiently removing refractory materials without exposing personnel to potential hazards.
- Laser Technology: Lasers are being increasingly utilized. Their precision allows for more accurate removal processes. This method minimizes the risk of damaging underlying structures, while also speeding up the removal time.
- Smart Tools: Tools equipped with IoT (Internet of Things) technology are making their way into refractory removal services. These smart tools can provide real-time data on temperature, structure integrity, and other key metrics, allowing for better planning and execution of removal tasks.
- Eco-Friendly Solutions: With rising environmental awareness, there is a growing emphasis on eco-friendly removal processes. The focus is on developing chemical agents that can effectively break down refractory materials without harming the environment.
"Embracing new technologies not only optimizes the refractory removal process but also aligns with sustainability goals that many companies are now prioritizing."
Market Outlook
Looking ahead, the market for refractory removal services is expected to grow substantially due to increasing industrial activity worldwide. Industries such as metallurgy, petrochemicals, and energy generation contribute significantly to this demand. Factors influencing the market outlook include:
- Rising Demand: As global manufacturing expands, the need for effective refractory maintenance will increase. Companies will seek proficient service providers who can ensure minimal downtime and compliance with safety regulations.
- Sustainability Initiatives: More companies are prioritizing sustainability. There will likely be an uptick in demand for services that offer environmentally friendly methods of refractory removal.
- Investment in Technology: Organizations are likely to invest more in the latest technologies that facilitate efficient removal processes. Technologies such as machine learning and advanced analytics could lead to improved operational strategies.
- Regulatory Compliance: With stringent regulations in place for industrial operations, companies will require skilled service providers who are well-versed in compliance measures regarding refractory materials.
Finale
The conclusion serves as a critical endpoint within this article, encapsulating the essence of refractory removal services. It provides a reflection on the necessity of understanding the full breadth and detail of this topic, particularly for professionals involved in industrial operations that utilize refractory materials.
Summary of Key Points
Understanding regulations is equally vital. Adhering to industry standards protects workers and promotes responsible practices. Additionally, selecting the right service provider plays a pivotal role in achieving efficient outcomes with minimal disruptions.
Final Thoughts
Engaging with the right information and resources empowers professionals to navigate the complexities of refractory removal, ensuring safety, compliance, and operational effectiveness.
Ultimately, investing in expert services not only guarantees optimal results but also fosters a culture of safety and excellence in industrial operations.