Integrating Metal and Plastic in 3D Printing Techniques

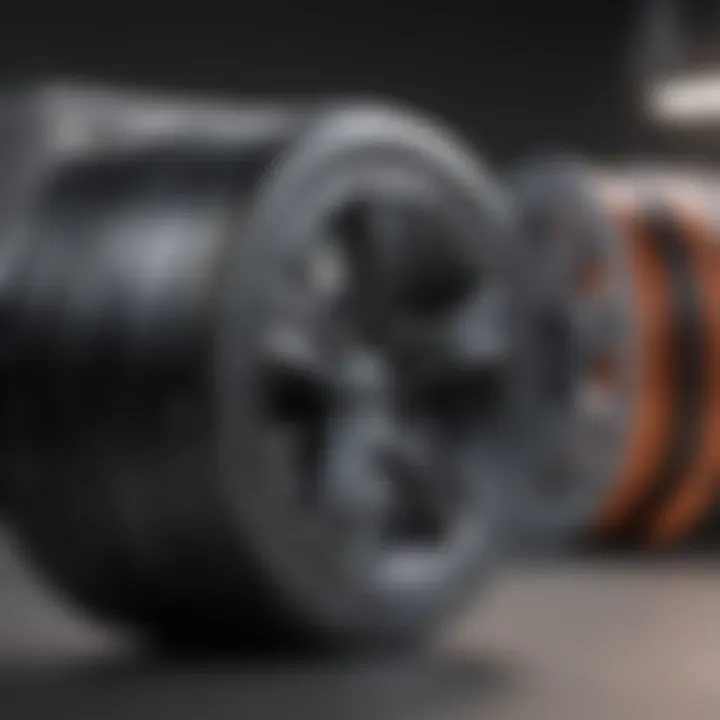
Intro
In recent years, the field of 3D printing has experienced remarkable growth, transforming how objects are designed and manufactured. One of the most sophisticated advancements within this arena involves the integration of metal and plastic. This practice paves the way for hybrid materials that can deliver enhanced performance for a myriad of applications, from engineering to artistic designs.
Understanding the complexities behind this integration requires a closer look at the methodologies employed in these processes. In what follows, we will delve into the various techniques used, the technology that makes it possible, and the implications these innovations carry for the future of manufacturing and material science.
Methodologies
Description of Research Techniques
The integration of metal and plastic in 3D printing sprouts from various innovative approaches. Most commonly, techniques involve either direct hybridization during the printing process or post-processing methods. One notable method is metal casting into plastic. Here, a plastic part printed by a fused deposition modeling process can be utilized as a mold for metal casting, allowing for metal features to be precisely embedded.
Another intriguing technique entails multi-material extrusion, where specialized nozzles are used to simultaneously deposit metal filaments alongside plastic. This enables a more seamless integration of materials, yielding composites with unique mechanical properties while maintaining lighter weights. While these methods are groundbreaking, they present their own challenges needing various additional equipment for precision and quality.
Tools and Technologies Used
To facilitate such innovative methodologies, a plethora of advanced tools and technologies are needed. Robotic arms equipped with an array of extruder heads can apply different materials in real-time, allowing for intricate designs that stand the test of both heat and mechanical stress. Furthermore, specialized 3D printers designed for hybrid fabrication, like the Markforged Metal X, can fuse metals and polymers with a high degree of effectiveness. Additionally, finishing tools that provide surface treatment are utilized to improve adhesion and finish quality, demonstrating the intricate balance between different materials in design and fabrication.
"The amalgamation of metal and plastic not only enhances durability but also introduces novel functionalities that pure materials fail to deliver."
Discussion
Comparison with Previous Research
Previous research mostly focused on either metal or plastic in isolation. While various studies documented the advantages of each material individually, the potential for their combined properties was often understated. Today, the discourse surrounding hybrid materials illustrates a significant shift in perspective. This integration paves the way for new avenues, promoting versatility in design while empowering industries to produce components that previously seemed unattainable.
Theoretical Implications
The theoretical implications of integrating metal and plastic extend beyond mere material science. They touch on the principles of engineering design, such as optimization and material efficiency. It pushes for a re-evaluation of how we think about structural integrity and performance. In a world increasingly leaning toward sustainability, the hybrid approach offers a promising alternative, enabling reduced material waste and innovative recycling methods.
In summary, the ongoing exploration into the integration of metal and plastic within the realm of 3D printing unfolds new chapters not only in manufacturing but also in scientific inquiry, captivating the curiosity of researchers and practitioners alike.
Overview of 3D Printing Technology
3D printing has transformed how we think about manufacturing and design. This overarching theme provides a critical backdrop to discussing the integration of metal and plastic. In today's fast-paced world, 3D printing offers versatility like no other method, efficiently producing complex geometries that were once difficult to achieve using traditional techniques.
Definition and Process of 3D Printing
3D printing refers to the additive manufacturing process whereby materials are joined together, layer by layer, to create a three-dimensional object. Unlike subtractive manufacturing, which involves cutting away material from a solid block, 3D printing starts from nothing, gradually constructing the desired shape. This saves material and can lead to less waste—an important consideration in today’s environmentally conscious landscape.
To understand the intricacies of this technology, it’s essential to consider the materials used, the machinery involved, and the range of applications it supports. The process generally begins with a digital model created through computer-aided design (CAD) software. This model is then sliced into thin horizontal layers by slicing software, allowing the printer to replicate each layer until the final product is formed.
Types of 3D Printing Techniques
Several techniques dominate the field of 3D printing, each offering distinct characteristics suitable for different tasks:
Fused Deposition Modeling (FDM)
One of the most prevalent techniques is Fused Deposition Modeling, notable for its accessibility and simplicity. In this process, thermoplastic filament is heated until it melts and is then extruded through a nozzle. The primary characteristic of FDM is its ability to print various plastics, including ABS and PLA, making it an attractive option for hobbyists and small-scale production. The critical advantage here lies in the cost-effectiveness and availability of materials. However, the adhesion between layers can sometimes become a challenge, affecting the strength of the final product.
Stereolithography (SLA)
Stereolithography is another method that brings a different approach to the table. Utilizing a UV light source, SLA cures liquid resin step-by-step, allowing for exceptionally fine detail and surface finish. The key feature of SLA is its precision; it's widely regarded as one of the most accurate forms of 3D printing. This accuracy makes it a preferred choice for industries requiring close tolerances, such as dentistry or jewelry design. However, the materials—primarily photopolymer resins—can be more brittle than those used in FDM, limiting durability in some applications.
Selective Laser Sintering (SLS)
Selective Laser Sintering takes a more industrial turn by employing a laser to fuse powdered materials such as nylon or metal into a solid structure. One standout characteristic of SLS is its ability to produce strong, functional parts without the need for support structures. This technique is particularly beneficial for producing complex designs that might be impossible through other methods. Still, SLS machines tend to be quite expensive, thus limiting access for individuals or smaller businesses.
Direct Metal Laser Sintering (DMLS)
Direct Metal Laser Sintering is crucial for those seeking the power of metal printing. By using a focused laser to melt layers of metallic powder, DMLS creates highly durable components. The defining aspect of DMLS is its ability to produce parts that exhibit superior mechanical properties, making it invaluable in aerospace, automotive, and medical sectors. Unfortunately, the cost of machinery and required materials can be prohibitive, which may deter smaller operations from employing this technique.
"Understanding different 3D printing techniques is essential for leveraging the unique strengths of metal-plastic integration for innovative applications."
In summary, the landscape of 3D printing is varied. Each technique offers unique benefits while also presenting specific challenges, particularly when merging diverse materials such as metal and plastic. This introduction lays the groundwork for understanding the various methodologies that make this integration possible.
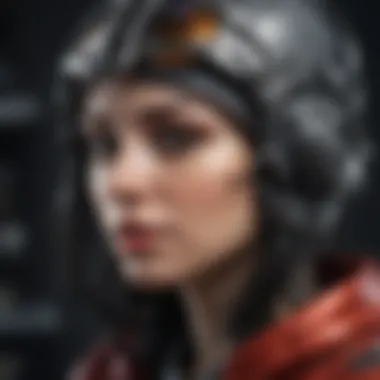
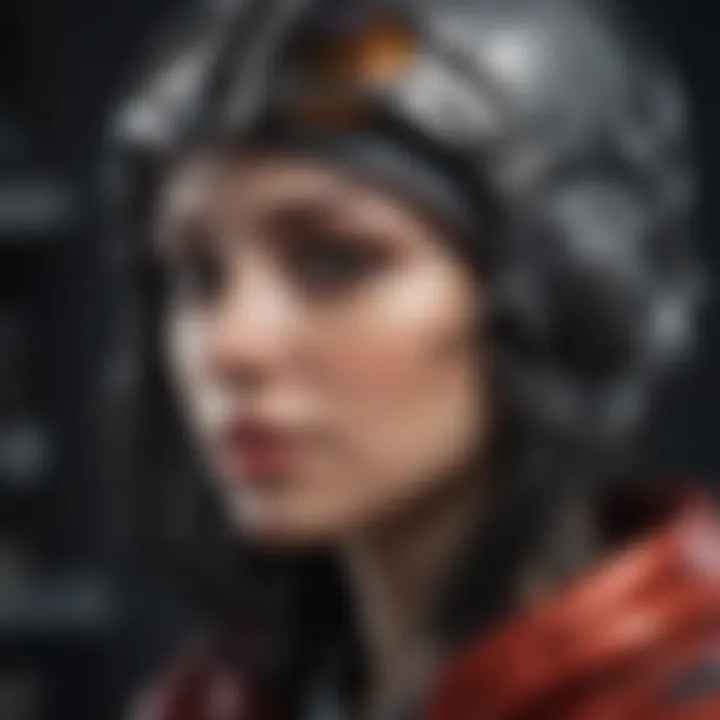
Materials Used in 3D Printing
When we talk about 3D printing, we can't overlook the critical role materials play in this transformative technology. Materials Used in 3D Printing form the backbone of the entire process, influencing the final product's structural integrity, aesthetic attributes, and functional capabilities. Understanding the intricacies of the materials, especially metals and plastics, is crucial as we dive deeper into how they can be effectively merged for innovative applications. By selecting the appropriate materials, manufacturers can create parts that meet stringent performance and design requirements.
Plastics in 3D Printing
Plastics have long been the star of the 3D printing stage due to their versatility and ease of use. Their wide range of properties makes them suitable for various applications, from prototypes to end-use components. They indeed have a strong foothold in the additive manufacturing world.
Types of 3D Printing Plastics
When discussing Types of 3D Printing Plastics, it’s essential to highlight categories like PLA (Polylactic Acid), ABS (Acrylonitrile Butadiene Styrene), and PETG (Polyethylene Terephthalate Glycol). Each offers unique characteristics. For instance, PLA is biodegradable and easy to print, making it a popular choice among hobbyists.
- Key Characteristics: High strength-to-weight ratio, dimensional stability, and ease of processing.
- Unique Features: PLA is plant-based, whereas ABS is known for its toughness but can warp if not printed in a controlled environment.
The main contributions of these plastics to this article lie in their accessibility and their role in producing lightweight components that can be combined with metals for enhanced functionality.
Properties and Applications
In terms of Properties and Applications, plastics commonly used in 3D printing are noted for their engineering properties. For example, PETG offers good impact resistance and chemical stability.
- Key Characteristic: Excellent layer adhesion and flexibility lend PETG an edge in applications requiring durability.
- Advantages/Disadvantages: While plastics enable intricate designs, they may lack the same thermal resistance as metals, limiting their use in high-temperature environments.
The discussion around properties helps to underline their importance when integrating with metals, as it showcases potential synergies and limitations that must be accounted for when forging metal-plastic hybrids.
Metals in 3D Printing
While plastics often take the limelight, the integration of metals into 3D printing certainly shouldn’t be brushed aside. Metals bring a whole new level of strength and durability, making them indispensable particularly in industries where performance is paramount.
Common Metals Used
Metals like stainless steel, titanium, and aluminum are indispensable in Common Metals Used in 3D printing.
- Key Characteristics: Titanium is known for its exceptional strength-to-weight ratio, while aluminum finds favor in lightweight applications due to its excellent malleability.
- Unique Feature: The choice of metals directly affects the mechanical properties of the printed items, leading to better performance in demanding applications.
These metals contribute significantly to the potential for hybrid printing by adding strength and thermal properties, which can complement the often lighter but more flexible plastics.
Mechanical Properties and Suitability
The Mechanical Properties and Suitability of metals in 3D printing are unequaled by plastics. Metals often exhibit superior fatigue resistance and stress tolerance, which is crucial for components subjected to dynamic forces.
- Key Characteristics: High tensile strength, excellent toughness, and superior corrosion resistance are vital for parts intended for harsh environments.
- Advantages/Disadvantages: While metals enhance durability and can withstand extreme conditions, they may also complicate the printing process, as they often require higher temperature settings and specialized machinery.
In summation, understanding the materials used in 3D printing, especially metals and plastics, is pivotal for optimizing the hybrid printing process. By leveraging the strengths of both materials, manufacturers can create components that are both functional and innovative, paving the way for advancements across various industries.
Merging Metal and Plastic in 3D Printing
The integration of metal and plastic in 3D printing represents a significant leap in manufacturing capabilities. By merging these two materials, one can exploit the unique advantages each brings to the table. Metal provides strength, durability, and thermal resistance, while plastic offers versatility and lightweight properties. The synergy between the two creates composite materials that can perform exceptionally well in various applications.
Understanding the nuances of this hybridization not only helps in advancing technology but also opens new avenues in industries such as aerospace and automotive, where both material performance and weight efficiency are critical. Moreover, exploring such combinations can lead to innovative designs that were previously unattainable with traditional manufacturing methods.
The Concept of Hybrid Printing
Hybrid printing is a revolutionary concept that intertwines the capabilities of different materials to achieve enhanced properties. This method focuses on strategically utilizing the strengths of both metal and plastic. As a result, hybrid parts can withstand more stress, function better under temperature fluctuations, and ultimately have a longer lifespan.
Additionally, the hybridization process paves the way for customization. Designers have the freedom to dictate where metal and plastic should be used within a part, which can significantly improve its overall performance. This level of control fosters creativity and ensures that each piece can be tailor-made for its specific application.
Methods for Combining Materials
The incorporation of metal and plastic can be achieved through various methodologies. Notably, two prominent techniques stand out: sequential layering and co-printing approaches. Each method has its unique benefits and drawbacks, tailoring its suitability to different applications.
Sequential Layering Techniques
Sequential layering is a fascinating approach where layers of metal and plastic are printed one after the other. This stacking method is one of its major characteristics. It allows for a distinct separation, enabling precise control over the material distribution, thereby optimizing performance.
One significant advantage of this technique is that it can utilize existing printer technology with minimal modifications, making it a popular choice. The modular nature of this method suits rapid prototyping and allows researchers to evaluate different configurations effectively.
However, challenges exist, particularly regarding layer adhesion. Achieving a robust bond between the layers can be tricky, and if not handled properly, it may lead to weaknesses in the final product.
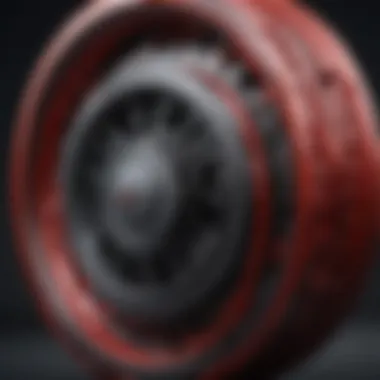
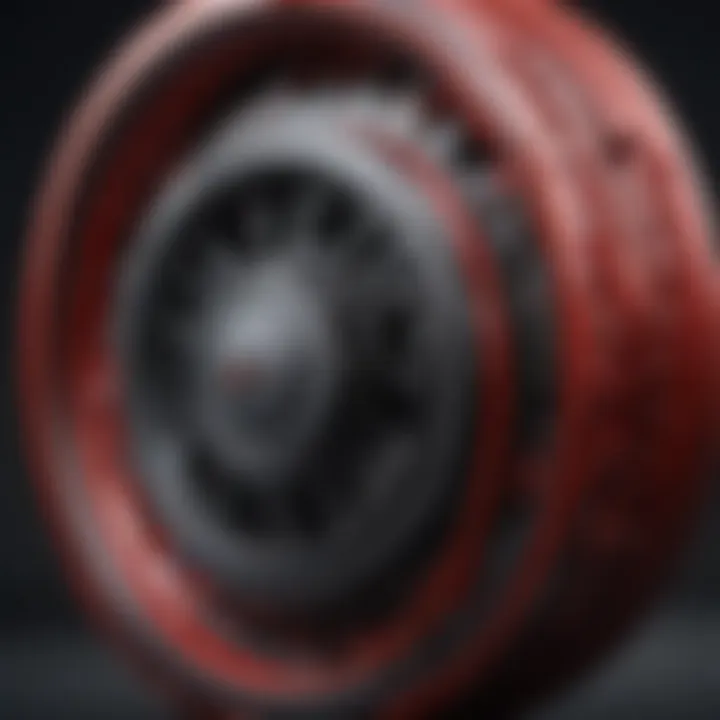
Co-Printing Approaches
Co-printing approaches simplify the integration of materials by simultaneously depositing both metal and plastic within the same print job. This real-time combination is a standout feature that enables the creation of parts with very complex geometries and tailored properties.
This method is advantageous as it can save considerable time in the production process and can lead to superior material properties compared to sequential techniques. Additionally, the simultaneous layering often results in excellent adhesion between the two materials, enhancing durability.
Nonetheless, mastering this process can be a bit of a challenge. The different thermal properties of metals and plastics might lead to complications, like warping or uneven distribution of materials. Staying on top of these issues requires a keen understanding of thermal dynamics.
"Combining materials in 3D printing opens a treasure chest of possibilities, allowing designers to push the boundaries of innovation."
In summary, the merging of metal and plastic through hybrid printing not only presents exciting opportunities for advancement in manufacturing but also demands consideration of various technical elements. Each method comes with its own set of challenges and benefits, shaping how industries will approach the future of 3D printing.
Advantages of Metal-Plastic Composite Printing
The integration of metal and plastic in 3D printing isn't just a trend; it's a game-changer that revolutionizes various fields, from aerospace to medical devices. The advantages of metal-plastic composite printing are vast and significant, meriting a closer look. This hybrid approach offers opportunities that standalone materials can't match, paving the way for innovative solutions to complex problems.
One of the most compelling aspects of this technology is its potential to enhance the usable attributes of printed parts. By combining the best characteristics of both metals and plastics, designers can create components that outperform traditional materials individually. Let’s peel back the layers on a couple of pivotal benefits: enhanced mechanical properties and weight reduction alongside cost efficiency.
Enhanced Mechanical Properties
When it comes to mechanical properties, the combination of metal and plastic yields remarkable results. Metals provide strength and durability, while plastics contribute flexibility and resistance to corrosion. This unique amalgamation can lead to materials with improved tensile strength, impact resistance, and overall longevity.
- Tensile Strength: Metal-plastic composites can withstand greater forces without deforming, an essential trait in high-stress environments. For instance, parts used in automotive applications that need to endure vibrations and load changes benefit from this increased strength.
- Impact Resistance: The toughness of plastics can absorb shock better than metals alone, making the composite a suitable candidate for parts exposed to sudden forces. One might find this quality particularly useful in protective casings for electronic devices.
- Corrosion Resistance: Plastics are inherently resistant to many chemicals. By integrating them with metals, components become less susceptible to corrosive environments, extending their usability in harsh conditions.
These enhanced mechanical properties serve industries where failure isn't an option. Take the aerospace sector, where a slight failure can lead to catastrophic results; robust, reliable components are a must.
Weight Reduction and Cost Efficiency
Switching gears, let’s talk about weight reduction and cost efficiency. As industries strive to reduce weight to improve fuel efficiency and performance, metal-plastic composites can play a significant role.
- Lightweight Solutions: Traditional metal parts can be heavy, adversely affecting performance in applications like aerospace and automotive. By integrating lightweight plastics, designers can significantly reduce weight without sacrificing the strength required for safety and functionality.
- Cost Reduction: Producing hybrid parts can also lead to substantial cost savings. With the ability to combine materials, manufacturers can minimize waste and enhance production speed. In fields where scaling production is essential, such as in producing automotive components or medical devices, these savings can ripple through the supply chain, making the end products cheaper without compromising quality.
By adopting metal-plastic composite printing, companies not only innovate but also enhance efficiencies across the board. This is not merely about combining materials; it's about rethinking whole systems of production.
Ultimately, these advantages paint a promising picture for the future of 3D printing as it continues to evolve.
Challenges in Hybrid 3D Printing
The integration of metal and plastic in 3D printing presents a unique set of challenges that need to be navigated carefully. These challenges are not just technical hurdles; they are critical considerations in determining the effectiveness and applicability of hybrid printing to various industries. Understanding these challenges is paramount for both current practitioners and those who are aiming to innovate in this space. The successful adhesion of metal and plastic is crucial, along with ensuring that the two materials maintain compatibility throughout the manufacturing process. Addressing these challenges is not only important for maximizing the performance of hybrid parts but also for realizing the full potential of this advanced technology.
Adhesion Challenges
Adhesion is one of the foremost challenges that arises in hybrid 3D printing. The interaction between metal and plastic can be complex, often resulting in weak bonds that may not withstand operational stresses. When layers of dissimilar materials are printed, you often face issues, such as delamination, where layers peel apart due to inadequate adhesion at their interface.
Key factors influencing adhesion include:
- Surface Preparation: Proper cleaning and possibly roughening the surfaces before printing help increase the contact area and promote better bonding.
- Material Properties: Different plastics and metals have unique properties that affect how well they stick together. For example, how the plastic expands or contracts during cooling can affect adhesion.
- Printing Parameters: Temperature settings, printing speeds, and the type of extruder can all play a role in determining adhesion strength.
In many cases, applying adhesion promoters or using advanced nanocoatings has shown promise. However, these methods often add complexity to the process and may not provide a foolproof solution for all material combinations. Thus, exploration into effective coupling agents and methods remains necessary to improve adhesion performance across diverse applications.
Thermal and Mechanical Compatibility
Beyond adhesion, thermal and mechanical compatibility must also be carefully considered. Each material behaves differently under changes in temperature, and when subjected to stress or load, they may react in ways that compromise the integrity of the final product.
This can manifest in several ways:
- Thermal Expansion Mismatch: Metals usually have lower thermal expansion coefficients compared to plastics. When a hybrid component is subjected to heating or cooling, it may lead to stress concentrations, causing warping or failure.
- Differing Mechanical Properties: The strength, elasticity, and overall durability of metal and plastic vary significantly. When subjected to mechanical loads, this can result in uneven stress distribution. For instance, if the metal acts as a stiff core, the surrounding plastic may yield or fracture under load, which diminishes the effectiveness of the hybrid component.
Ensuring compatibility requires a deep understanding of both material properties and the conditions they will face in practical applications. Research into advanced materials, like composites or specially formulated plastics that mimic the mechanical properties of metals, could pave the way forward in addressing compatibility issues.
"The ability to harmonize the properties of metal and plastic in hybrid printing will define the next wave of engineering innovation."
Current Applications of Metal-Plastic Hybrid Printing
The integration of metal and plastic in 3D printing holds considerable promise in diverse industries, leveraging the unique properties of both materials to create innovative solutions. The ability to produce lightweight yet sturdy components, as well as complex geometries that could not be made through traditional manufacturing, represents significant advances in engineering and design. With the rising demand for custom, durable, and efficient components, understanding the current applications of metal-plastic hybrid printing is vital. This enhances our grasp of the market trends, technological advancements, and future possibilities.
Aerospace Industry
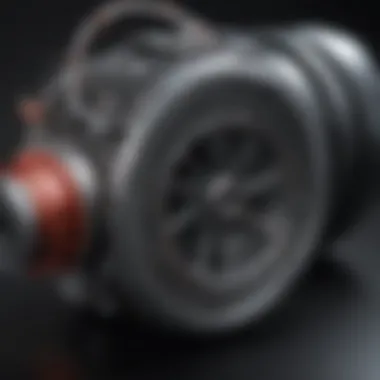
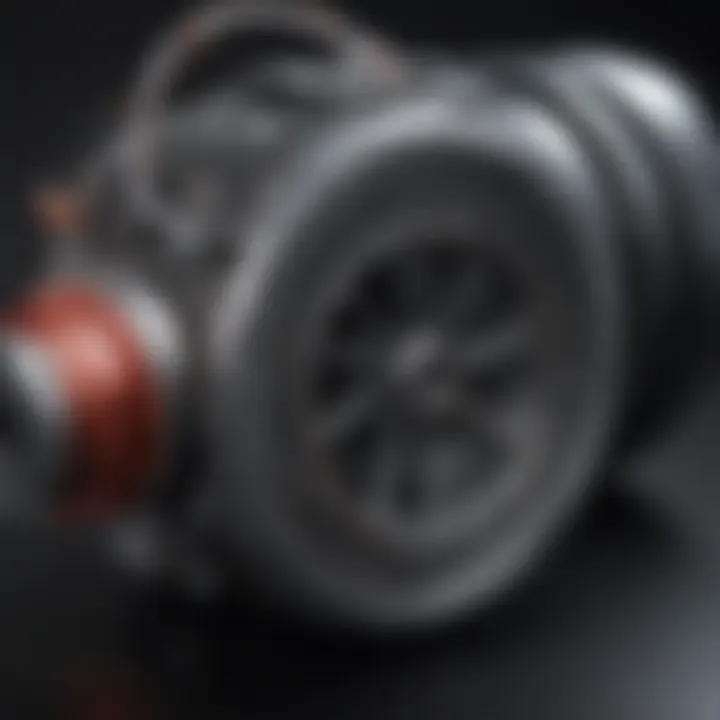
The aerospace sector is among the foremost adopters of metal-plastic hybrid printing technology. Components created through this technique benefit from reduced weight without compromising structural integrity, which is crucial in aerospace applications. For instance, parts like brackets and housings often integrate aluminum or titanium with polymer matrices, significantly lowering the overall weight of aircraft while retaining essential strength.
- Application Areas:
- Benefits:
- Aircraft components such as lightweight brackets.
- Fuel-efficient engine parts that are adapted for high-performance applications.
- Enhanced durability and resilience in high-stress environments.
- Reduction in fuel consumption owing to lower aircraft weight.
By adopting hybrid printing, aerospace manufacturers can not only reduce costs by utilizing fewer raw materials but also enhance aerodynamic performance, which is key for meeting modern flight efficiency standards.
Automotive Sector
The automotive industry is rapidly embracing metal-plastic hybrid printing to meet the dual demands of performance and cost efficiency. Hybrid technologies offer the ability to produce intricate parts that save weight and improve fuel efficiency. Consider the production of complex components such as structural reinforcements, housings for electronic components, and even trim pieces combining metals like steel and aluminum with engineered plastics.
- Key Benefits:
- Specific Applications:
- Fewer manufacturing steps leading to reduced costs.
- The ability to create lighter, more efficient vehicles that meet stringent emissions guidelines.
- Seat structures combined with lightweight metals and polymers for enhanced comfort and safety.
- Engine components that incorporate metal for heat resistance and plastic for weight reduction.
As automakers seek to align with environmental goals, the integration of metal and plastic in production processes is becoming a game-changer with regard to sustainable vehicle design.
Medical Devices
In the realm of healthcare, metal-plastic hybrid printing is becoming increasingly significant. The medical field demands precision, biocompatibility, and reliability, making the properties of hybrid materials ideal for various applications. Surgical tools, implants, and prosthetics have been developed using this technology to create customized solutions tailored to individual patient needs.
- Important Applications:
- Benefits to Healthcare:
- Customized implants that fit perfectly into the anatomical needs of patients.
- Surgical instruments that require both strength and lightweight characteristics to ease their handling during procedures.
- Improved patient outcomes due to tailored device designs.
- Reduction in production time for critical medical devices, allowing for quicker availability.
The continued integration of these materials is likely to result in even greater applications and benefits, further solidifying their relevance in modern engineering and design.
Future Directions in 3D Printing with Metal and Plastic
The integration of metal and plastic in 3D printing is not just a passing trend; it signals an era of unprecedented innovation and possibilities. With advancements in material science and manufacturing techniques, the landscape of 3D printing is rapidly evolving. These dual-material capabilities unlock countless applications across industries, influencing everything from production efficiency to product longevity. In this section, we will explore the promising innovations in material science alongside the sustainability considerations that are integral to the future of hybrid 3D printing.
Innovations in Material Science
The enhancement of materials is at the forefront of future developments in hybrid 3D printing. The fusion of metals, such as titanium and aluminum, with versatile plastics is paving the way for high-performance composites that exhibit superior characteristics. Recent breakthroughs have led to specialized filaments that combine the durability of metals with the flexibility and ease of use of plastics.
For instance, researchers are developing composites that integrate carbon nanotubes into plastic filaments. This not only improves mechanical properties but also adds features like electrical conductivity, enabling the creation of complex structures that serve specific functions. Moreover, the introduction of bio-based plastics in conjunction with metals holds immense potential in medical applications—think of customized implants that can safely integrate with body tissues.
Not to be overlooked, the development of smart materials that can adapt and respond to external stimuli is gaining traction. Materials that change properties in response to heat or light offer fantastic opportunities for designs that could transform based on their environment. Here, the innovation isn't merely in combining materials, but in enhancing their individual characteristics to provide functionality that was previously unattainable.
Sustainability Considerations
As the world pivots towards more sustainable practices, the 3D printing industry is pondering its environmental footprint. The integration of metal and plastic can significantly contribute to sustainability efforts—particularly through waste reduction and recycling initiatives. By using additive manufacturing processes, companies can minimize material waste that typically occurs in subtractive manufacturing. This reduction is crucial, especially in industries like automotive and aerospace, where parts can be highly costly and resource-intensive.
Furthermore, the use of renewable materials like bioplastics in conjunction with metals can reduce the reliance on fossil fuels. Companies are now investigating the lifecycle of hybrid products - from material sourcing to end-of-life disposal. The synergy between metal and plastic can lead to more robust recycling strategies, enabling the recovery of metals and the reuse of plastics.
It's also worth mentioning circular economy models that promote the reuse of materials. With advancements in sorting technologies, deconstructing hybrid components for recycling is becoming more feasible. Products designed specifically for easy disassembly can ensure that valuable materials are not lost. As the industry embraces these paradigms, the environmental impact of hybrid 3D printing can be considerably lessened, leading us towards a greener future.
"The future of 3D printing isn't just about making things faster; it's about making them smarter and more responsible."
The End
The integration of metal and plastic in 3D printing presents a cornerstone in the evolution of manufacturing processes. This hybrid approach not only leverages the distinct advantages of each material but also opens up a realm of possibilities that can drive innovation across diverse sectors. In this article, various dimensions of this integration have been explored, emphasizing its relevance in today's rapidly changing technological landscape.
Summary of Key Points
Through our discussion, key takeaways emerge that underscore the significance of this integration:
- Versatility of Materials: The ability to print using both metals and plastics allows for products that are lightweight yet strong. Components can be tailored to specific applications, enhancing performance and functionality.
- Enhanced Mechanical Properties: The combination of metal and plastic can lead to superior mechanical properties, suitable for demanding applications in aerospace and automotive industries.
- Innovative Applications: Industries are already seeing the benefits in terms of cost efficiencies and design flexibility. From customized medical implants to intricate aerospace parts, the applications are diverse and growing.
- Challenges to Overcome: Recognizing the hurdles, such as adhesion strengths and thermal compatibility, is crucial for further advancements in hybrid 3D printing contexts.
Implications for Future Research
Looking ahead, there are numerous implications for further exploration in the realm of metal-plastic hybrid 3D printing. Key areas for future research include:
- Material Development: There is a continuous need to innovate in material science to produce alloys and polymers that can bond effectively and withstand environmental stresses.
- Process Optimization: Refining the existing processes and developing new techniques that allow for seamless integration of these materials could lead to higher efficiency and part quality.
- Sustainability: Future studies might focus on the recyclability of these hybrid materials and the environmental impact of their production, addressing modern demands for sustainability in manufacturing.
In summary, the integration of metal and plastic in 3D printing is not just a fleeting trend but a significant advance in manufacturing technology that holds promise for a wide range of applications, driving both innovation and sustainability.