Exploring Liquid Photoresist: Principles and Innovations
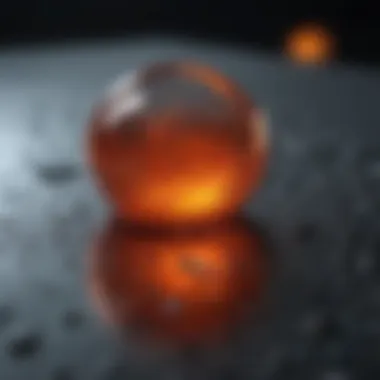
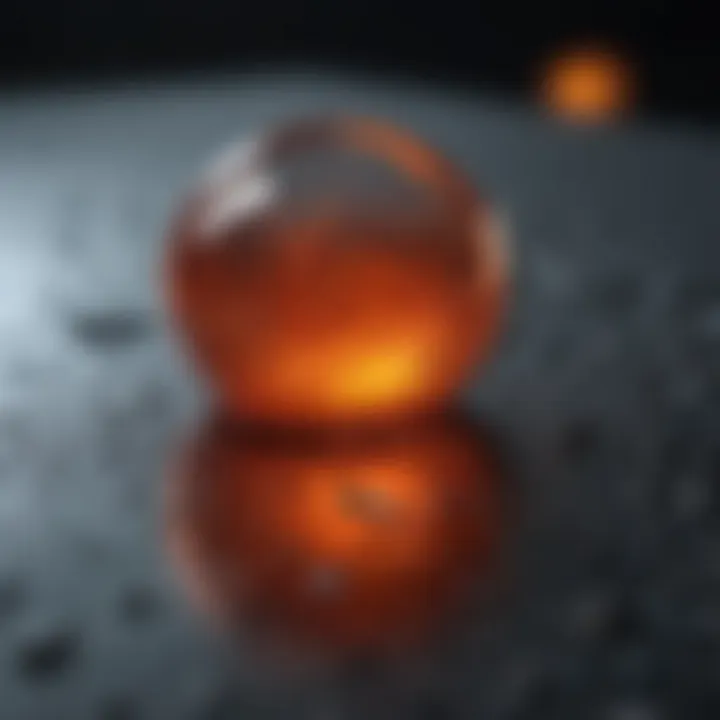
Intro
In recent years, the realm of microfabrication has burgeoned into a vibrant field, driven by the relentless demand for smaller, faster, and more efficient electronic components. At the heart of this technological advancement lies one unsung hero: liquid photoresist. This specialized material plays a pivotal role in the photolithography process, allowing for the precise transfer of intricate micro-patterns onto semiconductor substrates. While it may not be a household name, understanding liquid photoresist is essential for anyone venturing into the microelectronics field or looking to grasp the nuances of modern manufacturing techniques.
Liquid photoresist essentially functions as a light-sensitive material that undergoes a chemical change when exposed to ultraviolet (UV) light. This transformation is what enables the creation of complex circuitry on microchips. Within this article, we will examine not only the fundamental principles underpinning liquid photoresist technology but also its various applications across different industries. Moreover, we will delve into the latest innovations and environmental considerations that shape its use today.
The growing interest in sustainable practices has prompted researchers and industry innovators alike to explore environmentally friendly alternatives to traditional photoresists. As trends evolve, the importance of liquid photoresist in both current and future semiconductor manufacturing cannot be overstated. By walking through these various facets, this resource aims to enlighten students, researchers, educators, and professionals about the significance of liquid photoresist in the cutting-edge landscape of microfabrication.
Each section will serve as a stepping stone leading to a fuller understanding of the immense power and impact of liquid photoresist technology. With that, let’s dive directly into the Methodologies, where we will discuss key research techniques and the essential tools that fuel discoveries in the world of liquid photoresist.
Preface to Liquid Photoresist
Liquid photoresists are a cornerstone of modern microfabrication technology, playing a pivotal role in the intricate processes that define the production of semiconductors and other microelectronic devices. Understanding the nuances of liquid photoresist not only helps bridge the gap between theoretical knowledge and practical application but also reveals the significant advantages and challenges associated with their use.
In an era where miniaturization and precision are key, liquid photoresists offer unique benefits over traditional methods. They provide exceptional resolution and flexibility in design, enabling the crafting of intricate patterns essential for microelectronics. This section will set the stage, offering a comprehensive look into the core aspects of liquid photoresist, encompassing its definition, historical evolution, and a comparison against dry photoresist technologies, laying the groundwork for deeper exploration in the subsequent sections.
Definition and Purpose
Liquid photoresist, in simpler terms, is a light-sensitive material applied to a substrate in ways that allow for selective patterning. When exposed to specific wavelengths of light, portions of this material undergo chemical changes, transforming how they react to the developing solution that follows. This enables the precise etching or deposition of patterns on the substrate.
The purpose of utilizing liquid photoresist goes beyond just creating sharp images. In microelectronics, it empowers manufacturers to define features that are often smaller than a human hair. This capability is pivotal for producing advanced technologies, from integrated circuits to MEMS devices.
Historical Context
The journey of liquid photoresist technology began in the mid-20th century, coinciding with the emergence of integrated circuits. The transition from traditional contact lithography to more sophisticated forms marked a turning point. Early attempts relied heavily on emulsion-based photoresists, but these were limited in resolution and adaptability.
By the 1970s, advancements in polymer chemistry led to significant breakthroughs, propelling liquid photoresists into the spotlight. Notably, the introduction of negative and positive photoresists allowed for greater flexibility in design. This flexibility fundamentally shaped the semiconductor industry, evolving into the standards we see today.
Comparison with Dry Photoresist
When one compares liquid photoresist to its dry counterparts, the differences reveal the remarkable advantages of each. Liquid photoresist tends to provide superior coverage and better detail due to its ability to flow and conform to the substrate's surface. However, it also requires more precise handling to avoid issues like contamination and drying.
In contrast, dry photoresist often provides easier application and less mess, but it can suffer from limitations in terms of resolution and coverage. As each has its own pros and cons, manufacturers tend to choose based on specific needs. For many applications demanding high fidelity, liquid photoresists remain the preferred choice.
"The evolution of photoresist technology has fundamentally transformed microfabrication, leading to innovations that continue to shape the electronics landscape today."
In summary, the introduction to liquid photoresist encapsulates a crucial element of the microfabrication process, setting the stage for further discussion on its principles and applications. Understanding these foundational concepts will enrich the reader’s comprehension of this sophisticated technology.
Fundamental Principles of Liquid Photoresist
Liquid photoresist technology is vital for advancements in photolithography, which is indispensable for modern microfabrication. Understanding the fundamental principles enables researchers and professionals alike to appreciate the intricate balance of chemistry, light, and physical processes that underpin this technology. As industries rely increasingly on precise microstructures, grasping these details becomes crucial for innovation, enhancement of technologies, and maintaining competitive advantages.
Chemical Composition
The chemical makeup of liquid photoresist defines its properties and functionality. At its core, liquid photoresist typically comprises three fundamental components: polymers, solvents, and photoinitiators.
- Polymers: These form the backbone of the photoresist material, contributing to its mechanical properties and adhesion capabilities. The choice of polymer is paramount, as it influences both the etch resistance and the resolution achievable in microfabrication.
- Solvents: Solvents play a crucial role in the uniformity and viscosity of the liquid. They help dissolve the polymer and aid in the application process, allowing for an even coat. However, the volatile nature of solvents necessitates careful handling to minimize exposure risks and environmental impacts.
- Photoinitiators: When exposed to light, these compounds trigger chemical reactions that alter the local properties of the resist. They can either promote cross-linking or degrade the material, depending on the type of photoresist used (positive or negative).
This composition allows liquid photoresists to perform optimally in microfabrication processes, providing the necessary qualities for precision work while also accommodating scalability.
Light Sensitivity and Exposure
Light sensitivity is at the heart of the photoresist operation. The interaction of light with the photoresist leads to the crucial changes required for microstructuring. Exposure is orchestrated through various wavelengths and intensities that dictate the depth of the interaction with the resist.
- Wavelength Dependency: Different types of photoresist materials respond uniquely to varying light wavelengths. For instance, deep ultraviolet (DUV) and extreme ultraviolet (EUV) lithographies utilize different formulations to match their respective light sources.
- Exposure Time: The duration of exposure affects how effectively the photoresist changes. Different applications may require tailored exposure times to achieve desired resolutions or feature sizes. Too little exposure may lead to poor resolution, while excessive exposure can weaken the material beyond its intended limits.
The calibration of light exposure intensity is critical; getting this wrong can derail entire processes.
Developing Process Explained
Once the liquid photoresist has been exposed, the developing process is where the real magic happens. This step transforms the latent image formed during exposure into a tangible structure. Here’s how it typically unfolds:
- Rinse: Initially, the wafer goes through a rinse stage where a specific developer solution is applied. The developer interacts chemically with the exposed areas of the resist.
- Solubilization: For positive resists, the exposed areas become soluble, allowing them to wash away while leaving the unexposed parts intact. Conversely, negative resists behave oppositely, wherein the unexposed regions dissolve instead.
- Post-Development Processing: After developing, additional post-processing steps such as baking may be necessary to solidify the structures and eliminate residual solvent. These steps enhance final product stability and ensure smooth integration into subsequent fabrication stages.
The developing stage is not merely about shape; it's about ensuring that each feature is defined correctly and capable of standing up against the etching and deposition processes that follow.
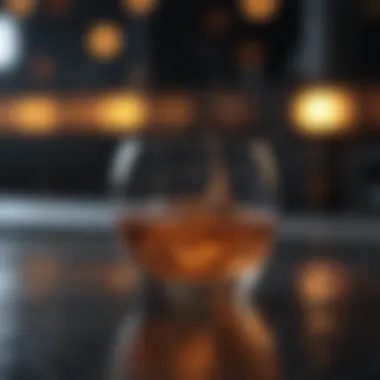
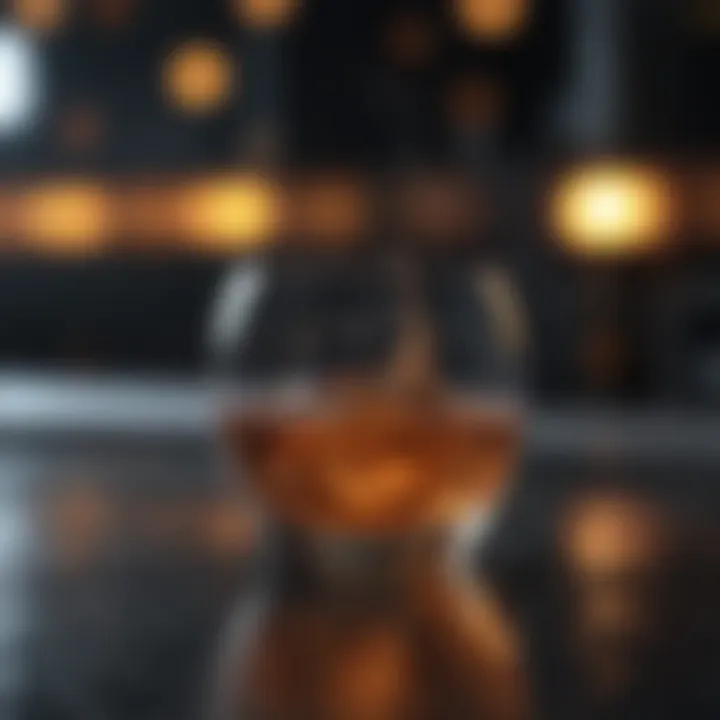
Applications of Liquid Photoresist
The world of liquid photoresist extends beyond mere theory into a dynamic realm of practical applications that are pivotal in contemporary technology. This section zooms in on how liquid photoresists play a critical role across various high-tech sectors, spotlighting their importance in microelectronics, MEMS fabrication, photovoltaics, and printed circuit boards. Each application illustrates the versatility, benefits, and considerations that come with utilizing liquid photoresist, ensuring a comprehensive understanding essential for students, researchers, educators, and professionals in the field.
Microelectronics and Semiconductor Fabrication
Liquid photoresist is the backbone of the microelectronics and semiconductor manufacturing industries. These materials are employed during lithography processes to create intricate patterns on semiconductor wafers. This is key in the production of microchips, where precision and accuracy are non-negotiable. The ability of liquid photoresist to form extremely fine features enables microelectronic devices to become smaller, faster, and more efficient.
The advantages of using liquid photoresist in this context include:
- Enhanced Feature Resolution: The fluidity of the photoresist allows it to flow and settle into the desired patterns, enabling the production of nanoscale structures that are crucial for modern electronics.
- Uniform Coating: Liquid photoresist can be uniformly applied to complex shapes, which is essential for the reliability of components.
- Cost Efficiency: The use of liquid over solid photoresists can also lead to cost savings in terms of material waste and manufacturing complexity.
In short, the role of liquid photoresist in semiconductor fabrication not only underpins the current technological landscape but also paves the way for future developments in the field.
MEMS (Micro-Electro-Mechanical Systems)
Micro-Electro-Mechanical Systems, or MEMS, involve intricate mechanical systems on a micro scale. Liquid photoresist is integral to this technology, allowing for the creation of highly complex structures that can include sensors, actuators, and micro mirrors. The flexibility of liquid photoresist enables the production of three-dimensional structures that are vital in MEMS applications.
"Liquid photoresist's adaptability makes it indispensable in crafting precise MEMS components, emphasizing its importance in the miniaturization of devices."
Some of the key points where liquid photoresist shines in MEMS production include:
- High-Aspect-Ratio Structures: Liquid photoresists can be engineered to produce high-aspect-ratio features, essential for functional MEMS components.
- Rapid Prototyping: The ability to quickly switch between different formulations of liquid photoresist accelerates the prototyping phase, a boon for research and development.
- Integration of Electronics and Mechanics: Liquid photoresist allows for seamless integration of mechanical and electrical components, which is vital for the functionality of MEMS devices.
Photovoltaics and Solar Cells
The solar power industry increasingly turns to liquid photoresist technology to enhance the efficiency of solar cells. Liquid photoresists contribute to processes like patterning thin-film solar cells, facilitating better light absorption and energy conversion.
Some key benefits include:
- Tailored Optical Properties: Different formulations can be designed to optimize the optical characteristics of solar cells, improving their performance under various lighting conditions.
- Streamlined Production Processes: The application of liquid photoresist simplifies the process of creating patterns, thus speeding up the production of photovoltaic panels.
- Improved Material Usage: With the precise application capabilities of liquid photoresist, there is less material waste during the production phase.
Printed Circuit Boards
When it comes to printed circuit boards (PCBs), liquid photoresist is indispensable in both the design and manufacturing processes. As circuits continue to shrink and demands for higher functionality grow, the importance of liquid photoresists in PCB fabrication cannot be overstated.
- Fine Line Patterns: Liquid photoresists enable the creation of fine line features necessary for high-density PCB designs, which are becoming standard in modern electronics.
- Layering Capabilities: The layering processes made possible by liquid photoresist technology help in developing multi-layer PCBs, facilitating the complex connectivity needed in today’s devices.
- Adhesion and Durability: These photoresists often have excellent adhesion properties, which contribute to the overall stability and performance of the PCBs over time.
In summation, the applications of liquid photoresist span several crucial sectors, demonstrating its relevance in advancing technology as we know it. By understanding these applications, researchers and industry professionals can harness the potential of liquid photoresist to drive innovation and improve existing systems.
Innovations and Advancements
The landscape of liquid photoresist technology is constantly ivolving, with innovations playing a crucial role in enhancing performance and application scope. These advancements are not just a few incremental changes; they are pivotal to meeting the demands of modern microfabrication processes. Innovations in this field aim to address key challenges such as resolution, material sustainability, and compatibility with advanced manufacturing techniques. Consequently, this section will delve into three specific areas of advancements ten scholars and professionals alike are eager to explore: emerging materials, nano-resolution techniques, and their integration with sophisticated lithography methods.
Emerging Materials
When we talk about new materials, we refer to substances that can outperform traditional photoresists in several manners. The focus is on enhancing properties like sensitivity, resolution, and environmental impact. For instance, high-performance polymers and biodegradable materials are attracting attention. These materials can provide a dual benefit: better performance and lowered ecological footprints.
Moreover, novel formulations such as:
- Fluorinated resists which offer improved etching resistance
- Polymer blends designed to enhance mechanical properties
These have the potential to significantly broaden the application of liquid photoresists in various industries, from electronics to renewable energy.
Nano-Resolution Techniques
Achieving unparalleled resolution is one manific challenge in the world of microfabrication. Innovations in nano-resolution techniques are leading the charge here. Technologies such as electron-beam lithography and X-ray lithography are helping to achieve incredibly fine features that were previously deemed unattainable.
These methods leverage the capabilities of liquid photoresist materials to create structures in the nano-scale, facilitating intricate designs that ultra-modern electronics demand. By pushing the boundaries of what’s possible, designers can now implement miniaturization trends in specific sectors like biotechnology and aerospace. Here is a list of some key nano-resolution methods:
- Direct-write lithography
- Nanoimprint lithography
Using these cutting-edge techniques allows manufacturers to optimize yield and functionality greatly. Moreover, adapting liquid photoresist within these methods brings forth new opportunities for innovation in design.
Integration with Advanced Lithography Methods
The advancement of liquid photoresist technology goes beyond just independent innovation; it's about how these materials integrate with existing lithography methods. Collaboration with advanced techniques like extreme ultraviolet (EUV) lithography enhances capabilities, bringing unprecedented advantages to the photolithography process.
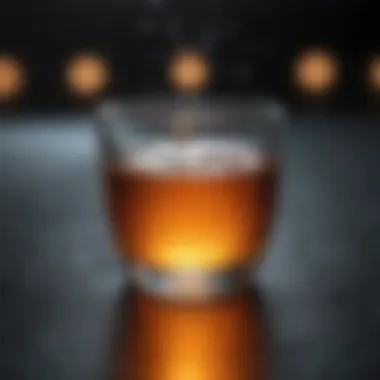
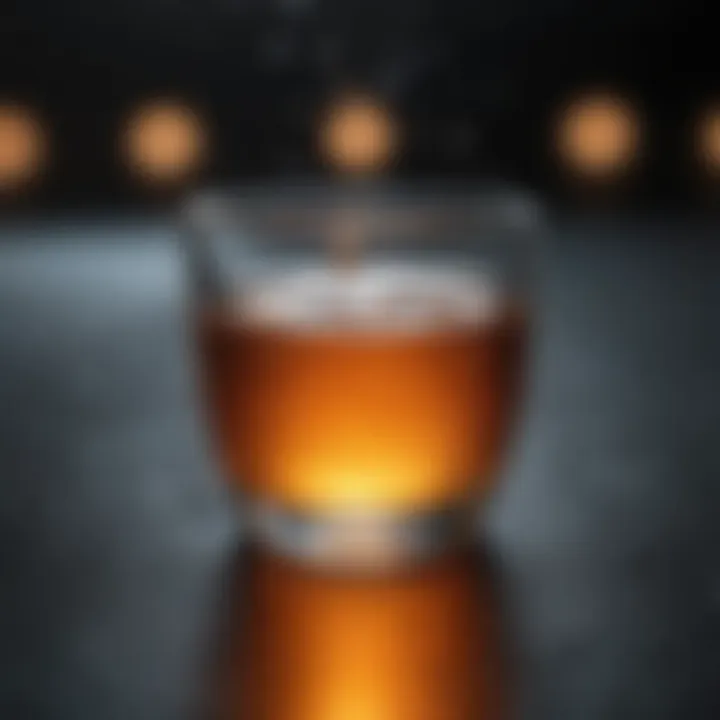
Liquid photoresist can be modified to optimize for performance under EUV conditions, enabling better performance and efficiency in the semiconductor manufacturing processes. The adaptable nature of these photoresists allows engineers to fine-tune formulations, thus:
- Maximizing sensitivity
- Improving film thickness uniformity
As result, manufacturers can not only increase production rates but also reduce waste, aligning closely with sustainable practices in manufacturing.
“A successful integration of innovations in liquid photoresist and advanced lithography can open doors to countless possibilities in electronics.”
In summary, the innovations driving advancements in liquid photoresist technology are necessary for future-proofing industries heavily reliant on microfabrication. Reasons range from the pursuit of better materials to techniques that drive down costs and amplify output efficiency. Each component plays an integral role in not just maintaining relevance in a competitive field, but in leading the charge toward a more sustainable and technologically advanced future.
Environmental Considerations
Understanding the environmental implications of liquid photoresist technology is crucial for its sustainable development and adoption in various industries. As the demand for microfabrication technologies continues to grow, so does the importance of making informed choices that minimize adverse environmental impacts. This section will explore the sustainability of materials, the practices for waste management, and the necessity for regulatory standards and compliance.
Sustainability of Materials
The sustainability of the materials used in liquid photoresist formulations covers both the source and the lifecycle of these chemicals. Manufacturers are increasingly focusing on bio-based or renewable resources to develop eco-friendlier photoresists. These alternatives help reduce reliance on petrochemical derivatives, which have considerable environmental consequences during extraction and processing.
Furthermore, research is continually ongoing to enhance the biodegradability of these materials. Traditional liquid photoresists often persist in the environment, leading to concerns regarding long-term pollution and toxicity. A shift toward materials that break down more easily can mitigate these issues, enabling a more circular approach to product lifecycle management.
For instance, the development of hybrid photoresists, which combine synthetic and organic components, has shown promise in balancing performance with environmental impact. This innovation not only improves the efficiency of microfabrication but also aligns with sustainable development goals.
Waste Management Practices
Proper waste management practices are essential in the liquid photoresist industry to minimize environmental harm. The handling of photoresist waste requires strict adherence to protocols that prevent hazardous substances from entering the ecosystem. Various industries are adopting three main practices to manage waste effectively:
- Segregation of waste: Separating liquid photoresist waste from other types of industrial waste helps in streamlining recycling processes and reducing cross-contamination, which can complicate disposal efforts.
- Recycling initiatives: Some companies have initiated recycling programs where used photoresist can be purified and reused. This not only decreases waste but also cuts down on costs related to raw material sourcing.
- Energy recovery: In certain scenarios, waste photoresist can be subjected to incineration with energy recovery. By converting waste into energy, industries can reduce their carbon footprint while still addressing waste concerns.
Effective waste management not only underscores a company's commitment to environmental stewardship but also enhances its reputation in an increasingly eco-conscious market.
Regulatory Standards and Compliance
The regulatory landscape surrounding liquid photoresist technology is becoming stricter as environmental awareness rises. Compliance with local and international regulations is not just a legal obligation but also an ethical responsibility. For instance, the European Union’s REACH regulations govern the use of chemicals, ensuring that materials are safe for both humans and the environment.
Adhering to these standards often necessitates significant investment in research and development to innovate cleaner and safer formulations. However, it can lead to a competitive edge by establishing a reputation for sustainability. Processors and manufacturers that remain informed about changing regulations are better equipped to adapt their practices accordingly.
Companies that embrace stringent regulatory standards often find themselves one step ahead, adapting swiftly to the market's changing demands.
In summary, environmental considerations in liquid photoresist technology are multifaceted and integral to its future. From material sustainability to waste management and compliance with regulations, every element plays a role in shaping a more sustainable industry.
Challenges Facing Liquid Photoresist Technology
Liquid photoresist technology is a cornerstone of advanced microfabrication processes, yet it does not come without complications. Recognizing and addressing the challenges that encircle this technology is vital for improving its application across various sectors, particularly in semiconductors. The nuances of these challenges can greatly impact the efficiency, cost-effectiveness, and overall success of the processes in which liquid photoresist is employed. Thus, a thorough analysis of these obstacles reveals not only the existing limitations but also potential pathways for innovation and improvement.
Limitations in Resolution
One of the primary hurdles in liquid photoresist technology is its limits in resolution. As the demand for smaller, more intricate circuits increases, achieving high-resolution patterns has emerged as a significant challenge. The resolution in photolithography is often dictated by the wavelength of light used in exposure and the characteristics of the photoresist itself. With traditional liquid resists, there’s a limit to how fine the features can be, especially when compared to advancements in solid photoresist materials.
- Walk the line of balance: While higher sensitivity liquid photoresists have been developed, their performance can sometimes lag regarding pattern fidelity at these minuscule scales. This inconsistency can be frustrating for manufacturers who need precision in their microelectronics fabrication. Resolving this issue will require innovation in material science, focusing on increasing the resolution capabilities while maintaining a suitable viscosity that allows for proper application and coating.
Adhesion and Film Thickness Issues
Adhesion of photoresist to substrates is another sticky situation. The process of coating a substrate with liquid photoresist must ensure not only a uniform thickness but also a strong bond between the resist and the underlying material. Issues of adhesion can lead to delamination during development and processing, rendering the patterns unreliable.
- Inconsistencies in film thickness can also result in uneven exposure and development outcomes, compromising the entire lithography process. When this happens, it’s crucial to evaluate the methods of application and the properties of the photoresist being used. Solutions may involve optimizing the spin-coating process or developing new formulations that enhance adhesion properties while allowing for consistent film thickness across differing substrates.
Cost Considerations
Lastly, the costs associated with liquid photoresist technology can be a double-edged sword. While liquid photoresists may offer certain performance benefits, the cumulative expense of raw materials, processing, and waste disposal can tilt the balance against their use in favor of other technologies.
- Economic pressures: Companies often face tight budgets and must consider how the costs of materials translate to operational efficiency. There's a growing need for cost-effective formulations that do not compromise on quality. Moreover, advancements in recycling methods for photoresist and better waste management practices could alleviate some of these financial burdens. Achieving this balance can potentially make liquid photoresists a more attractive option moving forward.
"The road ahead for liquid photoresist technology isn't without bumps. Addressing resolution limits, adhesion issues, and costs will pave the way for better applications in microelectronics."
Each of these challenges must be met head-on if liquid photoresist technology is to fulfill its potential in modern manufacturing processes. Addressing these difficulties is key not only to enhancing the quality and efficiency of production but also to reducing environmental impacts and costs in the long run.
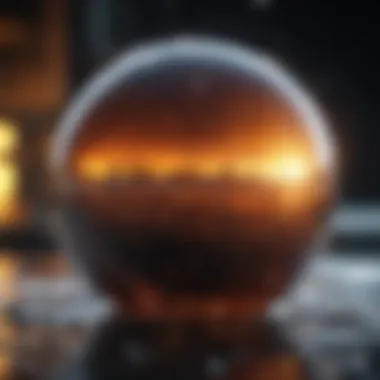
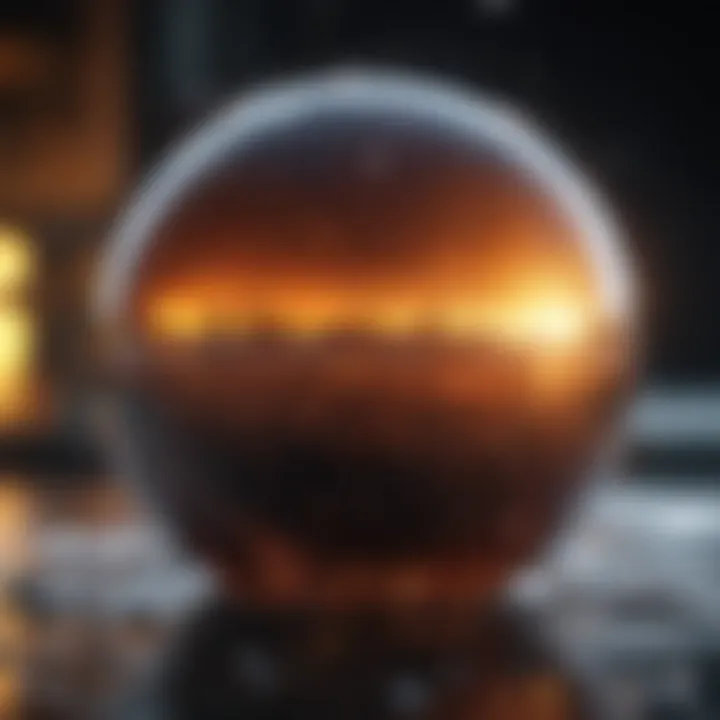
Comparative Analysis with Alternative Technologies
In assessing the landscape of photolithography, one cannot escape the importance of comparing liquid photoresist technologies to other methodologies. This section not only highlights the distinctions but also reflects on the technological advancements and the practical advantages or limitations these alternatives might introduce. By exploring various techniques, readers can grasp the broader implications on performance, cost-efficiency, and application suitability within diverse industries.
Solid Photoresists
Solid photoresists have been around for a significantly long time, providing a, straightforward way of patterning substrates. Unlike their liquid counterparts, solid photoresists are notably easier to handle in terms of application methods. With a dry state, there’s less risk of contamination and a longer shelf life without the worries often associated with solvents in liquids.
However, one must consider some key limitations:
- Thickness Control: Coating films with uniform thickness can be trickier with solids. The inherent properties could lead to non-uniform deposits that might affect the resolution.
- Sensitivity: Solid photoresists often exhibit lower sensitivity to light compared to some modern liquid formulations, which impacts the depth of exposure needed.
Despite these challenges, the solid form still plays an integral role, especially in specialized sectors that necessitate durability under high heat or aggressive chemical environments.
Nanoimprint Lithography
Nanoimprint lithography (NIL) offers a fascinating alternative that caters primarily to nanoscale patterning requirements. It operates through a different mechanism, involving mechanical stamping rather than light exposure, which can lead to patterns that are much finer than what traditional photoresists can achieve. Here’s a look at its advantages:
- Higher Resolution: NIL enables patterning at sub-10 nm scales, pushing the frontiers of manufacturing.
- Material Efficiency: This method typically demands less resin, making it economically appealing.
Nevertheless, it does come with its issues:
- Tooling Costs: Initial setup costs for NIL can be prohibitive, often demanding advanced machinery and precise control systems.
- Process Complexity: The multi-step processes of imprinting and subsequently curing can complicate production workflows.
Other Lithographic Techniques
The lithography field boasts numerous other techniques, such as electron beam lithography (e-beam), extreme ultraviolet lithography (EUV), and maskless lithography systems. Each has distinct characteristics:
- E-beam Lithography: Offers outstanding resolution but is usually slow and not suitable for mass production due to time constraints.
- EUV Lithography: This represents cutting-edge tech, reducing wavelength to create intricate patterns but demands high operational costs and specialized environments that can serve as a barrier for many smaller firms.
- Maskless Lithography: It presents a flexible option for prototyping. Enabling rapid change in design without the need for physical masks can save time and resources, though speed becomes a drawback for large-scale applications.
Future Trends in Liquid Photoresist Technology
As the landscape of technology constantly evolves, liquid photoresist remains at the forefront of innovation in microfabrication. The future of this technology holds significant promise, not only for existing applications but also for groundbreaking advancements that could reshape entire industries. Understanding these trends is vital for researchers, engineers, and companies aiming to capitalize on emerging opportunities.
Market Predictions and Growth
The liquid photoresist market is anticipated to undergo substantial growth in the coming years. Research suggests that several factors drive this expansion:
- Increasing demand in electronics: With the rise of smart devices, IoT, and even more intricate semiconductor technologies, the necessity for reliable liquid photoresists has never been more pressing. As these sectors continue to flourish, the associated demand for high-quality photoresist materials is inevitable.
- Advancements in material science: Continuous research into more effective formulations promises to improve the performance and adaptability of liquid photoresists. This includes exploring novel chemical compositions that enhance light sensitivity and resolution, ultimately broadening their application scope.
- Sustainability initiatives: As industries pivot towards greener practices, liquid photoresist technology will likely embrace eco-friendly materials and methods. Sustainability might not just be a trend; it could become a significant selling point, influencing purchase decisions in the near future.
Greater investment in R&D will also fuel this growth, producing new products tailored to specific niche markets. Firms that can pivot and innovate in this space should expect not just survival, but considerable profit.
Integration into Next-Generation Electronics
The integration of liquid photoresist in next-generation electronics is expected to usher in a new era of functionality and miniaturization. Here are key areas to watch:
- Flexible electronics: As we see a rise in flexible and wearable technology, liquid photoresists can enable the production of components that are lighter, thinner, and bendable. This will likely lead to products that offer better comfort and usability in everyday life.
- 3D integration: Future technologies will increasingly require the stacking of microelectronic components. Liquid photoresists will be integral in achieving precise layering during chip production, allowing for more compact and powerful electronic systems.
- Advanced photonics: The ongoing development in optical applications, particularly solid-state lighting and sensors, will require higher-performance photoresists. As these applications expand, the demand for tailored liquid formulations will grow correspondingly.
Research Directions and Funding Opportunities
Research into liquid photoresist technology is set for a robust trajectory, aligning with trends in other scientific fields:
- Collaborative efforts: Enhanced cooperation between academia and industry will foster innovation. Universities will likely partner with technology firms to explore cutting-edge formulations and applications of liquid photoresists.
- Funding for sustainability: With a growing emphasis on environmental impact, funding bodies might prioritize projects that develop eco-friendly photoresist materials or processes that minimize waste. This avenue is poised for exploration and could yield insightful breakthroughs.
- Focus on nano-resolution: The push towards nano-engineering will require research into liquid photoresists that can function efficiently at nanometer scales. Areas such as quantum computing and nanoscale electronic devices will greatly benefit from advancements in this domain.
The future of liquid photoresists is optimistic, with trends indicating a vast frontier of opportunities. Staying abreast of these developments is crucial for all stakeholders in the microfabrication and semiconductor fields, ensuring that the technology not only adapts but thrives in this dynamic environment.
Epilogue: The Role of Liquid Photoresist in Modern Technology
Liquid photoresist is an essential piece of the puzzle in the rapidly evolving domain of microfabrication and semiconductor technology. It isn’t just a chemical compound; it plays a pivotal role in determining the functionality and efficiency of microelectronic devices. With the ongoing miniaturization of components, the need for precise and reliable methods of patterning becomes even more crucial. Liquid photoresist technology supports this demand by allowing intricate designs and high-resolution patterns, which are necessary in applications ranging from smartphones to advanced medical devices.
Beyond merely providing the means to create patterns on silicon wafers, liquid photoresist also serves as a metaphorical bridge between the theoretical and practical aspects of semiconductor manufacturing. This substance reflects the progress we have made in technology, blending chemistry, physics, and engineering into a cohesive unit that drives innovation.
Summary of Key Points
- Fundamental Properties: The uniqueness of liquid photoresist lies in its chemical composition and the critical role of light exposure. The sensitivity of these materials to specific wavelengths enables the precise trapping of information that defines electrical circuits.
- Varied Applications: From the production of microelectronics to solar cells, liquid photoresist extends its utility across various industries. Expecting its implementations only to be confined within one realm is quite myopic.
- Sustainability Focus: Today, the push toward environmentally friendly practices is influencing the development of liquid photoresists. Addressing waste management and sustainability is essential for future growth and regulatory compliance.
- Challenges and Solutions: Although liquid photoresists offer various advantages, challenges in resolution and adhesion persist. The industry continues to explore innovative solutions to tackle these pressing issues.
Final Thoughts on Future Developments
Looking ahead, the trajectory for liquid photoresist technology seems promising, yet it comes with its challenges. Integration into next-generation electronics is paramount, but this will require continual advancements in materials and application techniques. Research funding is also an important part of this journey as it underpins innovative explorations that can lead to groundbreaking discoveries.
"As we advance, the intersection of technology and materials science will likely open new avenues for liquid photoresists, pushing the boundaries of what’s possible in microfabrication."
Moreover, the relationship between liquid photoresist and the growing demands for smaller, faster, and more efficient electronic devices cannot be overlooked. In the quest to develop next-generation technologies, adapting and evolving liquid photoresist applications is crucial. Whether it's enhancing its properties for better performance or creating more sustainable materials, the future holds intriguing possibilities for this technology.