Comprehensive Guide to 3D Printing: Principles and Innovations
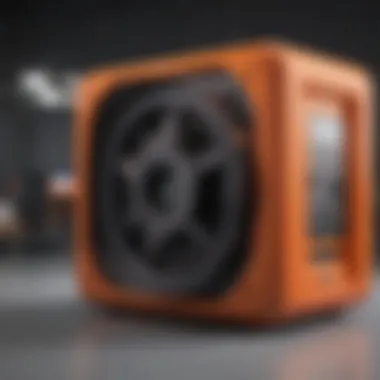
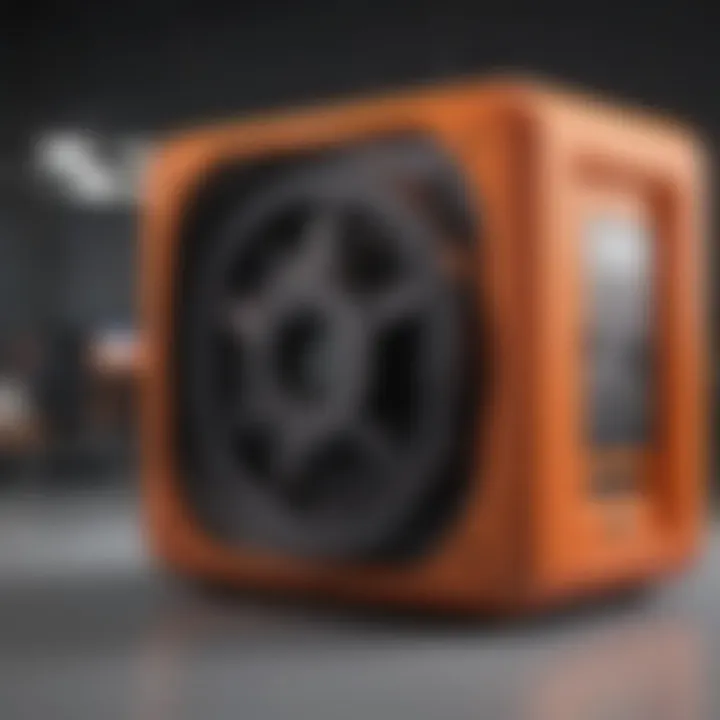
Intro
3D printing has fundamentally changed how industries operate in today's world. As a form of additive manufacturing, it enables the layer-by-layer construction of three-dimensional objects, a method that contrasts significantly with traditional subtractive processes. Industries from aerospace to healthcare leverage this technology, underscoring its wide applicability and revolutionary potential.
This guide aims to explore the principles and methodologies of 3D printing, offering a holistic view of its impact across various sectors. Through an examination of the types of technologies, materials, and applications, we uncover not only its advantages but also the challenges and future directions this domain may take. By addressing sustainability and regulatory considerations, we present a critical analysis that informs researchers and professionals.
Methodologies
Description of Research Techniques
In studying 3D printing, several research methodologies will be employed. The exploration begins with qualitative investigations, which include literature reviews and case studies of existing applications. Interviews with industry professionals provide real-world insights into implementation challenges and innovations. Additionally, quantitative methods such as surveys and statistical analyses may be applied to assess the performance metrics and user satisfaction in various contexts.
Tools and Technologies Used
Researching 3D printing necessitates the use of specialized tools and technologies. Some key instruments include:
- 3D Printers: Various models like the Ultimaker S5 and Formlabs Form 3 are commonly studied for their features and applications.
- Software: CAD software such as SolidWorks or AutoCAD for design preparations is crucial.
- Testing Frameworks: Tools for evaluating material properties and print quality enhance the research integrity.
Discussion
Comparison with Previous Research
Prior studies have laid the groundwork for understanding 3D printing's transformative influence. Comparative analyses highlight that while initial research primarily concentrated on prototype development, recent inquiries have widened the scope to include applications in production environments.
Theoretical Implications
The implications of this research span theoretical frameworks within manufacturing and design sciences. The concept of mass customization emerges as a significant outcome of 3D printing capabilities, pushing the boundaries of what is possible in production processes. Moreover, advancements in materials science challenge existing paradigms, indicating that the future holds significant potential for even more innovative applications.
"3D printing is not just about creating objects; it's about redefining the way we conceive production in modern society."
By delving into these methodologies and discussions, this guide aims to provide a comprehensive understanding of 3D printing, its applications, and what lies ahead.
Prelude to 3D Printing
3D printing represents a significant shift in manufacturing and production processes. Its rise has been facilitated by advances in technology, which allow for the creation of complex structures with remarkable precision. This section aims to elucidate the importance of 3D printing, detailing its definition, applications, and historical context, which set the stage for understanding its transformative impact on various industries.
Definition and Overview
3D printing, commonly referred to as additive manufacturing, is a method of creating three-dimensional objects from a digital file. This process builds objects layer by layer, using materials like plastics, metals, and ceramics. Unlike traditional manufacturing methods that often subtract material to create an object, 3D printing adds material incrementally. This fundamental difference allows for greater design flexibility, reduced material waste, and the potential for on-demand production.
The practical implications of 3D printing are vast. From rapid prototyping to bespoke manufacturing, it enables quick iterations and customization that were not possible with conventional techniques. Industries such as automotive, aerospace, healthcare, and fashion are beginning to harness these benefits to innovate and enhance productivity.
Historical Development
The inception of 3D printing dates back to the early 1980s. The first significant technology developed was stereolithography (SLA), which Charles Hull patented in 1986. This technology used ultraviolet light to solidify photopolymer resins, creating objects layer by layer. Other technologies soon followed, including Fused Deposition Modeling (FDM) introduced by Scott Crump in 1988, allowing for the use of thermoplastics in 3D printing.
In the 1990s and early 2000s, advancements continued, with several 3D printing systems emerging, driven by academic and commercial interest. As knowledge grew and costs fell, the accessibility of 3D printing expanded. By the 2010s, several companies, including Stratasys and 3D Systems, began to offer desktop 3D printers for consumers and businesses.
Today, 3D printing stands as a cornerstone of modern manufacturing, reflecting its journey from niche applications to widespread use across diverse sectors. It has evolved from a prototyping tool to a viable means of production, influencing not only what is manufactured but also how it is designed and used.
Fundamental Principles of Additive Manufacturing
Understanding the fundamental principles of additive manufacturing is crucial for grasping how 3D printing technology operates and its implications for various fields. Additive manufacturing is distinguished by its layer-by-layer construction process, thereby enabling complex geometries that traditional manufactuing methods struggle to achieve. This section delves into two primary components: layer-by-layer construction and how additive manufacturing differs from conventional subtractive approaches.
Layer-by-Layer Construction
The essence of additive manufacturing lies in layer-by-layer construction. This method involves adding material incrementally to create a three-dimensional object. Unlike more conventional methods, which often remove material from a solid block, additive manufacturing builds its designs from the ground up.
This technique offers significant benefits:
- Design Freedom: Complex shapes and intricate designs can be fabricated without the need for specialized tooling.
- Material Efficiency: Since material is only added where necessary, waste is significantly reduced compared to subtractive methods.
- Rapid Prototyping: Ideas can be turned into parts quickly, making it easier for designers and engineers to iterate and refine their products.
A typical process begins with creating a digital model of the object using computer-aided design (CAD) software. The 3D printer slices this model into thin horizontal layers, and the printer constructs the object layer by layer until it is complete. Each layer bonds to the layer beneath it, gradually building the final product. This method has proven to be beneficial across diverse sectors, from aerospace to medical applications, allowing for tailored solutions that were previously impossible.
Differences from Subtractive Manufacturing
Additive manufacturing bears a fundamental contrast to subtractive manufacturing. In subtractive manufacturing, material is removed from a solid block through processes such as cutting, milling, or drilling. This can lead to inefficiencies and waste, as often a large portion of the original material is discarded.
Key differences include:
- Material Utilization: Additive techniques often exhibit higher material utilization rates, decreasing waste.
- Production Flexibility: Adjustments to designs can be implemented more easily in additive processes since no retooling or setup is necessary.
- Customization: Print jobs can readily be adjusted for one-off products without changing the production line, enabling high levels of customization.
This understanding of the fundamental principles of additive manufacturing is pivotal, as it sets the stage for exploring the various technologies and materials involved in 3D printing. The shift from traditional methods allows industries to innovate and improve their practices, creating new possibilities for design and production.
Types of 3D Printing Technologies
Understanding the different types of 3D printing technologies is essential for grasping the transformative impact of additive manufacturing on various industries. Each method has unique characteristics, benefits, and limitations that make them suitable for specific applications. As industries strive for efficiency, customization, and creativity, exploring these technologies becomes increasingly relevant.
Fused Deposition Modeling (FDM)
Fused Deposition Modeling is one of the most common 3D printing technologies. FDM functions by extruding a thermoplastic filament through a heated nozzle. The material is laid down in layers to create a three-dimensional object.
Benefits of FDM include:
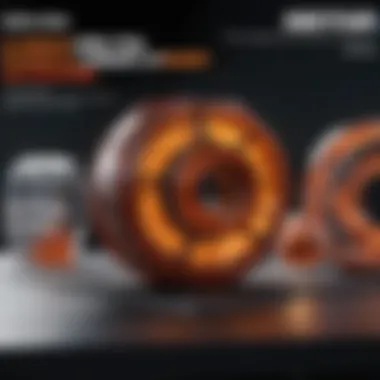
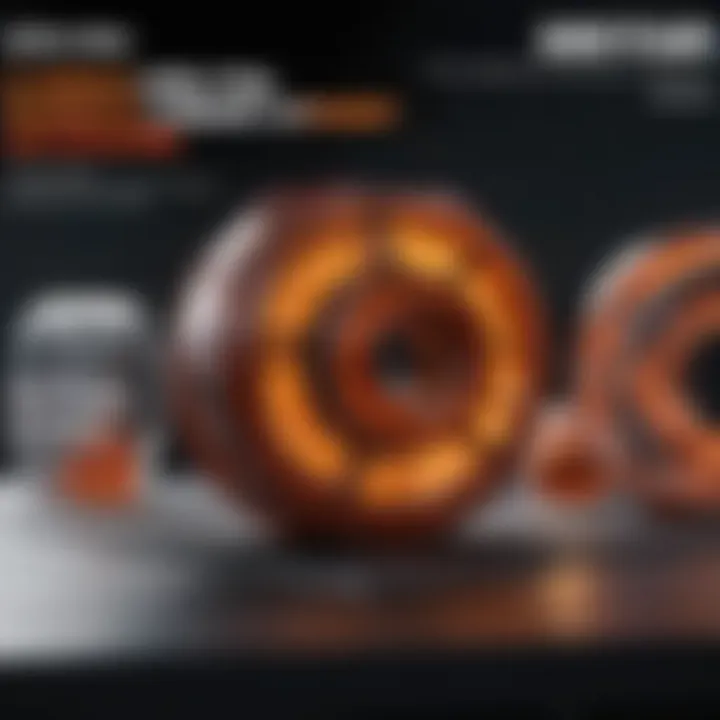
- Cost-Effectiveness: The equipment is relatively inexpensive compared to other types of 3D printing technology.
- Material Variety: FDM supports various materials like PLA, ABS, and PETG, improving versatility in applications.
- Ease of Use: Many users find FDM printers easy to operate and maintain.
However, FDM may not achieve the same precision and surface finish as other technologies, and it tends to have limitations with strength and resolution depending on the settings utilized.
Stereolithography (SLA)
Stereolithography employs a completely different approach than FDM. SLA uses ultraviolet light to selectively cure liquid resin in a build platform layer by layer.
Significant advantages of SLA include:
- High Resolution: SLA produces objects with superior detail and smooth surfaces, making it ideal for intricate designs.
- Fast Prototyping: It is effective in creating prototypes rapidly, thus enhancing the design iteration process.
Yet, SLA materials can be more expensive, and the finished products may require post-processing to achieve desired results.
Selective Laser Sintering (SLS)
Selective Laser Sintering is distinct because it utilizes a laser to fuse powdered material, typically plastic or metal, into solid structures. The laser selectively melts the powder according to the desired model.
Key features of SLS are:
- Complex Geometries: SLS enables the creation of highly complex parts that cannot be manufactured via traditional methods.
- Strength: Finished parts often exhibit good mechanical properties, making SLS suitable for functional prototypes or end-use parts.
Nonetheless, SLS requires a more significant initial investment, and post-processing may be needed to clean up the parts.
Binder Jetting
Binder Jetting is another innovative method that deposits a binding agent onto a powder bed, layer by layer. After printing, the object is usually infiltrated with a secondary material to enhance strength.
The advantages of Binder Jetting include:
- Material Flexibility: A variety of materials, including metals and ceramics, can be used effectively.
- Lower Costs: Compared to some technologies, Binder Jetting can be cheaper for certain production runs.
However, parts produced may lack the same level of strength as those made with SLS or SLA and typically require post-processing steps.
Digital Light Processing (DLP)
Digital Light Processing is similar to SLA but employs a digital light projector to cure resin across the entire layer at once. This can significantly speed up the printing process compared to SLA, which cures one dot at a time.
DLP's major advantages include:
- Speed: DLP can produce parts much faster than SLA, offering a time-efficient option for prototype development.
- Good Surface Finish: Like SLA, DLP can produce smooth surfaces and fine details.
However, while still effective, it can be limited in the materials it's compatible with compared to FDM or SLS.
Each of these technologies has specific applications where they excel. Therefore, choosing the right method depends on the desired outcome, material requirements, and budget considerations.
Materials Used in 3D Printing
The discussion of materials used in 3D printing is crucial to understanding the capabilities and limitations of this technology. Each material has unique properties that affect how it can be utilized in various applications. The selection of the right material allows designers and engineers to create products that not only meet functional performance requirements but also can be cost-effective. The choice of materials impacts durability, design freedom, and production timelines.
Plastics and Polymers
Plastics are among the most commonly used materials in 3D printing. They offer several advantages. For instance, plastics like acrylonitrile butadiene styrene (ABS) and polylactic acid (PLA) are both popular choices for their ease of use and availability. PLA is biodegradable, making it a favorite for environmental sustainability.
Benefits of Plastics:
- Ease of Printing: Most plastics are designed for user-friendly printing processes, allowing for intricate designs without much effort.
- Cost-Effectiveness: Generally, plastic filaments are less expensive, making them accessible for prototyping and smaller projects.
- Variety: There are numerous types of plastics with varying properties to suit specific needs.
The primary consideration when working with plastics is their mechanical properties. While they are lightweight and durable, they might not be suitable for all applications, especially in high-stress environments.
Metals and Alloys
Metals and alloys are increasingly being utilized in 3D printing for applications that require strength and durability. Technologies such as Selective Laser Sintering (SLS) enable the crafting of parts from materials like titanium, stainless steel, and aluminum.
Advantages of Metal 3D Printing:
- High Strength: Metal parts typically offer greater tensile strength compared to plastic.
- Thermal Resistance: Suitable for applications in extreme environments like aerospace.
- Precision: Offers high precision and can create complex geometries that may not be possible with traditional manufacturing.
However, the costs associated with metal 3D printing can be prohibitive for smaller-scale projects. The expertise required for design and post-processing is also a consideration that potential users must keep in mind.
Ceramics and Composites
Ceramics are another category of materials used in 3D printing. They are favored for their hardness and thermal resistance. Applications often include jewelry, art, and industrial uses where standard mechanical properties are insufficient.
Critical Points About Ceramics:
- Durability: Ceramics excel in environments that demand resistance to wear and corrosion.
- Aesthetic Qualities: Many choose ceramics for artistic endeavors due to their finish and ability to hold detail.
Composites combine different materials to enhance performance characteristics. They can include a mix of plastics reinforced with glass or carbon fibers, yielding unique properties.
Bio-materials
Bio-materials represent a fascinating frontier in 3D printing. These materials are derived from natural sources and can be employed in medical applications, such as tissue engineering. The biocompatibility of these materials makes them suitable for implants and prosthetics.
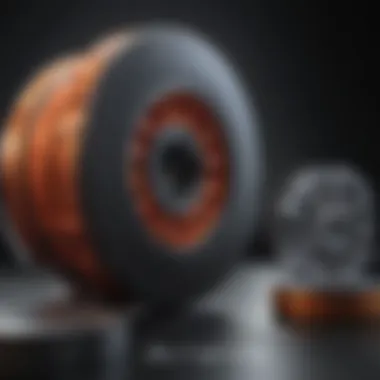
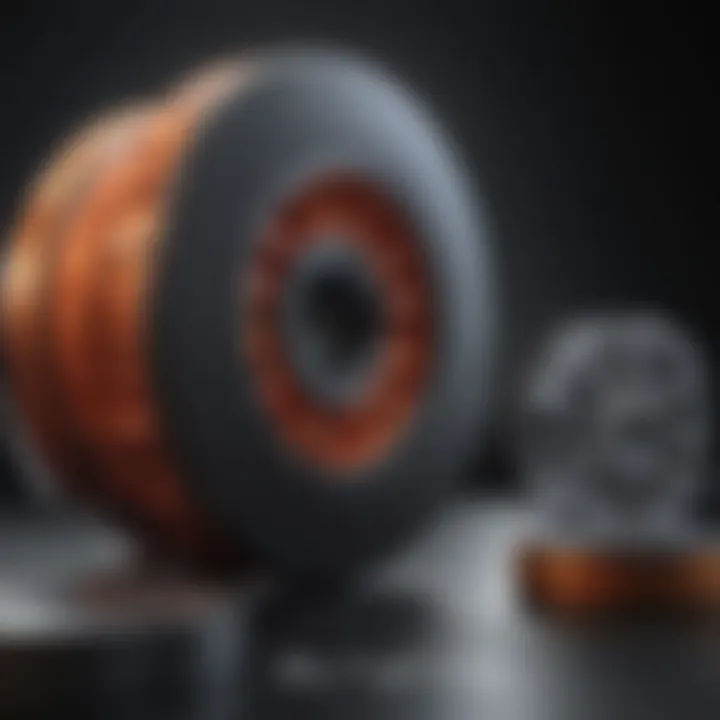
Considerations for Bio-materials:
- Biocompatibility: Essential for medical applications, ensuring they do not cause adverse reactions.
- Customization: Allows for the design of patient-specific solutions in medical fields.
As this technology progresses, materials derived from living organisms are playing a growing role in the customization of healthcare solutions.
"The choice of materials used in 3D printing is a major determinant of the technology’s success in diverse fields, from prototyping to specialized manufacturing."
Understanding materials is fundamental for anyone engaged in 3D printing. The right material selection not only defines the success of a project but also impacts broader applications across industries.
Design Considerations for 3D Printing
Incorporating design considerations into the 3D printing process is essential for achieving successful outcomes. The complexity of 3D printing lies not just in the technology but also in how the designs are crafted. The design must reflect both functional requirements and the specific capabilities and limitations of the selected printing technology.
3D Modeling Software
One of the first steps in 3D printing involves using specialized modeling software to create the digital representation of the object. The software should support the file formats compatible with the selected 3D printer. Some popular options include Autodesk Fusion 360, Tinkercad, and Blender. Each of these programs offers unique features and tools suited for different user experiences and complexity levels.
Using 3D modeling software also allows for adjustments during the design phase. Optimizing geometry for printability includes considering support structures, overhangs, and material flow. These decisions directly impact the quality and durability of the final product. Access to high-quality resources and tutorials can enhance user proficiency, which ultimately results in a successful print.
Design for Manufacturability
Designing specifically for 3D printing can lead to significant benefits in terms of efficiency and product performance. This concept, known as Design for Manufacturability (DFM), optimizes designs so that they can be more easily produced within the constraints of the chosen additive manufacturing technology. DFM involves several key considerations, such as:
- Minimizing complexity: Reducing the number of moving parts and assembly steps can streamline production.
- Orienting parts effectively within the printer: The orientation can influence the strength of the material and surface finish.
- Select materials with appropriate properties: The chosen material must meet specific performance standards for the intended application.
By focusing on these aspects, designers can produce affordable, functional products that meet customer expectations. Additionally, adopting DFM principles will support sustainability by reducing waste.
Simulation and Prototyping
Verification of design is crucial before actual production takes place. Simulation tools can help test how design will perform under various conditions and can predict potential challenges related to material behavior and structural integrity. This step allows designers to make necessary adjustments before the transition to physical models.
Prototyping plays a vital role in the development process as well. Creating a prototype provides hands-on experience and insights not always visible in a digital model. Iteratively refining the design based on prototype feedback can lead to improved functionality and quality. This approach not only saves time but also reduces costs associated with failed prints or flawed designs.
"Using simulation and prototyping to refine design is key to leveraging the full potential of 3D printing technology."
These considerations highlight that effective design practices are vital for 3D printing success, contributing significantly to performance, durability, and sustainability in various applications.
Applications of 3D Printing
The applications of 3D printing are vast and varied, reflecting the transformative potential of this technology across multiple industries. This section highlights the significance of these applications and examines how they enhance processes, foster innovation, and meet emerging needs in different fields. The benefits of 3D printing include improved efficiency, reduced time-to-market, and the ability to produce complex geometries that traditional manufacturing cannot achieve.
Prototyping and Product Development
Prototyping is a critical phase in product development. 3D printing streamlines this process significantly. Engineers and designers can rapidly create physical models of their ideas, allowing for immediate evaluation and iteration. This ability to prototype efficiently leads to shorter development cycles and minimizes costs.
3D printed prototypes can serve not only for testing functionality but also for assessing form, fit, and aesthetics. Companies such as Formlabs and Ultimaker offer tools and machines designed specifically for creating high-quality prototypes. This flexibility permits easier modifications based on feedback, ultimately resulting in better end products that are closely aligned with market demands.
Manufacturing and Production
In manufacturing, 3D printing has the potential to revolutionize traditional processes. Rather than manufacturing large quantities with standard molds, businesses can produce on demand using additive methods. This shift can significantly reduce inventory costs and waste.
3D printing technologies like Fused Deposition Modeling (FDM) and Stereolithography (SLA) allow for mass customization, enabling businesses to tailor products to individual customer specifications without the need for complex tooling. This adaptability is especially valuable in sectors such as consumer goods, where personalization is becoming increasingly important.
Medical Applications
The medical field has embraced 3D printing with remarkable success. Applications range from prosthetics and implants to bioprinting tissues and organs. For example, companies like Organovo are pioneering the bioprinting of tissues for medical research and, potentially, transplantation.
Custom implants can be tailored to fit the unique anatomy of patients, significantly improving outcomes. The ability to print anatomical models from patient scans enhances surgical planning and education, providing realistic representations for training purposes. These advancements illustrate 3D printing's impact on patient care and recovery.
Aerospace and Automotive
The aerospace and automotive industries have also recognized the advantages of 3D printing. Components produced through additive manufacturing are often lighter than their traditionally manufactured counterparts, leading to improved fuel efficiency and performance.
Companies like Boeing and Ford are already using 3D printed parts in their vehicles and aircraft, streamlining production and reducing timeframes. The ability to create complex geometries and lighter parts can lead to significant savings and improve overall functionality.
Art and Fashion
Art and fashion have found unique expressions through 3D printing. Artists are experimenting with the medium to create intricate sculptures, and designers are producing innovative clothing items that would be difficult to produce using conventional methods.
Projects such as Iris van Herpen’s runway shows showcase how fashion can integrate technology and art. These endeavors not only challenge traditional boundaries but also inspire new movements within the creative sector. They demonstrate the diverse possibilities offered by 3D printing for customization and unique designs.
"The future of fabrication is not just about creating things, but also about rethinking what can be made and how products can evolve in our culture."
In summary, the applications of 3D printing are transforming industries by enhancing product development processes, improving healthcare solutions, innovating vehicle design, and redefining artistic creation. As this technology continues to evolve, so too will its potential to meet the demands of various sectors.
Impact of 3D Printing on Sustainability
The significance of 3D printing in the context of sustainability cannot be overstated. As industries are increasingly scrutinized for their environmental impact, additive manufacturing stands out as a solution that can align production with sustainable practices. This section examines how 3D printing positively contributes to sustainability through waste reduction, sustainable material alternatives, and energy consumption considerations. Each of these elements plays a vital role in understanding how this technology can reshape modern manufacturing with fewer ecological footprints.
Waste Reduction in Manufacturing
One of the most notable advantages of 3D printing is its ability to significantly reduce waste compared to traditional manufacturing methods. In subtractive manufacturing, material is often cut away from larger blocks, leading to a considerable amount of excess material. In contrast, 3D printing functions on a layer-by-layer construction basis, utilizing only the material necessary to create the final product.
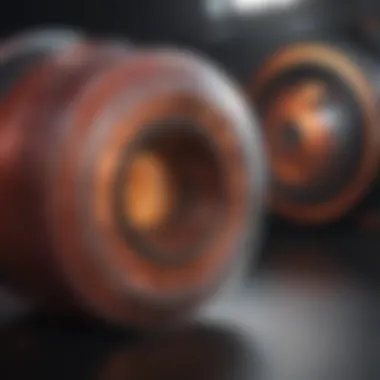
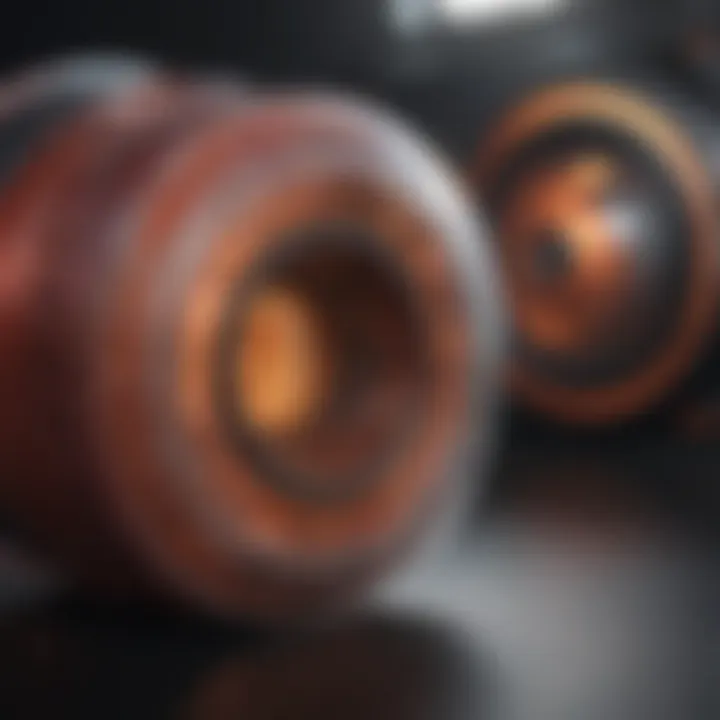
This process not only minimizes material waste but also lowers the costs for manufacturers. Studies indicate that additive manufacturing can lead to waste reductions of up to 90%. Moreover, reduced waste translates to less scrap material that needs to be disposed of, which is an essential factor in sustainable practices. By adopting 3D printing technology, companies can optimize their resources while fostering an environmentally-friendly manufacturing process.
Sustainable Materials Alternatives
In the pursuit of sustainability, the adoption of eco-friendly materials in 3D printing is gaining traction. Traditional materials such as plastics often pose significant environmental challenges, but advancements in material science have led to the development of sustainable alternatives. Biodegradable plastics, such as polylactic acid (PLA), are increasingly used in 3D printing applications.
Additionally, researchers are exploring materials derived from renewable resources, including cellulose and other plant-based compounds. These sustainable materials not only lessen the impact on landfills but can also minimize carbon emissions associated with material production. The move toward using sustainable materials ensures that 3D printing contributes to a circular economy where waste is minimized, and materials can be reused or recycled effectively.
Energy Consumption Considerations
Energy efficiency is another critical component of the sustainability narrative in 3D printing. While 3D printers often have lower energy consumption during production than their traditional counterparts, it is essential to consider the overall energy lifecycle. The energy required to produce the raw materials can offset some of the benefits of reduced operational energy.
However, innovations in this technology are focused on improving energy efficiency further. Manufacturers are creating printers that require less energy per print job and are designing processes that can operate at lower temperatures, thus using less power. Moreover, integrating renewable energy sources into the production environment can enhance the sustainability of 3D printing operations. Reducing energy consumption not only benefits the environment but can also yield cost savings for businesses, making it a win-win situation.
"Sustainability and innovation should go hand-in-hand in the evolution of 3D printing technology. The path forward is clear: the future lies in environmentally-conscious production methods."
Legal and Regulatory Considerations
Legal and regulatory considerations play a significant role in the growth and application of 3D printing technology. As this technology rapidly evolves, it raises various challenges for intellectual property rights, safety standards, and compliance regulations. Without proper legal frameworks, the benefits of 3D printing may not be fully realized, leading to potential disputes and hazards. Thus, understanding these issues is crucial for stakeholders in the 3D printing space.
Intellectual Property Issues
Intellectual property (IP) is a complex topic in the realm of 3D printing. This technology allows for the easy replication of designs, which can blur the lines of ownership and copyright. Designs can be digitized and shared rapidly, making it challenging to protect original work.
Key points include:
- Copyright: Copyright law applies to the designs used in 3D printing. Once a design file is created, it can be copyrighted, but enforcement can be difficult.
- Patents: Innovations in printing processes can be patented. This includes new methods or devices that enhance the printing capabilities.
- Licensing: Licensing agreements can help protect designers while allowing others to use their creations legally.
Legislation must evolve to address these issues. Companies and individuals should be aware of the potential legal ramifications of producing and sharing 3D prints.
Safety and Certification Concerns
Safety and certification in 3D printing are paramount, particularly in sectors like healthcare, automotive, and aerospace where the integrity of printed parts is critical. As the technology matures, so do the regulatory requirements surrounding it.
Several areas of concern include:
- Material Safety: Many materials used in 3D printing, especially plastics and resins, can emit harmful substances if not handled properly. Regulations must ensure that materials meet safety standards.
- Device Certification: Equipment used for 3D printing should comply with safety and performance standards. For instance, printers used in medical applications might need to undergo rigorous testing and certification.
- Quality Assurance: Ensuring the quality of the end product is vital. Standards must be established to ensure consistent results from 3D printers.
A well-defined legal and regulatory framework surrounding 3D printing can foster innovation while protecting inventors and consumers alike. These elements will shape the future of additive manufacturing in a safe and responsible manner.
Future Trends in 3D Printing
The landscape of 3D printing is in constant evolution. Understanding future trends is crucial for anyone involved in this technology. It allows businesses, researchers, and educators to anticipate shifts that can impact various sectors. Future trends will shape how industries operate by making manufacturing processes more efficient and responsive to consumer demands.
Advancements in Technology
New technologies are emerging within the 3D printing sector. These advancements improve the speed, accuracy, and range of materials that can be used. For instance, developments in multi-material 3D printing enable the creation of complex structures that traditional methods cannot achieve.
Other exciting technologies include 4D printing. This technique introduces the element of time into design. It allows printed objects to change shape or function when exposed to specific stimuli such as heat or moisture. This advancement has vast implications, particularly in fields like healthcare and engineering.
Moreover, improvements in software are revolutionizing the design phase. Sophisticated modeling programs streamline the process for engineers.
Integration with Other Technologies
3D printing is not an isolated technology. Its integration with other advanced technologies is transforming production systems. For example, the merging of 3D printing with artificial intelligence enables smarter production processes. AI can optimize designs and predict potential issues before they arise.
Furthermore, the convergence of 3D printing with the Internet of Things (IoT) opens new avenues for real-time monitoring. Smart sensors in 3D printers can provide data on materials and processes, enhancing efficiency.
Collaboration with robotics is also noteworthy. Robots can assist in the printing process, reducing manual labor and increasing output.
Market Predictions and Opportunities
The market for 3D printing is set to expand significantly. Analysts foresee an increase in adoption across various sectors, from manufacturing to healthcare. Investment in 3D printing startups is on the rise, suggesting growing confidence in this technology's capabilities.
Specific areas poised for growth include customized consumer products. This trend addresses the demand for personalization, allowing companies to offer tailored solutions. Additionally, industries like construction are beginning to explore large-scale 3D printing techniques. These methods have the potential to reduce waste and lower costs.
"The future of 3D printing promises to redefine manufacturing and design paradigms. Adapting to these changes is essential."
Closure
The conclusion of this article serves as a reflection on the critical themes discussed throughout the guide. It encapsulates the insights gained regarding 3D printing, a technology that is increasingly pivotal in various sectors. Understanding this topic is essential for students, researchers, educators, and professionals who are engaged in or affected by advancements in technology.
One key element highlighted is the transformative nature of 3D printing. The ability to create complex structures layer by layer has not only changed the landscape of manufacturing but also enabled innovations that were previously deemed impossible. From rapid prototyping to custom medical implants, the applications are vast and varied. This technology reduces timeframes in production and increases customization capabilities, which enhances the efficiency of processes across different industries.
Furthermore, the discussion around sustainability reinforces the importance of considering environmental impacts. 3D printing presents opportunities for waste reduction and the use of sustainable materials, crucial factors in today's manufacturing discussions.
In summary, the conclusion encapsulates the article's aim to not just inform but to provoke thought on how the evolution of 3D printing will continue shaping our future. The ongoing advancements in technology, the merging of different fields, and the regulatory landscapes surrounding it are elements that demand attention and understanding.
Summary of Key Points
- Transformative Potential: 3D printing reshapes industries by providing innovative solutions to production and design challenges.
- Efficiency Enhancement: The technology allows for faster prototyping and greater customization, improving production processes.
- Sustainability Awareness: The shift towards eco-friendly materials and waste reduction showcases the environmental benefits of additive manufacturing.
- Regulatory Considerations: Understanding the legal landscape is important for ensuring compliant innovation in 3D printing applications.
Final Thoughts on the Future of 3D Printing
Looking ahead, the future of 3D printing appears bright. With ongoing advancements in machine design and materials science, we can expect to see more robust and versatile 3D printing technologies. Integration with artificial intelligence and machine learning will likely improve efficiency and design capabilities further.
As industries continue to explore these technologies, new markets will emerge, and established businesses will adapt to leverage the benefits of additive manufacturing. The convergence of various technologies will only amplify the potential for innovation.
3D printing is poised to become a cornerstone in product development and manufacturing processes, suggesting a paradigm shift that may redefine how we approach design, production, and even consumption in the years to come.