Exploring Shot Peening: Enhancing Metal Durability
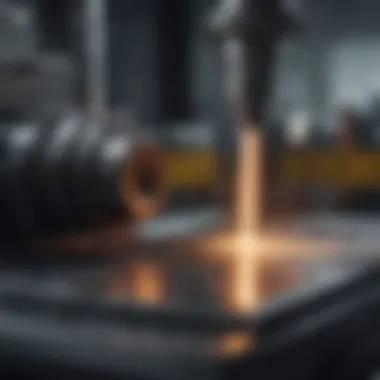
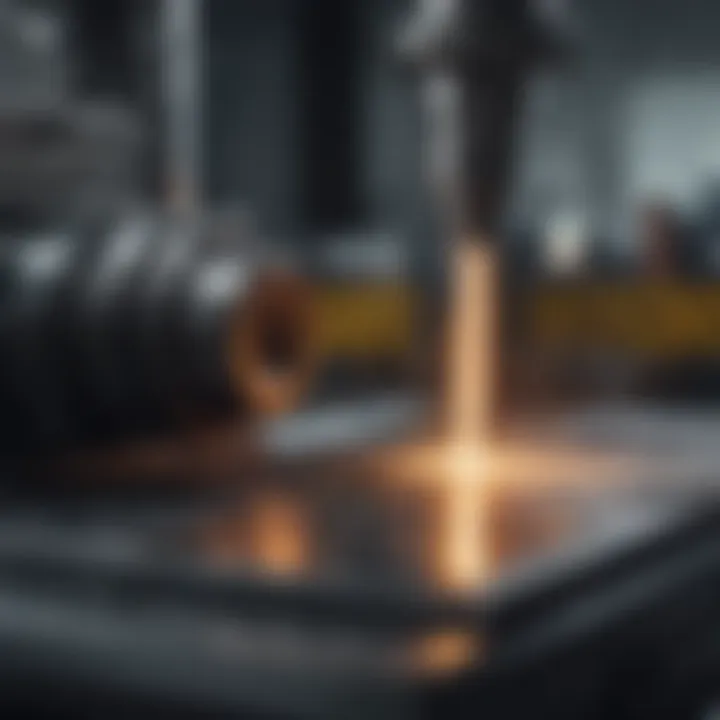
Intro
Shot peening is a crucial process used in metal treatment, heavily influencing the material's properties and lifespan. The main purpose of shot peening is to enhance the fatigue resistance of metals, making it an indispensable technique in engineering applications. This article examines the fundamentals of shot peening, both its practical application and the underlying scientific principles. By presenting a thorough understanding of this method, the discussion includes advancements in technology, comparison with earlier approaches, and recommendations for best practices in different industrial scenarios.
The significance of shot peening extends beyond theoretical concepts. It has direct implications in various sectors, from aerospace to automotive manufacturing, where structural integrity and durability are paramount. As industries push for higher performance materials, the demand for effective surface treatment methods like shot peening continues to grow.
Understanding the mechanics of shot peening helps engineers and researchers make informed decisions that can lead to better product performance and safety. This article aims to provide insights that will enhance the reader’s grasp of the methodology, effects, and applications of shot peening in modern metallurgy.
Methodologies
Description of Research Techniques
Research into shot peening utilizes a variety of methodologies to assess its effectiveness in metal treatment. Common techniques include experimental testing and computational simulations.
Experimental testing often involves:
- Conducting controlled peening trials
- Measuring residual stress impacts through X-ray diffraction
- Assessing fatigue life through cyclic testing procedures
These methods help establish a direct correlation between shot peening conditions and the mechanical properties achieved. Computational models can simulate shot peening processes, allowing researchers to predict outcomes under different parameters without extensive physical experimentation.
Tools and Technologies Used
The advancement of shot peening techniques relies on several modern tools and technologies. Equipment commonly used in the peening process includes:
- Shot peening machines which distribute media like steel or ceramic shots
- Surface measurement devices such as profilometers to gauge surface roughness
- Automated robotics to ensure consistent and repeatable peening patterns
Moreover, advancements in material science contribute to the development of high-performance peening materials, enhancing the overall effectiveness of the process.
Discussion
Comparison with Previous Research
Previous research often focused primarily on the mechanical impact of shot peening on various metal alloys. Recent studies, however, explore not only the immediate mechanical benefits but also the long-term effects on material fatigue and overall durability. This shift reflects a broader understanding of material behavior under multi-axial stress conditions and promotes a more holistic approach to shot peening strategies.
"The evolution of shot peening is reflective of broader advancements in material science and engineering practices."
Theoretical Implications
Theoretical implications derive from how shot peening introduces compressive residual stresses to the surface of materials. This is critical since compressive stresses counteract tensile forces that lead to crack initiation and propagation. When analyzed through the lens of fatigue failure theories, shot peening showcases its significant role in extending the lifespan of components subjected to cyclical loads.
The principles of shot peening interact with quality control processes, impacting overall industry standards. Thus, its theoretical standing not only shapes practical applications but also informs regulatory guidelines across sectors.
Prelude to Shot Peening
Shot peening plays a crucial role in enhancing the performance and lifespan of metal components in various industries. This process induces beneficial compressive residual stresses on the surface of the materials, which enhances their fatigue resistance and overall durability. Understanding shot peening is essential for students, researchers, and professionals in metallurgy and engineering fields. The subsequent sections will elaborate on the various aspects of shot peening, including its definition, historical development, and mechanics.
Definition of Shot Peening
Shot peening is a mechanical process that involves bombarding the surface of metal components with small spherical media, commonly referred to as shots. These shots strike the surface at high velocities, causing plastic deformation. The fundamental purpose of shot peening is to improve the mechanical properties of metal parts, particularly their resistance to fatigue. The process leads to the formation of compressive residual stresses, which counteract the tensile stresses that typically lead to material failure. This technique is widely employed in sectors such as aerospace, automotive, and manufacturing to enhance part performance under cyclic loading conditions.
Historical Context
The origins of shot peening can be traced back to the mid-20th century, around World War II. At that time, military applications for aircraft components, which needed to withstand extreme stress and fatigue, prompted significant interest in methods that could enhance metal durability. The first documented use of shot peening as a surface treatment method was observed during the manufacturing of critical aircraft parts. Over the decades, advancements in technology and material science further refined the understanding and application of shot peening.
As the aerospace industry evolved, so did the techniques used, from manual processes to automated systems. The 1990s saw a significant increase in the adoption of shot peening in the automotive sector, where safety and performance are paramount. Today, this process is standardized across industries, backed by regulations and guidelines to ensure consistency and quality in the treatments applied.
"Shot peening is not just a surface treatment; it is an integral process in enhancing the lifespan and reliability of critical components across various industries."
Mechanics of Shot Peening
Understanding the mechanics of shot peening is crucial for grasping its significant role in enhancing metal properties. This section delves into the fundamental principles, deformation mechanisms, and the development of residual stresses that occur during shot peening. Each element contributes to the overall effectiveness and application of the process in various industries.
Principles of Mechanics
At its core, shot peening is a mechanical surface treatment that utilizes a high-velocity stream of small particles, or shots, to impart compressive residual stress on metal surfaces. This compressive stress is vital as it counteracts tensile stress that contributes to material fatigue. The basic operating principle involves controlling the size, shape, and velocity of the shots to optimize the peening effect on the workpiece. The shots typically bounce off the surfaces and create a unique deformation pattern, contributing to fatigue life enhancement and wear resistance.
For effective shot peening, one must ensure the proper alignment of machines and consistently maintain the velocity of the shots. Variations in these parameters could lead to inconsistent results and diminish the intended benefits of the process.
Deformation Mechanisms
The deformation mechanisms at play during shot peening are complex and multi-faceted. When the shots collide with the metal surface, several outcomes may occur, which can be categorized as:
- Elastic Deformation: Initially, the metal may undergo elastic deformation, where it temporarily deforms upon impact but returns to its original shape once the stress is removed.
- Plastic Deformation: If the energy from the shot exceeds a certain threshold, the metal will experience plastic deformation, leading to permanent changes in its shape. This is the significant part of the peening process, enhancing fatigue resistance.
- Microstructural Changes: Repeated impacts prompt changes at the microstructural level. Grain refinement can occur in the metal matrix, enhancing mechanical properties like strength and toughness.
"The interaction of shot peening forces with the substrate creates changes that are essential for enhancing the material's lifespan."
Residual Stress Development
Residual stresses induced by shot peening are one of the most critical aspects to consider. During the process, the surface of the metal is hardened due to compressive residual stresses. These stresses arise largely from the high-energy impacts of the shots.
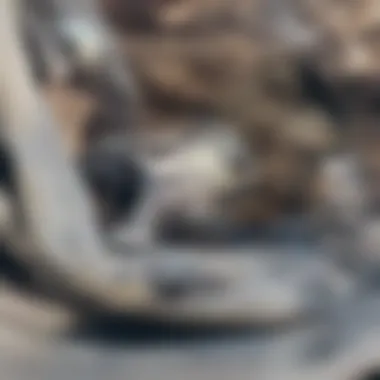

A well-designed peening process should ideally produce a profile of compressed stress that decreases with depth from the surface, while tensile stresses might exist deeper inside the material. The magnitude and distribution of these residual stresses are influenced by multiple parameters, including shot size, peening intensity, and coverage.
Understanding this development helps in designing components that can perform effectively under various loading conditions. It is essential for applications in fatigue-prone industries like aerospace and automotive, where component failure can have catastrophic consequences.
In summary, the mechanics of shot peening intertwine principles, deformation mechanisms, and the development of residual stresses. A robust understanding of these elements is necessary to fully leverage shot peening as a metal treatment method, ensuring its benefits are maximized in industrial applications.
Benefits of Shot Peening
The process of shot peening brings several advantages that are crucial in metal treatment. Understanding these benefits helps in appreciating its application across various industries. With a focus on metal fatigue resistance, enhanced material strength, and improved surface finish, shot peening serves as a vital tool in ensuring the longevity and durability of metal components.
Metal Fatigue Resistance
One significant benefit of shot peening is its contribution to metal fatigue resistance. Fatigue occurs in materials under repeated stress cycles. During the shot peening process, small metallic or ceramic pellets are propelled at high velocity towards the surface of a component. This creates compressive residual stresses on the surface, which counteracts tensile stresses that lead to fatigue failure.
Studies show that parts subjected to shot peening exhibit a marked enhancement in their fatigue life. For instance, aerospace components, which endure extreme cyclic loads, often use shot peening as a preventive measure against crack development. The ability to improve fatigue resistance is essential in maintaining the safety and reliability of high-stress applications.
Enhanced Material Strength
Another vital aspect of shot peening is its role in enhancing material strength. The mechanical deformation induced by shot peening not only reinforces the surface but also improves the overall toughness of the material. When a material is treated with shot peening, it undergoes strain hardening, which increases its yield strength.
For example, steel components that are shot peened can withstand higher loads than their untreated counterparts. This increase in strength allows for designs that can reduce material use while maintaining performance standards. In the automotive sector, shot peening has been widely adopted in manufacturing suspension parts and gears, ensuring durability and reliability under demanding conditions.
Improved Surface Finish
Lastly, shot peening contributes to improved surface finish. The process not only modifies the surface layer but also reduces the presence of micro-cracks and imperfections. A smoother surface is essential for applications where friction plays a role, such as moving parts in engines and gearboxes.
Through the efficient removal of sharper surface features, shot peening helps maintain a controlled surface roughness and enhances the aesthetic attributes of products. High-quality surface finishes also assist in improving the resistance to corrosion and wear, benefiting various industries ranging from aerospace to manufacturing.
"Shot peening is not just about resistance; it’s about shaping the future of metal durability."
In summary, the benefits of shot peening extend beyond the immediate performance enhancements. The processes of improving fatigue resistance, enhancing material strength, and achieving better surface finishes support industries in moving towards more efficient and reliable manufacturing. With these advantages, shot peening remains a critical method in metal treatment.
Types of Shot Peening Materials
Understanding the types of shot peening materials is essential for optimizing the shot peening process. Different shot materials provide unique benefits, affecting the efficiency and outcome of metal treatment. This section will explore three primary types: steel shots, aluminum shots, and glass beads. Each material has its characteristics, applications, and advantages. Choosing the right material is crucial for achieving desired results in surface enhancement.
Steel Shots
Steel shots are among the most widely used materials in shot peening. Their high density and hardness make them particularly effective in producing compressive residual stresses on metal surfaces. The size of the steel shot influences the peening's effect—larger shots deliver more energy but can cause deeper impressions, while smaller shots are less aggressive and provide a finer finish.
The benefits of steel shots include:
- Durability: Less prone to breakage compared to softer materials.
- Effectiveness: Efficient in creating surface changes that enhance fatigue resistance.
- Versatility: Suitable for a wide range of metals and applications.
Nevertheless, one must consider certain factors when opting for steel shots. These include potential surface distortion and the requirement of proper cleaning to prevent rust. Selecting the right balance is important for the specific application in metal treatment.
Aluminum Shots
Aluminum shots are lighter than steel and serve different purposes within the shot peening process. Their lower density results in less aggressive impacts, which can be beneficial for delicate components. Aluminum shots minimize the risk of damage while still creating favorable surface conditions.
The advantages of aluminum shots are:
- Reduced Weight: Ideal for use on lightweight alloys without additional strain.
- Gentle Abrasion: Produces a fine surface finish suitable for precision components.
- Corrosion Resistance: Less likely to corrode than steel shots, enhancing equipment longevity.
However, aluminum shots may not deliver the same level of residual stress as steel shots. In situations where more aggressive treatment is necessary, aluminum may not be the best choice. Careful consideration is needed based on the application requirements.
Glass Beads
Glass beads are commonly utilized for processes requiring a high-quality surface finish without excessive metal removal. They offer a unique approach, as they are suitable for both peening and cleaning operations. Their spherical shape ensures even distribution upon impact, which results in a more uniform surface treatment.
Key benefits of glass beads include:
- Surface Finish: Achieves a refined appearance, excellent for aesthetic applications.
- Minimal Material Removal: Preserves the dimensions of components during treatment.
- Safety: Non-toxic and environmentally friendly compared to metallic media.
On the flip side, glass beads might not induce deep compressive stresses compared to steel or aluminum shots. This limitation makes them best suited for specific scenarios, such as applications in the aerospace industry where visual quality is paramount.
Choosing the suitable shot material is vital for effective shot peening. The selected material should align with the application’s specific goals, whether for improving fatigue resistance, enhancing surface finish, or optimizing mechanical properties. By understanding the distinct characteristics each material offers, practitioners can make informed decisions that yield optimal results.
Shot Peening Techniques
Understanding the various shot peening techniques is crucial in the field of metal treatment. Each technique has unique benefits and considerations that impact overall effectiveness. These methods contribute not only to material strengthening but also to enhanced performance in different industrial applications. By exploring these techniques, practitioners gain insights into selecting the most suitable approach for their specific needs.
Air-Compressed Shot Peening
Air-compressed shot peening is one of the most common methods used in the industry. This technique involves propelling small metallic shots at high velocities using compressed air. The impact generated creates a compressive residual stress layer on the surface of the metal. This is significant in enhancing fatigue resistance.
The advantages of air-compressed shot peening include cost-effectiveness and ease of use. It is ideal for components with complex geometries. However, there are considerations to bear in mind, such as maintaining consistent shot velocity and ensuring optimal coverage. This approach can lead to greater metal longevity and reduced maintenance costs.
Centrifugal Wheel Peening
Centrifugal wheel peening utilizes a mechanical wheel to launch shots at high speeds. This method is efficient for treating large and heavy components, making it a favored choice in manufacturing sectors. The centrifugal force allows for a controlled flow of shots, ensuring uniform coverage over the surface.
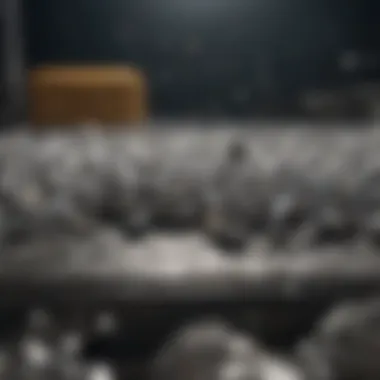
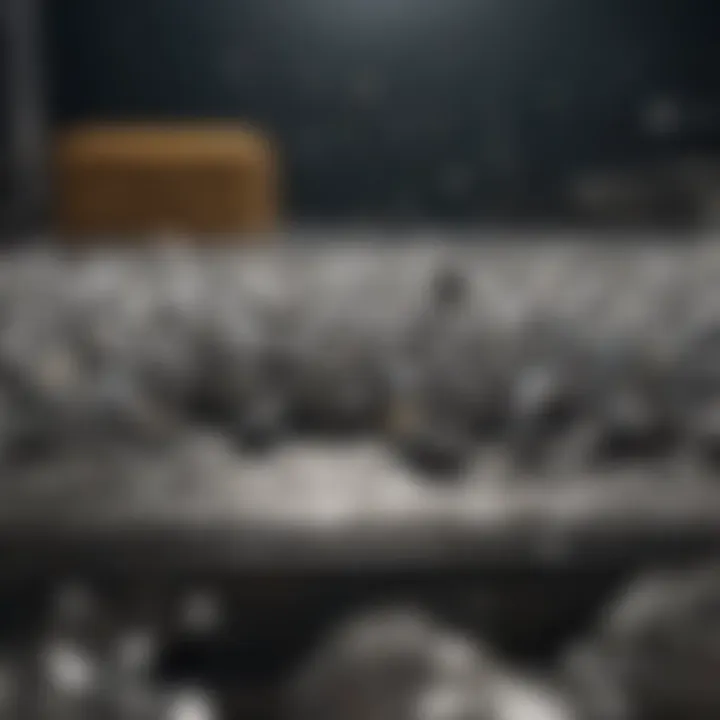
Key benefits of this technique include productivity and reduced processing times. It is particularly advantageous for parts that can withstand heavy impacts. However, practitioners must be cautious about controlling the peening intensity to avoid excessive deformation. The precision in controlling parameters is vital for achieving the desired surface finish without compromising material integrity.
Laser Peening
Laser peening is an advanced technique that employs high-energy laser beams to induce compressive stresses in metals. This method offers unique advantages, such as minimized risk of fatigue failure and the ability to treat components without heat distortion.
This technique is often used in critical applications, such as aerospace. It offers exceptional precision and control, allowing for treatment of intricate parts. However, it is also among the more expensive methods, which limits its use in certain sectors. The complexity of the equipment and need for skilled operation adds to the considerations for its application.
"The choice of shot peening technique directly influences the outcome of metal treatment, making it essential to match the method to the application requirements."
In summary, each shot peening technique has distinct characteristics. Air-compressed, centrifugal wheel, and laser peening each serve particular industrial needs. Understanding these differences enables professionals to implement the most effective strategy for enhancing metal performance and longevity.
Parameters Influencing Shot Peening
The process of shot peening is influenced by several crucial parameters. Each of these elements significantly affects the effectiveness and outcome of the treatment. Understanding these parameters can lead to improved performance and durability of metal components. Properly manipulating these factors can optimize the process, providing better results for a variety of applications.
Shot Size
Shot size is a fundamental factor in the shot peening process. It directly relates to the energy imparted onto the surface of the metal. Larger shots tend to deliver more energy, creating deeper compressive residual stresses. Conversely, smaller shots may provide a more uniform distribution of stress but at a lesser intensity. The selection of appropriate shot size hinges on the specific material and the desired outcome of the peening process. Generally, larger particles are effective for hard materials, while smaller ones are used for more delicate surfaces.
Peening Coverage
Peening coverage refers to the extent of surface area that the shot peening process impacts. Achieving adequate coverage ensures that all areas of the component receive the necessary treatment. It is typically measured as a percentage, with 100% coverage indicating complete treatment of the surface. Insufficient coverage can result in uneven stress distribution, potentially leading to premature failure. Therefore, it is essential to monitor the coverage, ensuring every part of the metal surface is peened appropriately, aligning with the goals of the treatment.
Impact Velocity
Impact velocity is another vital parameter in shot peening. This term defines the speed at which the shot impacts the metal surface. High impact velocities can increase the intensity of deformation and the associated compressive residual stresses in the material. However, excessively high velocities might lead to over-peening, which can damage the surface. Therefore, it is critical to maintain a balance in impact velocity, adjusting it according to the material properties and the desired mechanical performance outcomes.
To summarize, adjusting the shot size, ensuring sufficient peening coverage, and controlling impact velocity are all essential in tailoring shot peening to suit specific applications and material requirements.
Industrial Applications of Shot Peening
The industrial applications of shot peening represent a pivotal aspect of metal treatment. This process not only enhances the mechanical properties of various materials but also plays a significant role in extending the operational life of components across multiple industries. Understanding the specific benefits and applications of shot peening in industrial sectors provides valuable insights for professionals and researchers alike.
Aerospace Industry
In aerospace, shot peening is extensively utilized to improve the fatigue resistance of critical components such as turbine blades and landing gear. With the demanding operational conditions faced in aviation, parts are subject to high stress and fatigue, leading to potential failure if not properly treated. By imparting compressive residual stresses on the surface, shot peening reduces the likelihood of crack initiation and propagation.
Moreover, the aerospace sector often has strict regulations regarding safety and performance, which necessitates the use of reliable treatments like shot peening. The combination of enhanced durability and compliance with safety standards makes shot peening indispensable in the manufacturing of aircraft components.
Automotive Sector
In the automotive industry, the application of shot peening is critical for various components such as crankshafts, gears, and suspension parts. These elements must withstand high mechanical loads, vibrations, and impacts throughout their service life. Shot peening enhances the fatigue resistance of these components, which is essential for vehicle performance and safety.
Additionally, the automotive industry is currently shifting towards more lightweight materials for improved fuel efficiency. Shot peening helps maintain the strength and durability of these lighter materials, ensuring they can perform under stress. The ongoing advancements in shot peening technology further enable manufacturers to optimize the treatment process, resulting in better end products with reduced risks of failure.
Manufacturing of Heavy Equipment
The manufacturing sector for heavy equipment relies heavily on the benefits provided by shot peening. Equipment such as excavators, loaders, and bulldozers experience significant stress during operation. Shot peening enhances the surface properties of components like booms and arms, allowing them to absorb impacts better and reducing wear in harsh environments.
The longevity of heavy machinery is critical for maintaining operational efficiency in various industries, including construction and mining. With the high costs associated with equipment downtime and replacements, shot peening becomes a cost-effective solution. It improves the reliability of equipment, leading to higher productivity and lower overall maintenance costs.
Shot peening not only extends the life of components but also helps companies adhere to performance standards while reducing maintenance needs.
Overall, the industrial applications of shot peening are essential for enhancing material performance across sectors. Each segment benefits in unique ways, but the common thread is the enhancement of durability and operational efficiency, making shot peening an invaluable process in today’s manufacturing landscapes.
Standards and Regulations
The field of shot peening is guided by numerous standards and regulations, which are essential for ensuring safety, efficiency, and quality in industrial applications. These standards provide frameworks that govern the processes and outcomes of shot peening, especially in sensitive industries like aerospace and automotive. Adhering to these standards is crucial for gaining certification, maintaining competitiveness, and enhancing product reliability.
ASME Standards
The American Society of Mechanical Engineers (ASME) has developed guidelines that are widely recognized in the industry regarding shot peening processes. These standards specify requirements for equipment, material, and procedures. For instance, ASME B30.20 deals with the safety standards related to lifting equipment, which can include elements treated by shot peening. Compliance ensures operational safety and minimizes the risk of failure during use.
One significant benefit of following ASME standards is the promotion of uniformity across various practices within the industry. This consistency aids in quality control and ensures that products meet or exceed customer expectations. Additionally, ASME standards facilitate international cooperation by aligning practices to recognized norms, making it easier for companies to export products and enter global markets.
ISO Certifications
The International Organization for Standardization (ISO) offers certifications that are equally important in the context of shot peening. ISO 9001, for instance, focuses on quality management systems and is critical for organizations seeking to improve operational efficiency and product quality. This certification demonstrates that an organization is committed to meeting customer requirements and enhancing satisfaction.
ISO 13485 is another relevant standard, particularly in industries like medical device manufacturing, where shot peening may be employed. This standard emphasizes the need for a quality management system that is specific to medical devices, ensuring their safety and efficacy. By obtaining ISO certification, companies not only improve their credibility but also create trust with clients and regulators.
Challenges in Shot Peening
The process of shot peening, while widely recognized for its advantages, is not without its challenges. Understanding these challenges is essential for practitioners in the field. It helps to identify potential roadblocks in achieving optimal results from shot peening applications. By addressing these challenges, companies can enhance the effectiveness of shot peening, ensuring that its benefits are fully realized.
Material Selection
Choosing the right material for shot peening is critical. Different metals respond uniquely to the peening process. Steel shots, for example, are commonly used due to their durability and effectiveness, but they may not be suitable for all applications. The selection depends on factors such as the target material's hardness, the desired surface finish, and the intended use of the final product. For softer materials, aluminum shots might be more appropriate, as they reduce the risk of surface damage.
Furthermore, the size and shape of the shot can affect the peening outcome. A carefully chosen shot type can optimize the peening effect, while poor selection could lead to insufficient residual stress and surface improvement. Thus, engineers must weigh multiple factors in the selection process, considering both the properties of the shot material and the specifications of the component being treated.
Process Optimization
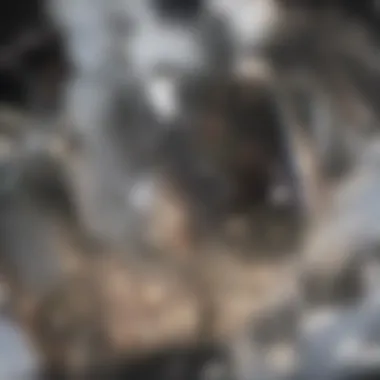
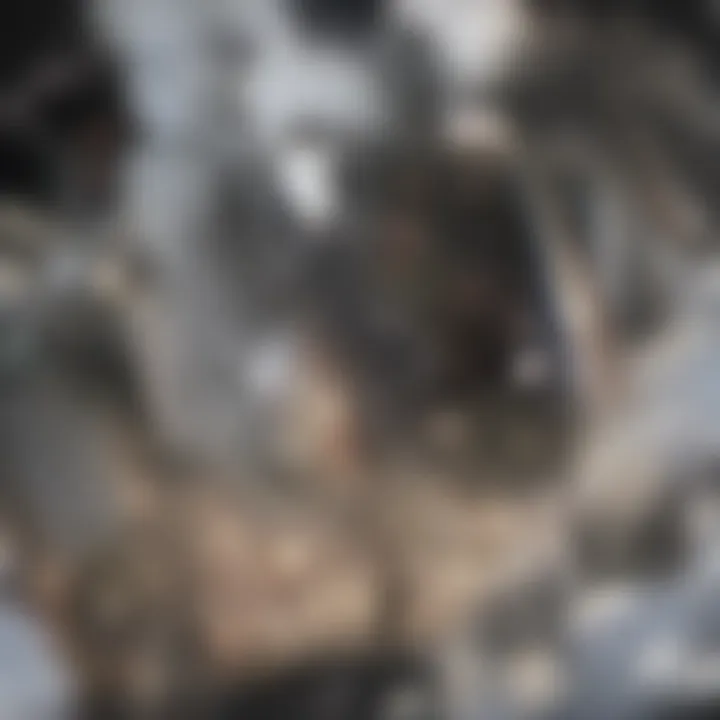
Optimizing the shot peening process is another significant challenge. The parameters of shot peening, including coverage, intensity, and velocity, must be fine-tuned for maximum effectiveness. Coverage refers to the area of the surface that is treated with the peening material. Inadequate coverage can lead to uneven treatment results, undermining the purpose of the process.
Intensity is another critical aspect. It typically relates to the impact energy of the shots on the surface. Higher intensity may increase material fatigue resistance, but it could also risk damaging delicate components. Thus, finding the optimal balance is essential to maintain the integrity of the workpiece.
"Optimizing the parameters of shot peening can significantly enhance the durability and performance of metal parts, necessitating a detailed understanding of the treatment process."
In addition to these parameters, the environment in which shot peening occurs can influence results. Dust, humidity, and surface contaminants must all be managed to prevent adverse effects on the shot and finished product. Overall, careful attention to process optimization is vital to overcoming these challenges and ensuring the efficacy of shot peening as a metal treatment.
Future Trends in Shot Peening Technology
The continuous evolution of shot peening technology plays a vital role in enhancing the performance and reliability of metal components. As industries move towards more complex designs and stricter quality standards, understanding future trends in shot peening becomes increasingly important. These trends reflect a drive for improved efficiency, precision, and integration of advanced technologies. Organizations will benefit from these developments by achieving better material properties, reducing operational costs, and meeting regulatory requirements.
Integration of Automation
The integration of automation in shot peening processes can significantly increase efficiency and consistency. Automated systems are capable of handling repetitive tasks with precision, reducing human error and variability. This means that shot peening can be performed at a higher throughput while maintaining quality control.
- Robotic Systems: Robotic arms can be programmed to execute shot peening in various angles and positions, enabling intricate geometries and complex parts to be treated effectively.
- Real-Time Monitoring: Utilizing sensors and electronic monitoring systems allows for real-time data collection during the peening process. This data can be analyzed to optimize parameters such as shot flow, impact velocity, and coverage.
- Predictive Maintenance: Automated systems can also facilitate predictive maintenance strategies by monitoring equipment health and performance. This ensures minimal downtime and maximizes productivity.
The benefits of automation in shot peening extend to a reduction in labor costs and improved safety. Workers can focus on higher-level tasks, while machines handle the repetitive and potentially hazardous activities.
Advancements in Simulation Models
Advancements in simulation models provide manufacturers with valuable tools to better understand and predict the effects of shot peening on materials. Simulation technology allows for comprehensive analysis and visualization of the shot peening process, offering insights into its impact on metal properties.
- Finite Element Analysis (FEA): FEA helps predict how components will respond to shot peening. This understanding allows for optimization of the process before physical implementation.
- Material Behavior Simulation: By simulating different types of metals and their responses to various peening conditions, engineers can tailor treatments to specific requirements and performance criteria.
- Cost-Effective Prototyping: With simulation models, companies can assess numerous scenarios without the need for extensive physical testing. This reduces costs associated with prototyping and can lead to faster time-to-market.
These advancements create a more data-driven approach to shot peening. The ability to visualize and manipulate variables within a virtual environment enhances decision-making processes and contributes to better overall results in metal treatment operations.
Understanding future trends in shot peening technology is essential for maintaining competitiveness in industries that rely on high-performance materials and components.
Comparative Analysis of Surface Treatments
The comparative analysis of surface treatments is crucial in understanding their unique impacts on material properties and performance. This exploration allows metal engineers and practitioners to make informed decisions regarding treatment methods that optimize durability and cost-efficiency for specific applications. While several surface treatment methods exist, shot peening stands out due to its versatility and effectiveness in enhancing fatigue resistance, which is a critical factor for the longevity of metal components.
Evaluating shot peening alongside other surface treatments highlights several important elements:
- Effectiveness: Shot peening effectively induces compressive residual stresses on the surface of materials, thus elevating fatigue strength. In contrast, methods like grinding or surface hardening may alter only surface characteristics without benefiting overall fatigue life.
- Cost-Effectiveness: The operational costs associated with shot peening are often lower compared to other methods like laser hardening or nitriding. This makes it a more economical choice for large-scale applications where budget constraints are significant.
- Adaptability: Shot peening can be performed on various materials and geometries, making it suitable for a wide range of industries, including aerospace, automotive, and heavy machinery. Other treatments may be limited to specific metals or complicated shapes.
- Minimal Distortion: Due to its controlled process, shot peening typically results in minimal distortion of the component, unlike some thermal-based methods that could cause warping or changes in properties.
Shot Peening vs. Other Methods
When comparing shot peening to other surface treatments, it is important to note the specific operational mechanisms and benefits:
- Plating and Coating: While plating or coating can protect against corrosion and wear, they may not significantly enhance the fatigue properties of metals. Shot peening, on the other hand, improves component strength under cyclic loading.
- Hardening Processes: Processes like carburizing or nitriding create hard layers on the surface but can lead to brittleness. Shot peening, however, maintains a balance between hardness and ductility, crucial for enduring dynamic loads.
- Surface Finishing Techniques: Techniques like grinding provide a smooth surface finish, which is ideal for aesthetic purposes but may not address underlying issues like fatigue. Shot peening enhances sub-surface strength, which is essential for parts under stress.
In summary, while various surface treatments offer specific advantages, shot peening often provides a more balanced solution for enhancing the fatigue resistance and durability of metallic components.
Cost-Benefit Considerations
When evaluating the cost-benefit aspects of shot peening compared to other surface treatments, several factors need to be considered:
- Initial Investment: The initial setup for shot peening equipment can be significant, but ongoing costs are lower than for some treatments. Techniques like ion implantation or laser surface treatment often come with high operational costs that may not justify the benefits for every application.
- Longevity of Benefits: The improvements gained from shot peening often outlast those from surface coatings, which can wear over time. The enduring benefits of shot peening make it a preferable investment for critical components subjected to high-stress environments.
- Versatility in Applications: The ability of shot peening to be applied across various industries adds to its cost-effectiveness. It can be used on diverse metal types without requiring unique setups, thus reducing expenses over time.
- Regulatory Compliance: Many industries face strict regulations regarding surface treatments, particularly in aerospace and automotive. Shot peening adheres well to these standards, potentially reducing costs associated with re-certification and compliance for other treatments.
Best Practices for Implementing Shot Peening
Implementing shot peening effectively requires an understanding of various best practices that optimize the treatment process. These practices not only improve the efficiency of the process but also ensure that the desired effects on metal fatigue and durability are achieved. By adhering to specific guidelines, manufacturers can enhance the performance of components subjected to shot peening.
Pre-Inspection Requirements
Before initiating the shot peening process, a thorough pre-inspection is crucial. The pre-inspection phase helps identify potential issues that could impact the treatment results. Here are some key aspects to focus on:
- Material Assessment: Understand the type of metal being treated. Different metals react differently to shot peening, requiring tailored approaches.
- Surface Condition: Inspect the surface for defects such as scratches, rust, or corrosion. A clean surface is critical for effective peening.
- Geometric Considerations: Evaluate the component's shape and size. Complex geometries may require specialized setups to ensure uniform peening coverage.
- Existing Residual Stresses: Analyze any pre-existing stresses in the material. Understanding these can help optimize the shot peening parameters.
In this stage, creating a detailed report documenting the findings is important. This will aid in monitoring the treatment and ensuring traceability.
Post-Treatment Evaluation
After the shot peening process is complete, a thorough post-treatment evaluation is necessary to assess its effectiveness. This evaluation helps confirm that the treatment met its intended goals and identifies any areas for improvement. Important considerations include:
- Visual Inspection: Conduct a visual assessment to check for any visible defects introduced during peening. Look for indications of over-peening or surface damage.
- Surface Hardness Testing: Perform tests to measure the hardness of the surface. Comparing pre- and post-treatment hardness readings can indicate the effectiveness of the peening process.
- Residual Stress Measurement: It is important to evaluate the residual stress profile post-treatment. Techniques such as X-ray diffraction can provide detailed insights into stress distributions.
- Documentation of Findings: Record all observations and measurements thoroughly. This documentation is crucial for future reference and continuous improvement.
By following these best practices, organizations can effectively implement shot peening and achieve desired enhancements in material performance. Proper attention to detail in both pre-inspection and post-treatment evaluations significantly reduces the risk of operational failures and ensures longevity of metal components.
Finale
The conclusion section of this article is crucial as it encapsulates the significant themes discussed throughout. A clear understanding of shot peening and its applications can lead to tangible benefits in various industries. The importance of this topic lies not only in recognizing its mechanical impact on materials but also in appreciating the broader implications for industrial processes.
Summary of Key Points
To summarize, shot peening is a crucial treatment method that enhances the mechanical properties of metals. Here are the key points covered in this article:
- Definition and History: The origins and development of shot peening were explored, emphasizing its growth as a vital metal treatment process.
- Mechanics of Shot Peening: Detailed information on the principles that govern shot peening, including deformation mechanisms and residual stress development.
- Benefits: The article highlighted how shot peening improves metal fatigue resistance and enhances material strength.
- Materials and Techniques: Various materials used for shot peening were discussed, such as steel shots and glass beads, along with the different techniques employed in the process.
- Industrial Applications: Applications in sectors like aerospace and automotive were analyzed, showing the breadth of shot peening usage in industry.
- Standards and Challenges: Important regulations and the challenges faced in material selection and process optimization were examined, providing context for best practices in implementation.
- Future Trends: The integration of automation and advancements in simulation models indicate a progressive outlook for shot peening technology.
Final Remarks on Future Research Directions
As industries evolve, the need for innovation in shot peening practices becomes even more essential. Future research should focus on the following directions:
- Advanced Materials: Investigating new materials for shot peening can improve efficiency and effectiveness in applications where traditional materials fall short.
- Optimized Processes: Further studies are needed to fine-tune the parameters influencing shot peening, ensuring maximum effectiveness in treatment processes across varied applications.
- Sustainability Initiatives: Addressing environmental concerns associated with traditional shot peening methods will become increasingly relevant. Research into more sustainable practices can contribute to a greener manufacturing approach.
- Digital Technologies: Integration of digital technologies and artificial intelligence in the shot peening process can facilitate better monitoring and control, enhancing quality assurance.