An In-Depth Analysis of Ceramic Cement: Properties and Future Directions
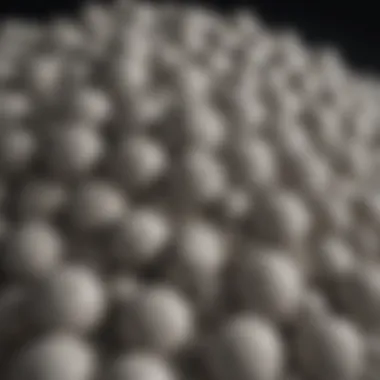
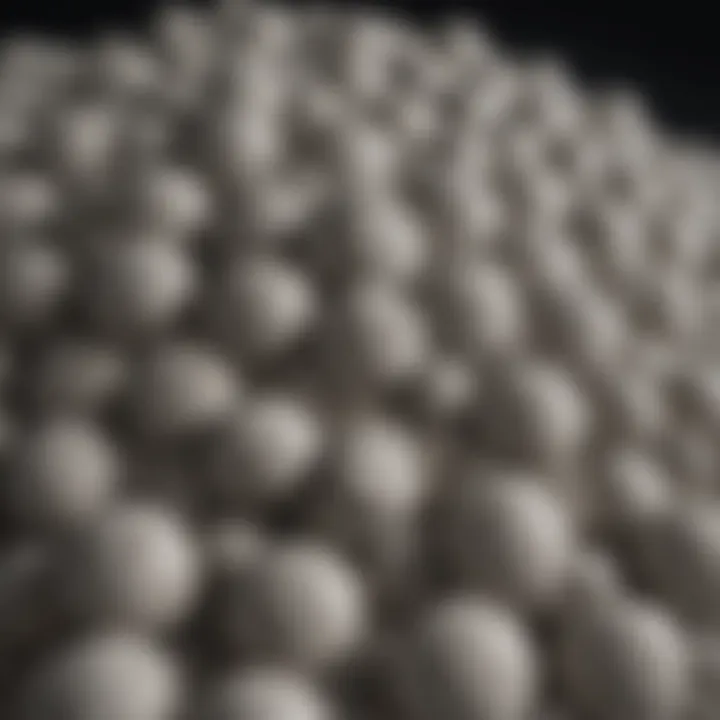
Intro
Ceramic cement, a material that combines the characteristics of both ceramics and cement, has emerged as a versatile solution in various industries. Its unique properties make it a subject of much interest among students, researchers, educators, and professionals. This article will explore the multifaceted aspects of ceramic cement, focusing on its distinct qualities, diverse applications, and potential future developments. By understanding this material, one can appreciate its role in contemporary science and engineering.
Key Points
- Understanding the chemical composition of ceramic cement is crucial.
- Mechanical characteristics and advantages over traditional materials will be analyzed.
- The production processes will be described to highlight challenges and methodologies.
- Future directions and innovations in ceramic cement research will also be discussed.
The focus on ceramic cement is not simply academic. Its implications on construction, sustainability, and performance open avenues for further research and application. Therefore, this analysis will provide insights that are not only relevant but also essential for those engaged in engineering and material science.
Methodologies
A comprehensive understanding of ceramic cement requires an exploration into the methodologies applied in its research and development. The evaluation of this material encompasses various research techniques and technological tools that enable scientists to analyze its properties and applications effectively.
Description of Research Techniques
Research in ceramic cement involves both qualitative and quantitative techniques. Techniques such as X-Ray Diffraction (XRD) and Scanning Electron Microscopy (SEM) are commonly employed to analyze the microstructure and crystalline properties of this material. Moreover, mechanical testing methods include flexural strength testing and compressive strength tests, which help in ascertaining the performance of ceramic cement under various conditions. The integration of theoretical frameworks with empirical data guides the ongoing development and enhancement of ceramic cement.
Tools and Technologies Used
Modern research leverages advanced tools and technologies for the synthesis and analysis of ceramic cement. Some notable tools include:
- X-Ray Diffraction (XRD) for phase analysis.
- Scanning Electron Microscopy (SEM) for surface characterization.
- Differential Thermal Analysis (DTA) for thermal stability assessment.
- Rheometers to evaluate the flow properties of cement mixtures.
These instruments facilitate a deeper insight into the material's behavior and enhance the understanding of its composite nature, which is essential for future applications.
Discussion
The exploration of ceramic cement extends beyond its immediate characteristics; it requires contextualizing its findings within the broader spectrum of material science.
Comparison with Previous Research
When comparing ceramic cement with traditional materials like Portland cement, it is crucial to highlight the differences. Previous research indicates that ceramic cement often exhibits superior durability, resistance to chemical attack, and lower shrinkage rates. Such traits champion its use in demanding applications, where reliability is paramount. Academic studies often reveal how ceramic cement can outperform conventional materials in critical conditions.
Theoretical Implications
The theoretical implications stem from understanding how ceramic cement integrates with concepts from both ceramic and cement science. The bonding mechanisms and phase interactions that occur during curing are of particular interest. This knowledge bolsters predictive models that inform engineers about material behaviors under various stressors, lending significant insight into future design applications.
"Understanding the interplay between different material sciences enriches the knowledge base for compound materials like ceramic cement, paving the way for innovative applications."
Understanding Ceramic Cement
Ceramic cement is a material that has garnered significant attention within various fields, especially in construction and engineering. It presents unique attributes that differentiate it from traditional cements, offering a range of benefits. Its properties, such as high strength, durability, and thermal resistance, make it a preferred choice in diverse applications. Moreover, understanding ceramic cement involves recognizing its chemical makeup and the historical context in which it has evolved.
This section aims to provide clarity on what ceramic cement is and trace its historical development. Such comprehension is essential for students, researchers, and professionals who seek to exploit the material's potential, whether in innovation or practical applications.
Definition of Ceramic Cement
Ceramic cement can be defined as a type of cement that incorporates ceramic materials into its formulation. This combination aims to enhance the mechanical and thermal properties compared to conventional cements. The primary components often include silica, alumina, and various oxides, which together form a strong matrix upon curing. Ceramic cement typically exhibits lower porosity, making it ideal for applications that require chemical resistance and lower moisture absorption.
In practical terms, ceramic cements are used in environments that demand superior performance under stress. They are often found in specialized construction scenarios, aerospace components, and biomedical devices.
Historical Development
The history of ceramic cement is rooted in the broader context of cement and ceramic technology. Initially, traditional cements, such as Portland cement, dominated the construction landscape due to their widespread availability and ease of use. However, as industries began to prioritize durability and performance, the need for high-efficiency materials emerged.
During the latter half of the 20th century, advancements in material science led to the exploration of ceramic composites. Early iterations of ceramic cement aimed to improve the performance of construction materials by incorporating elements that allowed for better heat resistance and lower expansion rates. Researchers found that the use of ceramics within cementitious systems not only enhanced performance but also extended the range of possible applications.
Today, ceramic cement continues to evolve. Innovations in production technology and formulations contribute to superior material properties. As industries increasingly focus on sustainability and performance, understanding both the definition and historical context of ceramic cement becomes crucial. It equips professionals to leverage advances in material science effectively.
"Ceramic cements are not just materials; they represent the intersection of science and engineering, pushing the boundaries of what is possible in construction and beyond."
Chemical Composition
The chemical composition of ceramic cement plays a crucial role in determining its properties and performance across various applications. Understanding the specific elements that constitute ceramic cement allows researchers and engineers to tailor its characteristics to meet the demands of different industries. From mechanical strength to thermal stability, the composition can significantly influence the behavior of ceramic cement in real-world scenarios. Key elements such as silica and alumina contribute to the durability and resilience of the material, making it essential to delve into these components to fully comprehend their impact.
Basic Components
Ceramic cement primarily consists of various oxides, with silica, alumina, and calcium oxide being the dominant ones. Silica, often derived from quartz, serves as the primary glass-forming oxide and influences the strength and hardness of the cement. Alumina enhances the thermal properties and provides better strength at high temperatures. Calcium oxide, generally sourced from limestone, contributes to the binding properties, helping unify the entire cement matrix.
Moreover, other elements such as magnesia and sodium oxide can also play a role. Magnesia may improve the thermal shock resistance, while sodium oxide can modify the melting point, which is essential during the firing process. This interplay of components is vital, and the right balance can lead to superior performance in high-stress environments.
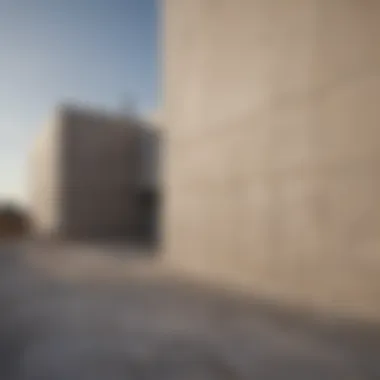
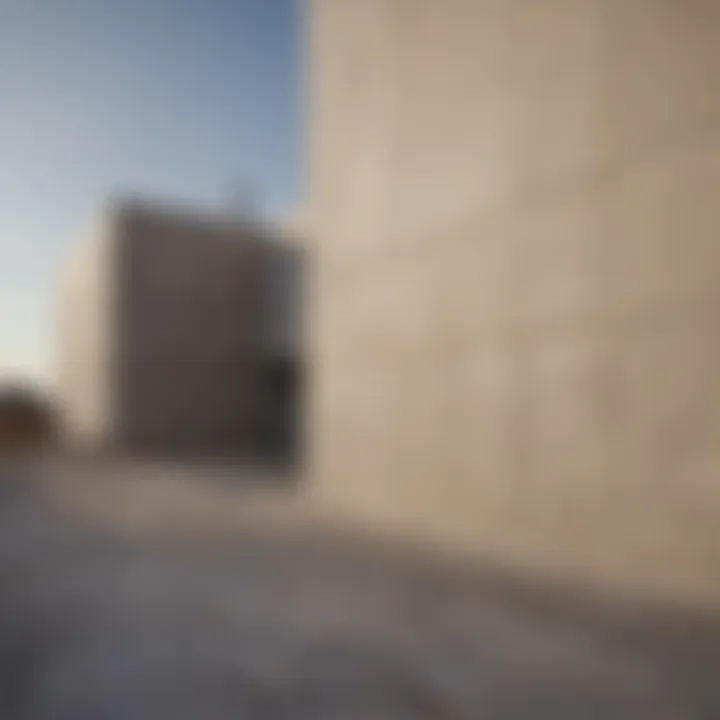
Additives and Modifiers
In addition to the basic components, various additives and modifiers are employed to enhance the performance of ceramic cement. These include plasticizers, which improve workability, making it easier to mix and apply. Other common additives include fibers, which can enhance tensile strength and reduce brittleness. Fibers such as nylon or carbon have gained popularity for this purpose.
Another important category of modifiers consists of pozzolans. These materials can react with the calcium hydroxide present in the cement, forming additional cementitious compounds. Examples include fly ash and slag, which not only improve strength but also contribute to sustainability by utilizing industrial by-products.
The precise formulation of ceramic cement, integrating both its basic components and additives, is key. This formulation directly affects its durability, workability, and overall performance in specific applications. Understanding these modifiers and their functions helps in making informed choices when selecting materials for engineering projects or research purposes.
The composition of ceramic cement dictates its compatibility with various applications, and innovation in formulations continues to push the boundaries of what's possible in material science.
Properties of Ceramic Cement
The properties of ceramic cement play a critical role in determining its applicability across various fields. Understanding these properties helps in evaluating the material's performance, enhancing its usage in specific scenarios. Ceramic cement is not only made for structural integrity but also for specific reactions to thermal and chemical influences. The precise attributes offer benefits that often surpass those of traditional cements.
Mechanical Properties
Mechanical properties are fundamental to the performance of ceramic cement. They characterize how the material responds under different loads and conditions. These properties include tensile strength, compressive strength, and flexural strength.
Tensile Strength
Tensile strength refers to the resistance of a material to being pulled apart. This aspect is very important in applications where the ceramic cement is subjected to tension forces. A high tensile strength ensures that the material can withstand significant stresses without failure. This quality makes ceramic cement favorable in settings where durability and reliability are critical.
One key characteristic of tensile strength is its relationship with the microstructure of the ceramic. Aspects such as the grain structure and bonding significantly impact the tensile capacity. While ceramic cements typically exhibit lower tensile strength compared to metallic counterparts, their ability to function effectively in tension-bearing roles is highly valued.
A unique feature of high tensile strength is its role in enhancing the overall lifecycle of the structures. However, a disadvantage may emerge in applications with constant shock loads, where sudden forces can lead to fractures despite high tensile ratings.
Compressive Strength
Compressive strength defines a material's ability to withstand axial loads without crushing. In construction, it is often the most critical property. High compressive strength in ceramic cement signifies that it can support heavy loads and maintain structural integrity over time.
Compressive strength is a prominent feature of ceramic materials, making them widely accepted in infrastructure projects. Its high values ensure that buildings and other structures can resist the weight they bear.
However, while ceramic cement can handle compression well, its brittleness can lead to catastrophic failure under sudden impacts. This highlights the need for careful consideration in applications where shock resistance is required.
Flexural Strength
Flexural strength refers to the capacity to withstand bending forces. It becomes particularly relevant in structures that face mixed loads during their lifecycle. This property indicates how well the ceramic cement can deform under load without cracking.
Flexural strength combines the benefits of both tensile and compressive strengths. It allows for designs that involve arches and beams made from ceramic cement. Such designs leverage this strength, allowing for innovative architectural solutions.
The unique advantage of high flexural strength is its contribution to lightweight design. It enables thinner sections of material while maintaining structural viability. On the downside, the bending performance can decrease when exposed to high temperatures or chemical environments.
Thermal Properties
Thermal properties dictate how ceramic cement reacts to temperature changes. Understanding these attributes is crucial for applications in environments with extreme temperatures.
Thermal Conductivity
Thermal conductivity measures how well a material can conduct heat. For ceramic cement, a specific thermal conductivity is beneficial in applications where heat insulation is needed. Low thermal conductivity indicates good insulation properties, which both reduce energy costs and maintain desired temperatures.
The effective insulating nature of ceramic cement allows for its use in various thermal applications, such as in industrial furnaces or passive buildings, where energy efficiency is key. However, variations in thermal conductivity among different ceramic compositions can limit some uses.
Thermal Expansion
Thermal expansion refers to how much a material expands when subjected to temperature increases. It is critical in environments with significant temperature fluctuations. Ceramic cement usually has a low thermal expansion coefficient, making it stable under thermal stress.
This stability is a desired feature in construction applications that endure temperature variations. However, if other materials in a composite structure do not share similar expansion properties, it may lead to stress concentrations.
Chemical Resistance
Chemical resistance is the ability of ceramic cement to withstand reactions with chemicals in its environment. This property is indispensable for applications in aggressive environments, where exposure to acids, bases, and harsh solvents can occur.
Ceramic cement stands out for its resistance to chemical attacks, unlike other common building materials. This feature expands the material's usability in industries such as chemicals and pharmaceuticals.
In essence, the properties of ceramic cement—ranging from mechanical facets like tensile, compressive, and flexural strengths to thermal attributes and chemical resistances—establish its prominence in numerous applications. Each characteristic not only details the performance under various conditions but also indicates areas requiring careful consideration in engineering and application.
Production Processes
The production processes of ceramic cement play a critical role in determining its final properties and performance. Understanding these methods is essential for enhancing production efficiency and product quality. Each technique employed in manufacturing contributes uniquely to the material characteristics and, consequently, its applications across various industries.
Manufacturing Techniques
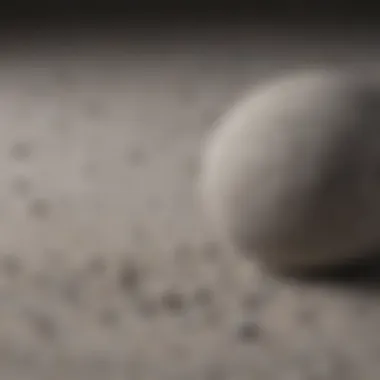
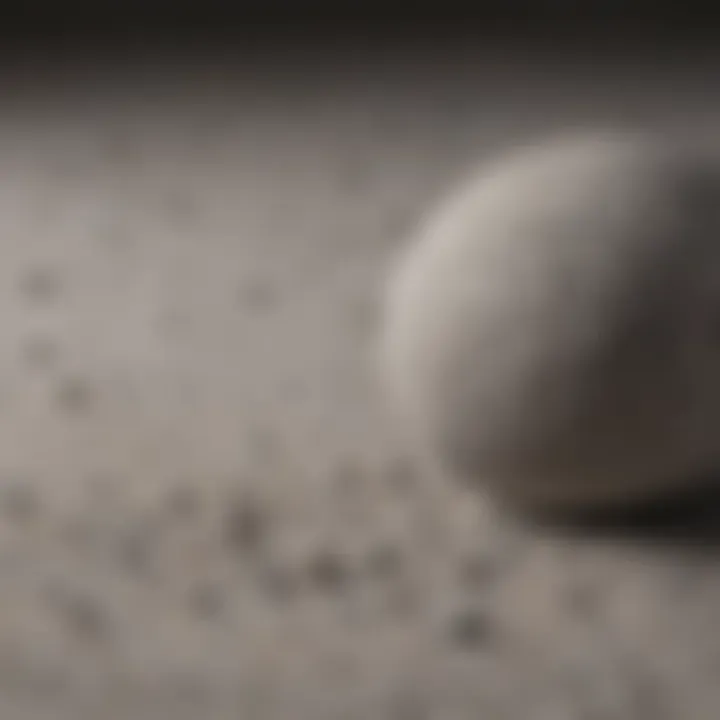
Casting
Casting is one of the oldest manufacturing techniques used for ceramic cement. This method involves pouring a liquid mixture of the ceramic material into molds where it solidifies. The key characteristic of casting is its ability to produce intricate shapes and designs with high precision. This feature makes it a popular choice in sectors that require complexity in design, such as art and sculpture.
Among the advantages of casting is the reduction of waste material, as the process can be tailored to exact dimensions. However, one disadvantage is the lengthy curing time, which can delay large-scale production. The resulting ceramic pieces typically exhibit superior surface finishes, making casting an appealing route for many applications.
Spray Drying
Spray drying is a process that converts a liquid suspension into a dry powder. After preparation, the liquid mixture is sprayed into a hot gas stream. The water evaporates quickly, leaving behind fine ceramic particles. A key characteristic of spray drying is its efficiency, enabling high-volume production of ceramic powders.
This technique is beneficial because it allows for a uniform particle size distribution, which is crucial for consistent performance in applications. However, the process requires careful control of parameters such as temperature and pressure to avoid defects in the final product. The rapid processing speed of spray drying contributes significantly to reducing overall production time.
Sintering
Sintering is a thermal process where compacted powders are heated below their melting point. This technique leads to the densification of the ceramic material, enhancing its mechanical properties. The key aspect of sintering is its ability to improve strength and reduce porosity effectively.
Sintering is favored because it can significantly enhance the durability and performance of ceramic cement. However, the process may require high temperatures, which can increase energy consumption during production. Understanding the sintering conditions, such as time and temperature, is essential for optimizing the final properties of the ceramic product.
Quality Control Measures
Quality control in the production of ceramic cement is paramount to ensure that the final products meet the required standards and specifications. This involves a series of checks and tests performed throughout the production process.
Regular testing of raw materials is essential. Each batch should be analyzed for consistency in composition and properties. In-process inspections can catch discrepancies early, preventing defects in final products. Additionally, post-production tests, such as mechanical stress tests and thermal resistance evaluations, determine if the cement meets the expected performance criteria.
Adopting standardized testing methods ensures that manufacturers can maintain quality and improve customer satisfaction. Furthermore, a robust quality assurance program can lead to innovations in production techniques, ultimately advancing the overall field of ceramic cement.
Applications of Ceramic Cement
The applications of ceramic cement are extensive and diverse, covering various fields such as construction, aerospace engineering, and biomedical engineering. Understanding these applications helps highlight the significant impact ceramic cement has on modern technology and infrastructure. Each application addresses specific requirements and brings unique advantages, showcasing ceramic cement's adaptability.
Construction Industry
Tile Adhesives
Tile adhesives made from ceramic cement are pivotal in the construction industry. They offer strong bonding capabilities between tiles and substrate surfaces, which is essential for durability. One key characteristic is their high shear strength, enabling the installation of tiles in various environments, including moist areas like bathrooms and kitchens. The unique feature of these adhesives is their quick setting time, allowing for rapid project completion. However, one disadvantage is their potential brittleness, which may lead to cracking under extreme conditions if not applied correctly.
Structural Components
Ceramic cement is also utilized in the creation of structural components, such as beams and columns. These components benefit from the material's excellent compressive strength, positioning ceramic cement as a reliable choice for load-bearing applications. The primary advantage is its resistance to environmental degradation, making it suitable for both indoor and outdoor structures. One unique feature is its lightweight nature, which reduces the overall weight of the construction. However, a drawback is the initial cost of production, which can be higher compared to traditional concrete.
Aerospace Engineering
Reinforcement Materials
In aerospace engineering, ceramic cement serves as a reinforcement material for various structures. Its primary role is to enhance the mechanical properties of composite materials used in aircraft. One notable aspect is its ability to withstand high temperatures, making it suitable for parts subjected to extreme conditions. This unique feature provides enhanced safety and performance. Despite its benefits, it can be more expensive than other traditional materials, limiting its widespread use in some applications.
Heat Shields
Ceramic cement is critical in the production of heat shields, particularly for spacecraft. These shields protect vehicles from intense heat during atmospheric re-entry. A key characteristic of ceramic heat shields is their thermal stability. This stability ensures the integrity of the spacecraft under high thermal stress. The unique feature of using ceramic cement in heat shields is the low thermal conductivity, which effectively insulates the interior of the spacecraft. However, the fragility of the material can raise concerns during the installation and handling processes.
Biomedical Applications
Bone Implants
Ceramic cement is increasingly being used in biomedical applications, specifically in the creation of bone implants. The material is known for its biocompatibility, allowing for successful integration with human tissue. A vital characteristic is its osteoconductivity, promoting bone growth around the implant. The primary advantage of using ceramic cement for bone implants lies in its ability to mimic natural bone properties. Still, a disadvantage is the potential for stress shielding, which may weaken surrounding bone over time.
Drug Delivery Systems
Another significant application is in drug delivery systems. Ceramic cement can be formulated to release therapeutic agents over an extended period. One important aspect of these systems is their controllable release mechanism, allowing for tailored treatment options. The unique feature is its ability to combine mechanical support with drug delivery, which is vital in complex therapies. However, the challenge lies in ensuring the stability and bioavailability of the drugs used in these formulations.
"The applications of ceramic cement illustrate its versatility and potential to address complex engineering challenges across diverse fields."
As the demands for innovative materials grow, the applications of ceramic cement will continue to expand, driving advancements in technology and material science.
Challenges in the Use of Ceramic Cement
The use of ceramic cement presents a variety of challenges that must be understood for its effective application. In this section, we will explore the two principal challenges: brittleness and fracture, and the cost of production. Each of these factors can significantly influence the overall viability and effectiveness of ceramic cement in various applications.
Brittleness and Fracture
Ceramic cement is known for its exceptional strength but also for its brittleness. This means that while it can withstand high compressive forces, it can fracture under tension or impact. The tendency to fail in a brittle manner is a critical drawback. When structure is subjected to loading, the internal stresses can cause sudden breaks, leading to failure without much visible warning.
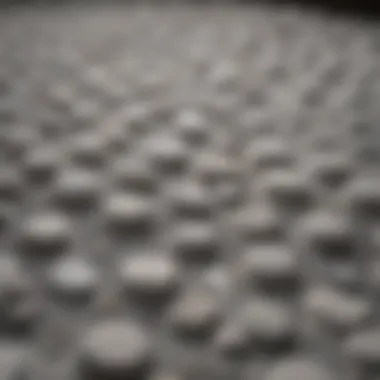
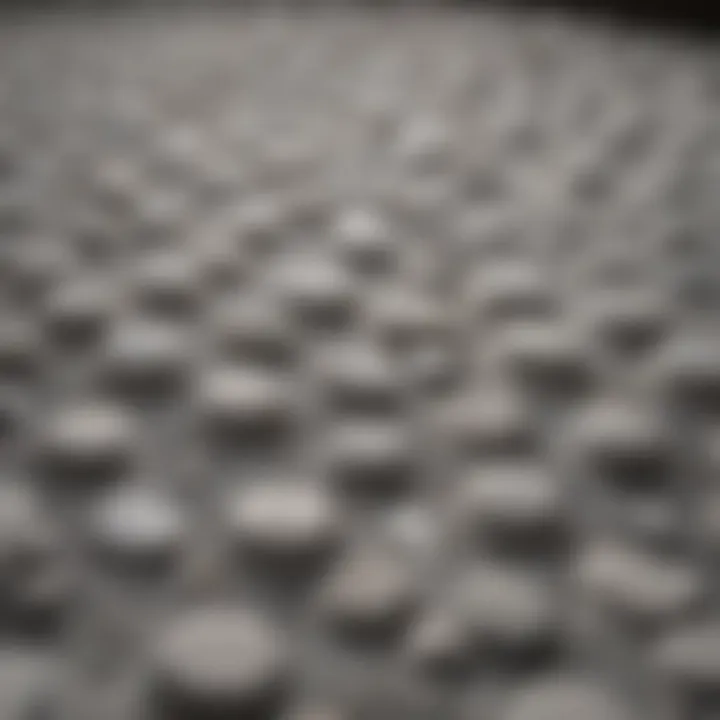
The brittle nature of ceramic cement limits its use in certain structural applications, especially in areas where flexibility is required. For instance, in the construction industry, if ceramic cement is utilized in regions that experience vibrations or dynamic loads, there is a heightened risk of cracking. This limitation encourages researchers to explore additives or composite materials that could enhance ductility while retaining the advantageous properties of ceramic cement.
Moreover, understanding the mechanisms of fracture can aid in the development of better formulations. The incorporation of reinforcement materials or adjustments in microstructure may help mitigate brittleness and allow for more versatile applications. In summary, while ceramic cement has merit, its brittleness remains a significant barrier to broader utilization.
Cost of Production
The cost of producing ceramic cement is another notable challenge. High-quality ceramic materials often require specialized extraction and processing techniques. Raw materials, including alumina and silica, must be sourced, processed, and often subject to high-temperature treatments, all of which contribute to increased costs.
Additionally, the advanced methodologies required for the manufacturing processes, such as sintering, can be energy-intensive. The capital investment for equipment and technology is substantial, making it more expensive than some traditional cement materials. This expense can limit its adoption in cost-sensitive markets.
To address these concerns, research is focusing on optimizing production methods. For instance, exploring alternative raw materials or reducing energy consumption during manufacturing could make ceramic cement more economically viable.
Ultimately, addressing the cost of production is essential for the widespread adoption of ceramic cement in various industries.
Understanding these challenges is vital for engineers and developers who wish to harness the potential of ceramic cement while addressing its limitations in real-world applications.
Recent Research Trends
Research in ceramic cement has expanded significantly over recent years, highlighting its versatile nature and potential applications across various industries. This trend is essential because it not only enhances our understanding of ceramic cement but also paves the way for innovations that could redefine its utilization in modern engineering and construction. The intricate balance between its properties, applications, and the ongoing challenges emphasizes the need for continuous advancements in this field.
Innovations in Formulations
Recent research has explored numerous innovations in formulations of ceramic cement. These innovations are often aimed at enhancing performance while maintaining sustainability. Researchers are delving into alternative raw materials, such as recycled aggregates and industrial by-products, to develop ceramic cement that is not only high-performing but also environmentally friendly. This shift towards using alternative materials has numerous benefits:
- Cost-Effectiveness: Utilizing by-products can significantly reduce material costs.
- Resource Efficiency: Making use of waste materials effectively lowers the demand for virgin resources.
- Enhanced Performance: Certain additive materials can improve characteristics like strength and durability.
Furthermore, scientists are investigating how nano-materials can enhance the properties of ceramic cement. Nano-silica, for example, has shown potential in increasing tensile and compressive strength, thus making it suitable for a wider range of applications. This line of research could lead to the development of ultra-high-performance ceramics that outperform traditional materials on multiple fronts.
Sustainability Considerations
The focus on sustainability in recent research trends has been pivotal. As industries become more conscious of their environmental impact, the demand for sustainable materials is rising. In the context of ceramic cement, this consideration leads researchers to explore:
- Reduction of Carbon Footprint: Innovations are being made to reduce the carbon emissions associated with the production of ceramic cement. For example, the utilization of lower firing temperatures in the manufacturing process can decrease energy consumption significantly.
- Circular Economy Practices: Emphasis is placed on developing ceramic cement that can be recycled at the end of its life cycle. This not only conserves resources but helps minimize landfill waste.
- Bio-based Additives: The exploration of bio-based materials as additives represents a significant step forward in aligning ceramic cement with sustainability goals. These materials can offer unique properties while being more environmentally benign compared to traditional chemical additives.
"The integration of sustainability in the formulation of ceramic cement not only advances the technology but also addresses pressing environmental issues."
By prioritizing sustainability in research, the ceramic cement industry is working to ensure its future is not only technologically advanced but also ecologically responsible.
Future Directions
The future of ceramic cement is marked by innovative advancements and a growing recognition of its practical applications. As industries continue to demand materials that offer outstanding performance and sustainability, ceramic cement is positioned to play a pivotal role. Understanding the future directions for this material not only highlights potential benefits but also underscores the importance of continued research and development.
Emerging Technologies
Emerging technologies in ceramic cement are largely defined by the integration of smarter production techniques. The use of automation and advanced computational methods in the manufacturing process can lead to better consistency and quality. Notably, 3D printing technology is reshaping the landscape of ceramic cement applications in construction and biomedical fields.
Furthermore, nanomaterials are being increasingly researched to enhance the properties of ceramic cement. Incorporating nanoparticles can potentially improve strength and durability while maintaining lightweight characteristics. This advancement could lead to new formulations that outperform existing products.
Research into bioactive ceramic cement is also progressing. These materials can interact with biological systems, making them suitable for applications in medicine, such as bone grafts and drug delivery systems. By focusing on the synthesis and functionalization of these bioactive ceramics, researchers aim to bridge the gap between material science and medicine.
Potential Market Growth
The potential market growth for ceramic cement is remarkable. As sectors like construction, aerospace, and biomedical engineering continue to expand, the demand for high-performance materials will likely increase.
In the construction industry, ceramic cement's application in tile adhesives and structural components presents significant opportunities. The push for sustainable and energy-efficient materials aligns with the properties of ceramic cements, fostering growth in this sector.
Moreover, the increasing awareness of material innovations presents a ripe opportunity for composite materials that integrate ceramic cement. This trend involves hybrid solutions that combine properties from different materials, further diversifying applications and markets.
According to recent studies, the global ceramic cement market is anticipated to grow steadily within the next decade. Factors driving this growth include:
- Advancement in technology and manufacturing processes.
- Stricter regulations on building materials and sustainability.
- Increased investment in research and development.
The continued evolution of ceramic cement in response to technological advancements and market needs will be a crucial determinant in its future success.
In summary, the future directions for ceramic cement indicate a landscape rich with potential and innovation. By harnessing emerging technologies and capitalizing on market growth opportunities, industries are poised to benefit from the unique characteristics and capabilities of ceramic cement.
Epilogue
In this article, we explored various dimensions of ceramic cement, a material that holds significant promise across multiple industries. This conclusion synthesizes the key findings and emphasizes the essential role ceramic cement can play in current and future applications.
Ceramic cement's unique properties, including its mechanical durability and thermal stability, position it as an essential material in fields such as construction, aerospace, and biomedicine. As highlighted, it offers numerous advantages over traditional materials. It is imperative to acknowledge that the ongoing developments in production processes, such as advanced manufacturing techniques, contribute to enhancing its practical viability.
Moreover, recent research trends focusing on sustainability and formulation innovations pave the way for enhanced adaptability of ceramic cement. These advancements not only address the challenges associated with cost and brittleness but also open the door for innovative applications tailored to meet market demands.
"Understanding the future trajectory of ceramic cement can aid stakeholders in making informed decisions for investments in research and material development."
In summary, ceramic cement's versatility and potential market growth indicate a promising future. As industries continue to seek more efficient and durable materials, ceramic cement remains a key player ready to adapt and innovate, ensuring its relevance in the evolving landscape of material science. Through comprehensive exploration, we have established its significance and left open opportunities for further inquiry and development.